Hydraulic gear pumps are essential components in numerous industrial and machinery applications, playing a critical role in managing fluid flow within hydraulic systems. For these pumps to function efficiently over extended periods, quality seals are indispensable. These hydraulic gear pump seals are not merely peripheral components; they are central to optimal performance, ensuring system integrity and prolonging the life of the pump. Choosing the right seals can be a game-changer for efficiency and reliability, making it crucial for engineers and operators to understand their dynamics and selection criteria deeply.
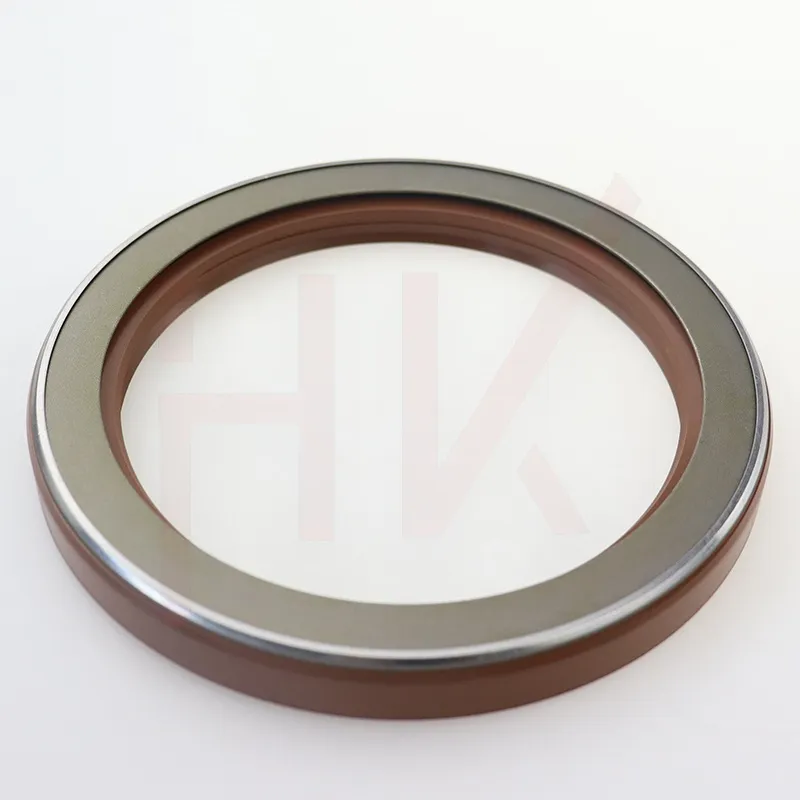
Seals in hydraulic gear pumps are designed to prevent fluid leakage, keep contaminants out, and contain system pressure, which is essential for maintaining the pump’s volumetric efficiency. They must withstand challenging conditions, including high pressure, extreme temperatures, and aggressive fluids, making the choice of materials and design crucial. Common materials utilized for these seals include nitrile rubber (NBR), fluorocarbon (Viton), and Polytetrafluoroethylene (PTFE), each offering unique benefits suited to specific operational environments.
The first step in choosing suitable hydraulic gear pump seals involves understanding the operational environment of the pump. For instance, if a pump is used in high-temperature conditions, selecting seals made from Viton can offer superior heat resistance compared to standard nitrile options. Conversely, PTFE seals are recognized for their excellent chemical resistance and low friction, making them ideal for operations involving aggressive fluids.

When evaluating seals, it's pertinent to consider the types of seals available and their respective applications. Shaft seals, for instance, are integral to prevent leakage along the pump shafts, while face seals can be vital for ensuring the sealing integrity of connecting surfaces. Each has distinct design features optimized for specific functionality within the pump mechanisms.
In addition to material and type, assessing the seal's pressure capacity and tolerance levels is paramount. A mismatch here can result in premature seal failure, leading to potential fluid leaks and costly downtime. Consulting with manufacturers' specifications and industry standards can provide guidance on selecting seals that meet or exceed operational demands of the hydraulic gear pump system.
hydraulic gear pump seals
Seals must also be checked regularly as part of a broader maintenance program to ensure they remain in optimal condition. Regular inspections can identify wear and tear, cracking, or other signs of degradation that, if left unaddressed, could lead to system inefficiencies or failures. Employing predictive maintenance technologies like vibration analysis or thermography can enhance this proactive approach, helping identify issues before they result in costly breakdowns.
Establishing strong relationships with reputable manufacturers can also be advantageous. Suppliers with comprehensive expertise in hydraulic systems can offer valuable insights into emerging seal technologies or enhancements that might provide superior performance or longer lifespans. Engaging with these experts ensures that you’re not only using the best current options but are also aware of improvements and innovations in seal material science and design.
The investment in high-quality hydraulic gear pump seals goes beyond immediate operational efficiency; it speaks to a commitment to system reliability, longevity, and safety. Proper seal selection and maintenance can shield a hydraulic system from unplanned downtimes and inefficient operation, reducing expense overheads and increasing productivity over time.
Understanding and navigating the complex landscape of hydraulic gear pump seals requires balancing practical experience, technical knowledge, and a commitment to continuous learning. As the technology evolves, new materials and designs will emerge, potentially offering enhanced performance features. Staying updated through industry journals, technical seminars, and collaborations with industry leaders ensures you maintain an expert grasp on seal efficacy and application, fostering an environment of trust and authority while ensuring hydraulic system excellence.
Adopting this comprehensive approach not only ensures that hydraulic gear pumps fulfill their potential but also fortifies an organization’s reputation for maintaining mechanical integrity, efficiency, and modernity in its industrial operations.