Selecting the right motor seal is crucial for ensuring the longevity and performance of your machinery. Motor seals serve as vital components that prevent leakage and contamination in rotating shafts within motors. Choosing the right seal involves understanding its application, material suitability, and operational environment. Here’s how you can make an informed choice.
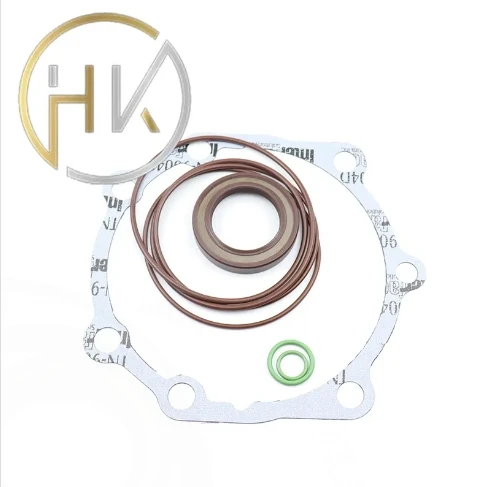
Motor seals come in various types, including lip seals, mechanical seals, and oil seals. Each is designed for specific applications and environmental conditions. Lip seals, for example, are commonly used for their ability to withstand high-speed rotations and are often found in applications requiring minimal leakage. Mechanical seals are known for their robust build, making them ideal for heavy-duty industrial machines. Oil seals, on the other hand, are frequently used to retain lubricants while preventing dirt, dust, and water from entering the system.
Material selection is another critical factor when choosing motor seals. The material must be compatible with the substances it will encounter, as well as the temperature and pressure conditions of the application. Common materials include nitrile rubber, fluoroelastomer (Viton),
silicone, and PTFE. Nitrile rubber is widely used due to its excellent resistance to oils and petroleum-based fluids but may not perform well in high temperatures. Viton offers superior heat resistance and chemical compatibility, making it suitable for high-temperature applications. Silicone seals are favored for their flexibility and ability to function in extreme temperatures. PTFE provides exceptional chemical resistance and is often used in aggressive chemical environments.
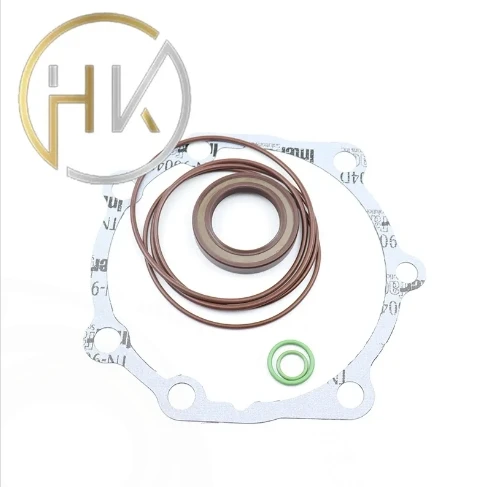
The operational environment greatly influences the choice of motor seal. Conditions such as temperature fluctuations, pressure variations, exposure to chemicals, and the presence of abrasive materials necessitate specific seal characteristics. In environments with high temperature and pressure, seals made from durable materials like Viton or PTFE are recommended. For outdoor applications exposed to dust and moisture, lip seals with proper protective coatings can prevent ingress.
To ensure the reliable performance of your motor seals, proper installation and maintenance are essential. Incorrect installation can lead to premature seal failure, resulting in leakage and damage to the motor. It is crucial to follow the manufacturer's guidelines during installation, using the prescribed tools and techniques. Additionally, regular inspections and maintenance are necessary to identify wear and tear early. Maintenance procedures may include cleaning the seal surfaces, checking for cracks or deformities, and replacing the seal if necessary.
motor seal
Real-world experience emphasizes the importance of choosing the right motor seal for specific applications. A case study from an industrial setting revealed how the correct seal selection and maintenance improved machine efficiency and reduced downtime. The facility shifted from using standard nitrile seals to Viton seals, which provided better resilience in the high-temperature environment, leading to a decrease in maintenance frequency and cost.
Furthermore, working closely with manufacturers and experts can provide invaluable insights into the best motor seal choices. These professionals offer expertise in seal design, material science, and application engineering, ensuring the seal not only fits perfectly but also functions optimally within the specified environment. Their authoritative knowledge often allows businesses to tailor solutions that address unique operational challenges, thereby enhancing productivity and reliability.
Trustworthiness in seal performance can also be enhanced by selecting products from reputable manufacturers adhering to international quality standards. Certifications such as ISO 9001 for quality management systems can be a good indicator of a manufacturer's commitment to producing high-quality, reliable seals.
In conclusion, choosing the right motor seal is not just about meeting immediate operational needs but also ensuring long-term efficiency and reliability. By considering factors such as seal type, material, environmental conditions, and expert recommendations, businesses can safeguard their machinery against failures while optimizing performance. Proper installation and maintenance further cement the seal's role as a critical component in motor reliability.