Hydraulic motor oil seals play an integral role in maintaining the efficiency and longevity of hydraulic systems. These components are designed to prevent leaks, protect against contaminants, and ensure that the machinery operates smoothly under various conditions. Understanding their importance requires a blend of hands-on experience, technical expertise, and authoritative knowledge, ensuring trustworthiness in all hydraulic system applications.
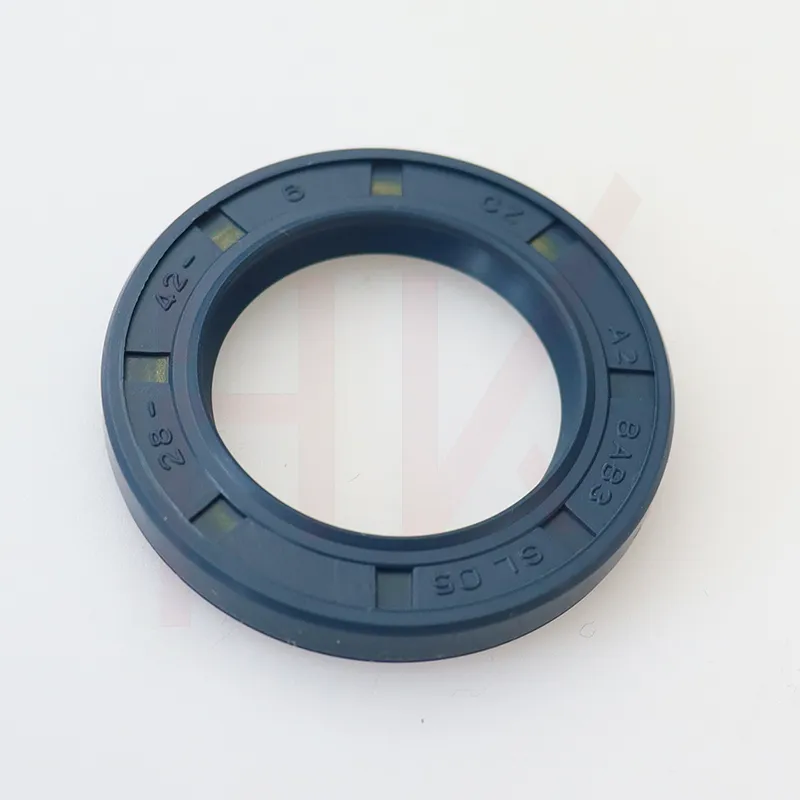
In any hydraulic system, oil seals act as guardians of the moving parts. They are strategically positioned to close off spaces between stationary and moving components, thereby preventing the leakage of hydraulic fluid. This is crucial because the leakage can lead to decreased system efficiency, potential environmental hazards, and increased maintenance costs. The effectiveness of a hydraulic motor depends significantly on the integrity of its oil seals, making their selection and maintenance pivotal for optimal performance.
When selecting an oil seal for a hydraulic motor, various technical considerations should be made. It's essential to evaluate the temperature range, pressure capacity, and the chemical properties of the fluid in use. Experienced professionals understand that an oil seal must be compatible with the specific hydraulic fluid to avoid degradation, which can result from exposure to certain chemicals. Additionally, the temperature and pressure ratings ensure that the seal can withstand the operational conditions without deformation or failure.
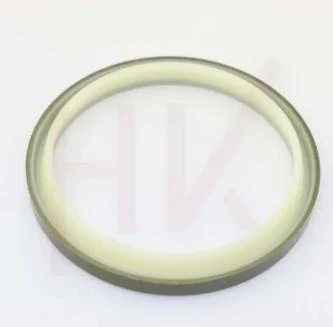
Oil seals come in various materials, each offering distinct advantages depending on the application. For example, nitrile is a popular choice because of its balance of durability and cost-effectiveness, suitable for applications with moderate pressure and temperature. However, for higher temperature ranges or extreme pressures, materials like fluorocarbon or silicone might be preferred. Therefore, expert knowledge in material science and engineering is vital for recommending the right seal for a specific application, ensuring system longevity and reliability.
Moreover, installation and maintenance of these seals require precision and expertise. During installation, any misalignment or incorrect fitting can lead to premature wear and tear. Skilled technicians emphasize the importance of ensuring that the sealing surface is impeccably clean and that the seals are carefully installed using the appropriate tools. This attention to detail helps prevent initial installation failures, which can contribute to early system downtimes and costly repairs.
hydraulic motor oil seal
Regular maintenance checks are also essential to sustain the performance of hydraulic motor oil seals. Inspections should include looking for signs of wear, such as hardening, cracking, or even slight deformations. Addressing these issues promptly with parts replacement can prevent minor problems from escalating into catastrophic failures. Trustworthy maintenance programs are underpinned by routine checks and balances which professionals with extensive experience in the field often advocate.
As manufacturers continue to innovate, the development of advanced oil seal technologies offers improved sealing capabilities to meet evolving industrial demands. New seal designs incorporate innovative lip geometries and materials that enhance the sealing capability, improve resistance to wear, and extend the service intervals of hydraulic motors. Industry experts emphasize staying abreast of these emerging technologies to maintain competitive advantage and ensure machines run efficiently with minimal environmental impact.
Lastly, partnering with reputable suppliers and manufacturers of hydraulic oil seals is crucial. These entities provide the assurance of quality and compliance with industry standards. Authoritative suppliers also offer valuable insights and support, drawing from vast reservoirs of industry-specific knowledge and historical data to provide solutions tailored to unique operational challenges.
In summary, hydraulic motor oil seals are more than just a passive component. Their correct specification, installation, and maintenance require a confluence of experience, expertise, authority, and trustworthiness. Ensuring these characteristics are adhered to not only enhances the reliability and efficiency of hydraulic systems but also reinforces the safety and environmental compliance within diverse industrial applications.