The hydraulic cylinder dust seal plays an indispensable role in the longevity and efficiency of hydraulic systems across numerous industries. This critical component, often overlooked, safeguards the inner workings of hydraulic cylinders from dust, dirt, and other contaminants that can disrupt performance and cause premature wear. Understanding the intricacies of hydraulic cylinder dust seals will enhance one's ability to maintain these systems effectively, ensuring operational efficiency and equipment longevity.
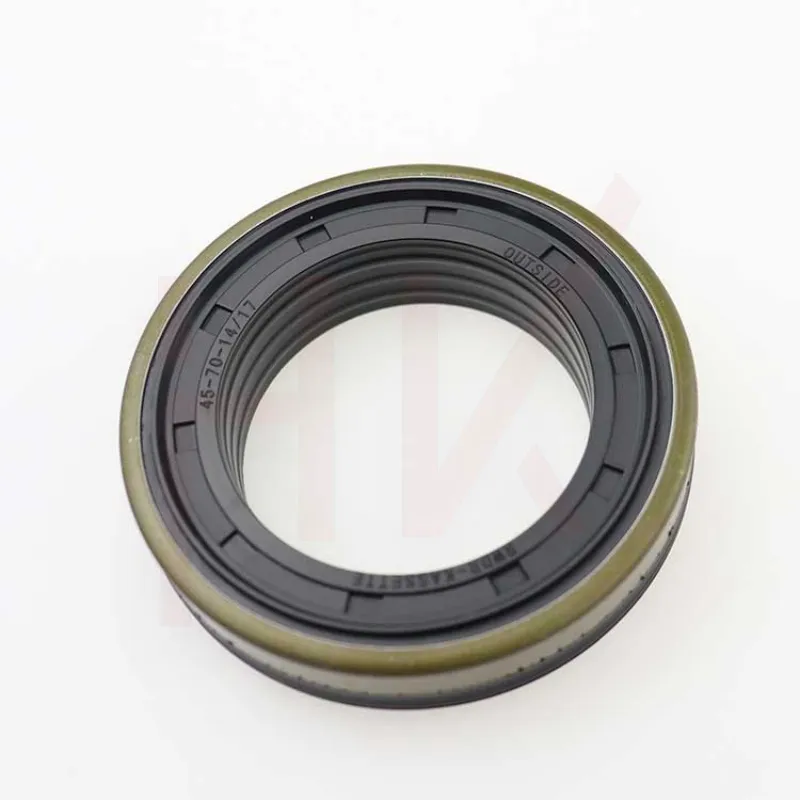
The primary function of a hydraulic cylinder dust seal is to prevent environmental contaminants from entering the hydraulic cylinder. Dust seals are typically composed of durable materials such as nitrile, polyurethane, or a combination of both. These materials are selected based on their resilience, flexibility, and resistance to environmental stresses. A well-designed dust seal will provide an airtight barrier, preventing the ingress of abrasive particles that may lead to scratches on the cylinder rod surface. Such scratches can result in fluid leakage and diminished seal integrity, ultimately leading to significant maintenance challenges and operational downtimes.
In outlining the selection criteria for hydraulic cylinder dust seals, one must consider the operational environment of the hydraulic system. Applications in harsh or extremity-focused environments such as construction sites or mining require seals that offer enhanced durability against abrasive and corrosive substances. Here, polyurethane is often favored for its superior abrasion resistance and ability to maintain performance under fluctuating temperatures. Conversely, applications in less severe conditions may benefit from the flexibility and cost-effectiveness of nitrile seals.
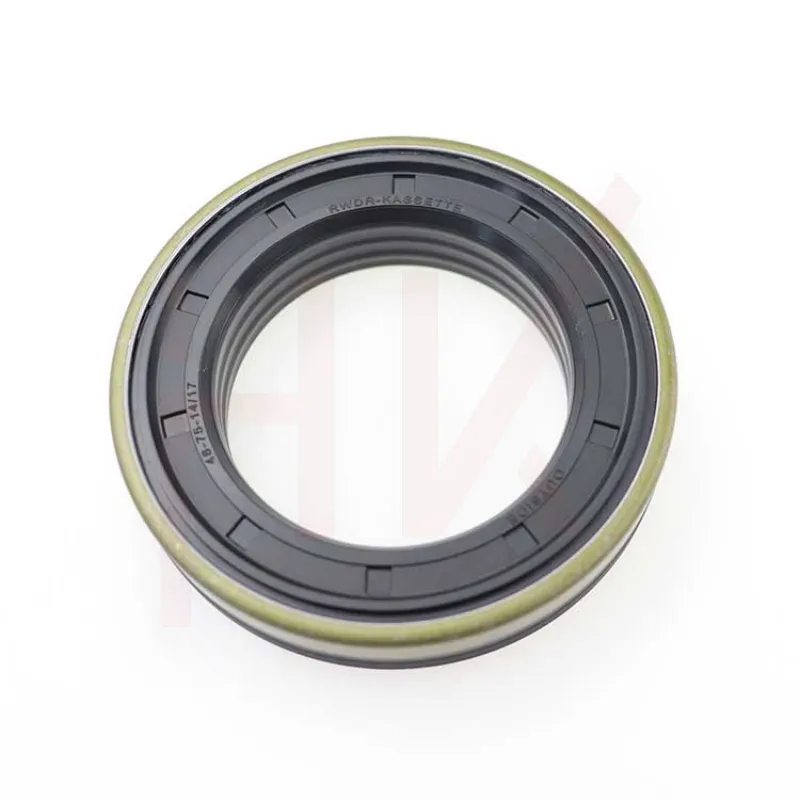
Installation and maintenance practices significantly impact the effectiveness and lifespan of hydraulic cylinder dust seals. Proper installation technique prevents misalignment and ensures the seal is seated correctly, which is crucial for optimal performance. Detailed attention should be given to cylinder rods, inspecting them for nicks or scratches prior to installation of dust seals. Additionally, regular maintenance checks should include an inspection for any signs of seal damage or wear, such as cracks or tears, which could compromise the sealing surface. Implementing a proactive maintenance schedule not only extends seal lifespan but also fortifies the hydraulic system against unexpected failures.
Expertise in hydraulic systems emphasizes that even the best quality dust seals require regular lubrication. Lubricants can provide an additional layer of protection and aid in mitigating friction between the seal and moving surfaces. However, selecting the appropriate lubricant is essential; incorrect lubrication can cause seal material degradation and reduced effectiveness. Therefore, referring to manufacturer guidelines when choosing lubricants ensures compatibility with the seal material.
hydraulic cylinder dust seal
Beyond material and maintenance considerations, design innovations in hydraulic cylinder dust seals have elevated operational efficiencies. Dual-lip seals, for instance, offer enhanced protection by establishing a double barrier against ingress, significantly reducing the likelihood of leaks. Additionally, manufacturers are investing in research to develop smart seals incorporating sensors to monitor wear and performance, predicting potential failures before they occur. This progression not only enhances reliability but also integrates seamlessly with industry trends towards predictive maintenance and smart technologies.
In industries where the reliable operation of hydraulic systems is pivotal, reliance on trusted manufacturers and suppliers of hydraulic cylinder dust seals cannot be overstated. Established companies with a comprehensive portfolio and robust aftermarket support offer both assurance and quality. They provide valuable resources, including detailed product specifications, installation guides, and technical support to assist in addressing any issues that may arise.
Purchasing from reputable sources also ensures compliance with industry standards and a commitment to continual improvement in line with evolving hydraulic technology advancements. The collaboration between end-users and manufacturers can foster a culture of innovation, leading to the development of more efficient, robust, and durable hydraulic seals.
The value of a hydraulic cylinder dust seal is undeniably vast, impacting everything from system efficiency to overall cost management. By prioritizing seal quality, installation accuracy, and proactive maintenance, industries dependent on hydraulic systems can significantly enhance their operational resilience and reliability. As technology and material sciences continue to evolve, so too will the efficacy and application range of hydraulic cylinder dust seals, securing their place as a cornerstone of hydraulic system integrity.