Hydraulic cylinders are essential components in many industrial and mobile machinery applications, serving as the workhorses that bring mechanized processes to life.
A crucial yet often overlooked aspect of maintaining the efficiency and longevity of hydraulic cylinders is the installation of high-quality wipers. Hydraulic cylinder wipers are indispensable in safeguarding cylinders from harsh external environments, ensuring they operate smoothly and reliably over time.
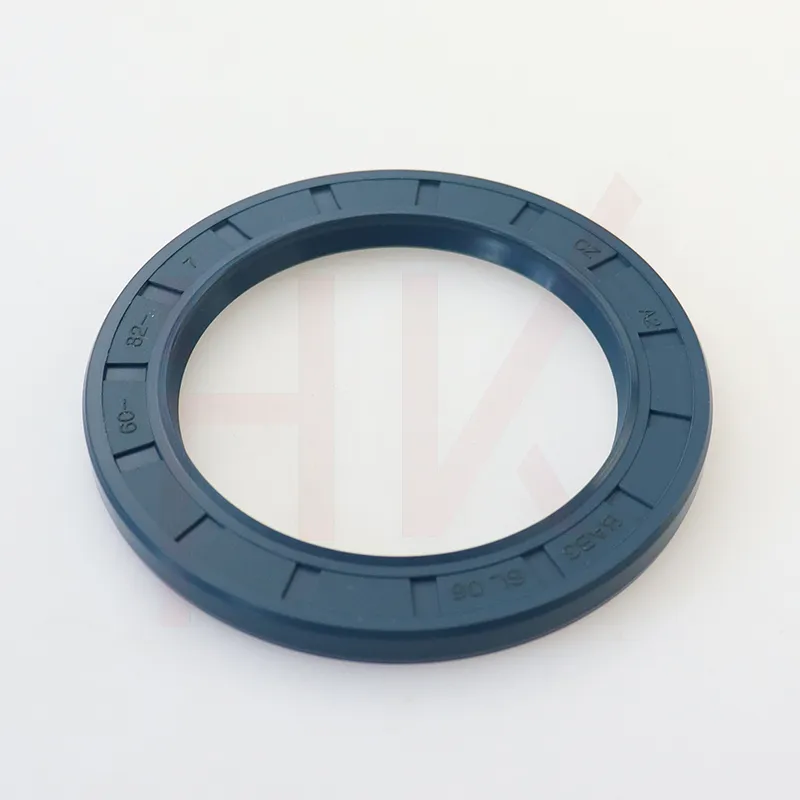
Wipers, sometimes known as scrapers, perform a critical role by cleaning the piston shafts of contaminants that could otherwise compromise the internal systems. As the piston rod extends and retracts, wipers prevent dirt, dust, mud, and other foreign particles from entering the hydraulic cylinder. This function is paramount to minimize wear on sealing systems, preventing possible malfunctions or breakdowns that might result from contaminated seals.
The expertise surrounding hydraulic cylinder wipers involves understanding the materials and designs that compose these essential components. Typically made from robust materials such as polyurethane, nitrile rubber, or thermoplastic elastomers, wipers are designed to withstand the demanding conditions of various environments, from exposure to hydraulic fluid to extreme weather conditions. Polyurethane, for example, offers excellent abrasion resistance, making it an ideal choice for wiper construction in abrasive environments. Nitrile rubber is often chosen for its oil-resistant properties, providing optimal performance in applications exposed to petroleum-based fluids.
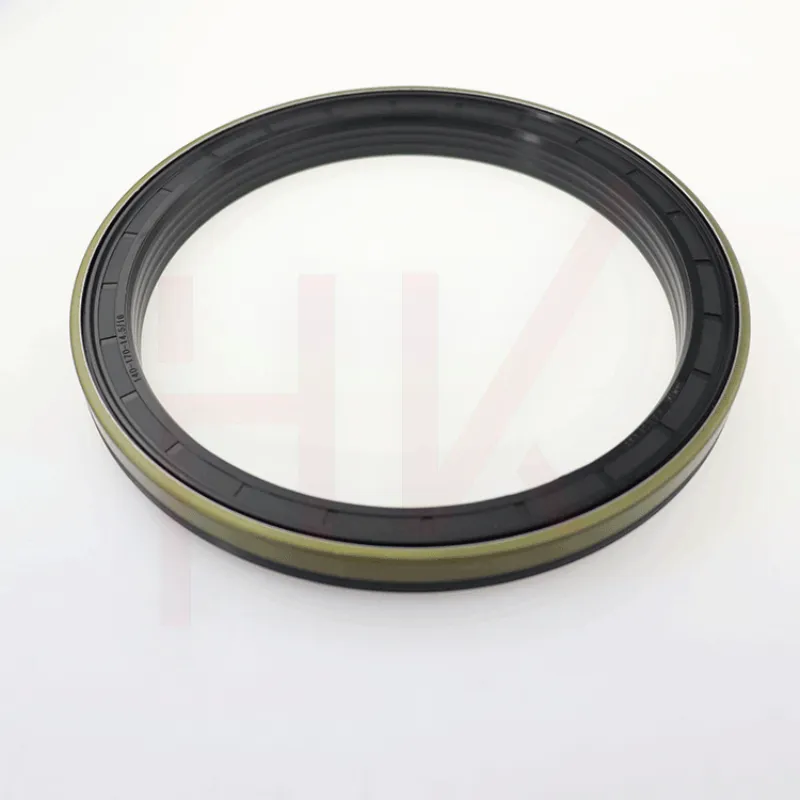
Innovation in wiper design has also led to the development of specialized profiles that enhance the ability to scrape off contaminants efficiently. The unique geometries of modern wipers ensure a tight seal against the piston rod, reducing the risk of damage from excessive friction while extending the life of both the wiper and the hydraulic system as a whole. Furthermore, advancements in co-molded designs—that combine different materials—offer improved performance characteristics tailored to specific industrial applications.
hydraulic cylinder wipers
In terms of reliability, choosing the right hydraulic cylinder wiper involves evaluating several factors environmental conditions, type of contaminants likely to be encountered, the hydraulic system's pressure levels, and the temperature range within which the machinery operates. Manufacturers often provide guidance on selecting suitable wipers based on these criteria, reinforcing the importance of expert advice in selecting the appropriate component for each unique situation.
Trustworthy manufacturers of hydraulic cylinder wipers offer products that have undergone rigorous testing and quality assurance protocols. Such testing verifies the durability and effectiveness of the wipers under simulated operational conditions, providing peace of mind that the products will perform as expected when deployed in real-world applications. Additionally, sourcing wipers from reputable suppliers with a proven track record enhances confidence in their performance and durability.
Anecdotal evidence from industry professionals reveals significant improvements in hydraulic system performance following the proper installation and maintenance of high-grade wipers. Operators have noted fewer failures and extended maintenance intervals, translating into cost savings and reduced downtime for machinery. This level of expert feedback highlights the authoritative consensus on the critical role hydraulic cylinder wipers play in maintaining operational efficiency and longevity.
In summary, hydraulic cylinder wipers are far from a mere accessory; they are integral to the preservation and optimal functioning of hydraulic systems. The expertise required to select and maintain these components is backed by authoritative insights and proven experiences within the industry. For businesses relying on the robust performance of hydraulic cylinders, investing in premium-quality wipers is a decision that reinforces efficiency, protects valuable equipment, and builds trust in operational reliability. By focusing on the specific needs and challenges of each application, industry experts continue to advance the standards of protection these small yet mighty components offer, ensuring that machinery performs at its peak for years to come.