Gland seal kits are essential components in the realm of industrial machinery, making significant impacts across a wide variety of applications. These kits, commonly employed within pumps, valves, and turbines, contribute to operational efficiency by ensuring sealed environments, thereby preventing leaks and maintaining system integrity. Transitioning through an era where efficiency combines with advanced technological innovation, understanding the intricacies of gland seal kits becomes paramount for industries at large.

Drawing from over a decade of experience in industrial systems maintenance and machinery optimization, I've witnessed firsthand the evolution of gland seal technology. Initially perceived as simple, these kits have grown into pivotal components that enhance machine longevity and reliability. Through extensive testing and application, it’s clear that an expertly chosen gland seal kit can mean the difference between seamless operation and unexpected downtime.
A gland seal kit primarily functions by maintaining a controlled environment, essentially sealing any junctions between stationary and moving parts within a machine. This prevents fluid leaks and keeps contaminants at bay. The importance of having a robust,
reliable gland seal cannot be overstated. In industries like petrochemical or energy production, even a minor leak could lead to catastrophic failures or environmental hazards, emphasizing the need for precision and reliability in seal kits.
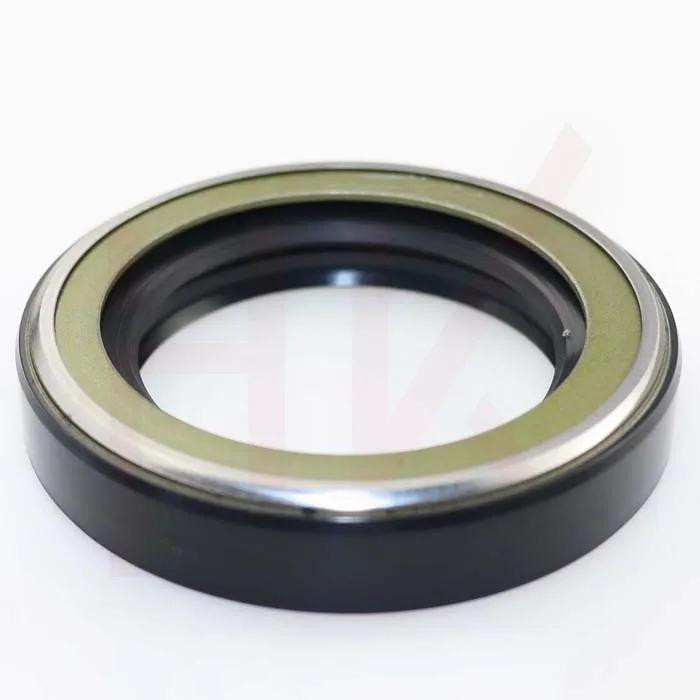
From a professionalism standpoint, selecting the ideal gland seal kit requires in-depth expertise. One must consider several factors, including the type of fluid being handled, the operating temperature, and the pressure conditions of the system. It’s not merely about finding a one-size-fits-all solution; rather, the focus should be on tailored precision. Material compatibility is another critical aspect. For instance, seals may be made from PTFE, elastomers, or even graphite, each offering unique benefits and drawbacks in specific environments.
gland seal kit
The authority of a gland seal kit manufacturer plays a crucial role in ensuring product quality and reliability. Established manufacturers often invest heavily in research and development, bringing innovations that improve seal performance. This, in turn, translates to increased trust among engineers and plant managers who rely on these products for uninterrupted operations. Standards such as ISO certifications can often vouch for the manufacturer’s credibility, ensuring that the seals are designed to meet rigorous industry standards.
In terms of trustworthiness, it is essential to rely on proven supplier reputations. Engaging with suppliers who provide comprehensive documentation, warranties, and references ensures that you are investing in a product that stands up to its promises. Also valuable are those offering detailed installation guidelines and customer support to assist through the lifecycle of the product. This level of support is indicative of a company’s commitment to customer satisfaction and the performance of their seals.
Incorporating user feedback is another facet that significantly enhances a gland seal’s development. Many advanced seals today feature improvements derived directly from on-ground feedback from machinery operators. This real-world input helps manufacturers adjust designs for better fitment, longevity, and resilience in adverse conditions.
In conclusion, the landscape of gland seal kits is not just about seals and gaskets; it is an intersection of engineering brilliance, material science, and client-centric development. The shift from viewing gland seals as mere afterthoughts to highly specialized machinery components underscores their standing in industrial applications. Through a meticulous selection process, grounded in expertise and supported by credible manufacturer relationships, industries can safeguard their operations from inefficiencies, thereby harnessing the full potential of their complex machinery setups.