High pressure seals are critical components in numerous industrial applications, known for their ability to maintain the integrity of systems against leaks even under extreme conditions. Understanding their functionality and importance can significantly enhance operational efficiency in sectors ranging from manufacturing to aerospace.
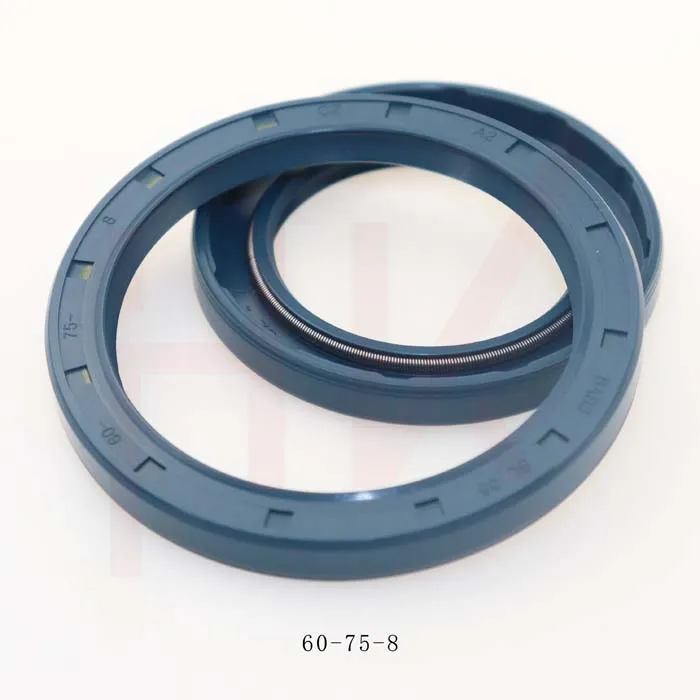
In industries where machinery is consistently exposed to high pressure and fluctuating temperatures, the need for components that can withstand such harsh environments is paramount.
High pressure seals are designed to meet these demanding requirements by providing secure containment of fluids or gases within a system. They act as barriers that prevent the escape of pressurized substances, thereby ensuring the continued safe and efficient operation of equipment.
One of the notable features of high pressure seals is their construction material. These seals are typically made from advanced compounds such as PTFE, nitrile rubber, and polyurethanes, each selected for its specific properties that contribute to durability and performance. For instance, PTFE offers exceptional chemical resistance and operates efficiently in a wide range of temperatures, making it suitable for applications where both high pressure and corrosive substances are present.
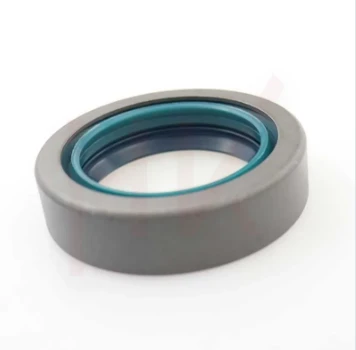
Experience in the field reveals that the selection of the appropriate high pressure seal is as crucial as its installation. An improperly chosen seal may lead to failures that result in costly downtime or hazardous situations. Therefore, it is essential to understand the operational environment, including pressure levels, temperatures, and exposure to chemicals, to select the ideal seal.
Expertise in high pressure seal technology is often shared through collaboration with manufacturers and engineers who specialize in seal design and application. They offer insights into the nuances of seal performance, including longevity and maintenance requirements. Moreover, these experts can recommend custom solutions tailored to specific industrial needs, which can often mean the difference between a seal that simply performs well and one that excels under the most challenging conditions.
high pressure seal
Authoritativeness in the field is underpinned by continuous improvements and innovations in seal technology. Leading manufacturers invest in research and development to produce seals that not only meet current industry standards but set new ones. These include innovations such as self-lubricating seals which enhance operational life, or seals that incorporate composite materials designed to deal with multi-directional pressure.
Building trustworthiness in high pressure seal solutions involves rigorous testing and quality assurance protocols. Manufacturers adhering to international standards such as ISO 9001 can provide peace of mind that the seals have been tested for quality and reliability. In addition, case studies and testimonials from other users can be valuable resources for assessing the performance and reliability of high pressure seals in real-world applications.
A deep dive into case studies where high pressure seals have revolutionized operations demonstrates their importance. For example, in the oil and gas industry, effective sealing solutions are critical in drilling applications where pressure levels can reach extreme highs. The correct seal not only prevents leaks that could lead to environmental disasters but also ensures consistent delivery of performance, which is crucial for productivity and safety.
Understanding the life cycle management of high pressure seals also influences operational success. Regular inspection, maintenance schedules, and timely replacements prevent unexpected failures. Many companies capitalize on digital monitoring systems to track seal performance, necessitating familiarity with IoT technologies and predictive maintenance strategies.
Selecting and maintaining high pressure seals decisively enhances efficiency and safety in industrial applications. Leveraging experience and expertise ensures these components are optimized for performance, reliability, and cost-effectiveness. The ongoing advancements in seal technology demonstrate commitment to quality and innovative solutions that meet evolving industrial demands.