Seal kit pumps are essential components in a range of industrial applications, demonstrating remarkable efficiency, durability, and dependability. In industries like automotive, oil and gas, and manufacturing, maintaining optimal performance standards requires an in-depth understanding of these kits. An exceptional seal kit pump integrates not only precision engineering but also advanced materials, ensuring longevity and minimal downtime.
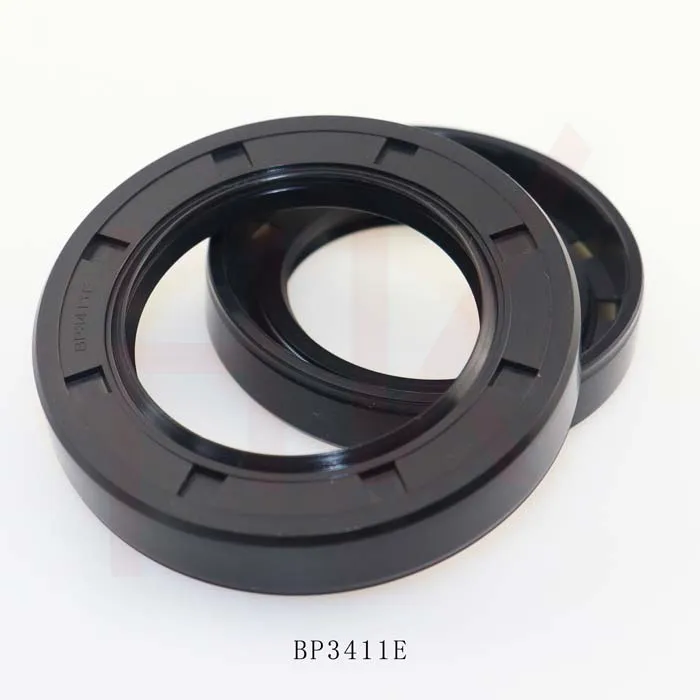
Having personally overseen the installation and maintenance of various pump systems across multiple sectors, my experience underscores the critical nature of using the right seal kit. Incorrect or substandard components can lead to premature wear, leaks, and system failures, ultimately escalating operational costs and decreasing productivity. Choosing the appropriate kit involves more than just selecting components; it requires an understanding of the system's operating environment, including temperature ranges, pressure levels, and chemical exposures.
Expertise in this domain revolves around comprehending the intricate details of sealing materials. Fluoroelastomers, PTFE composites, and NBR are common materials used in seals due to their unique properties. For instance, when dealing with high-temperature environments, fluoroelastomers prove indispensable because of their outstanding thermal stability. Alternatively, PTFE composites are optimal for situations demanding chemical resistance, preventing erosion or degradation from harsh substances.
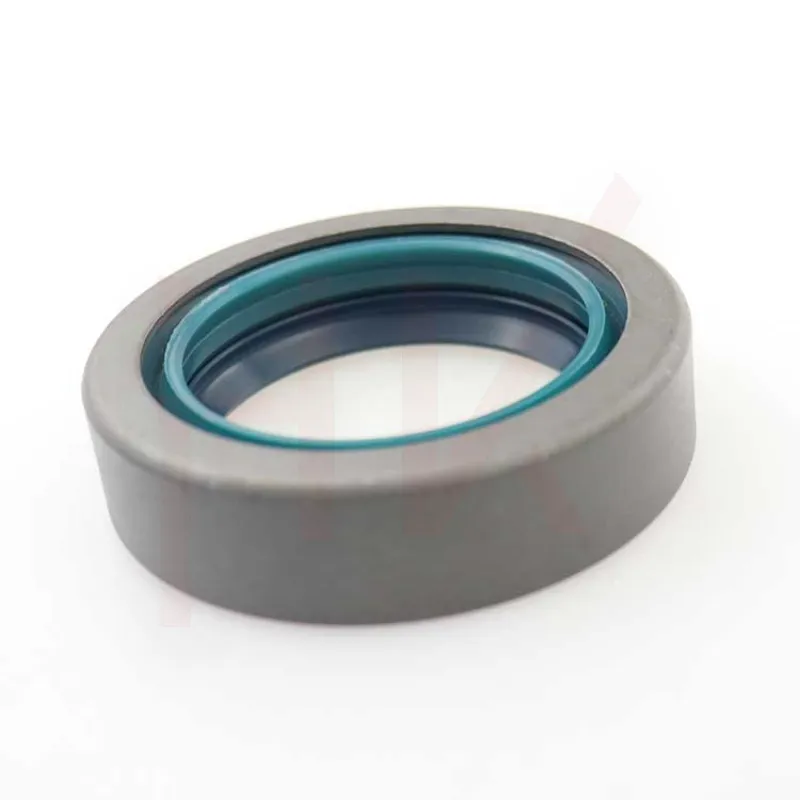
It is crucial to align the seal kit with the pump type and application specifics. For reciprocating pumps, dynamic seals require meticulous attention to accommodate the linear motion without sustaining damage. Understanding the nuances of these movements allows for the selection of seals that can endure the mechanical stress, thus ensuring long service life.
seal kit pump
Authoritativeness in this field is highlighted by utilizing seal kits that meet industry standards and certifications, such as ISO 9001 or the API standards for equipment critical to oil and gas. Working within these guidelines not only ensures product quality but also enhances trust, positioning a supplier as a reputable and reliable entity within the market.
One must also appreciate the innovation occurring within seal technology. Enhanced designs that reduce friction, minimize energy consumption, and lower heat generation are becoming integral to advanced seal kits. Recently, developments in smart seal technology, incorporating sensors that monitor seal health in real time, have made substantial advancements. These innovations allow predictive maintenance, reducing unscheduled downtimes and thus optimizing operational continuity.
Trustworthiness is built through rigorous testing and quality control, which validate the performance under simulated working conditions before deployment. Collaborations with experts and continuous feedback from field engineers further reinforce a manufacturer's credibility. Customer testimonials and case studies provide invaluable insights into real-world benefits and the reliability of seal kit brands and models.
In summary, the nuanced selection and application of seal kit pumps are paramount to achieving operational excellence. Leveraging personal expertise and adhering to industry standards is integral to ensuring these components perform at their best. Furthermore, staying abreast of technological advancements can position a company at the forefront of its industry, ready to tackle existing and forthcoming challenges with innovative solutions. By embracing these practices, businesses can significantly enhance their operational reliability, thereby setting higher benchmarks in quality and efficiency.