Rotary shaft oil seals, often referred to as radial lip seals, play a crucial role in maintaining the integrity and efficiency of machinery by preventing the leakage of lubricants, oils, and greases while keeping contaminants at bay. These seals are indispensable in various industries, from automotive to manufacturing, thanks to their ability to ensure operational efficiency and longevity of equipment.
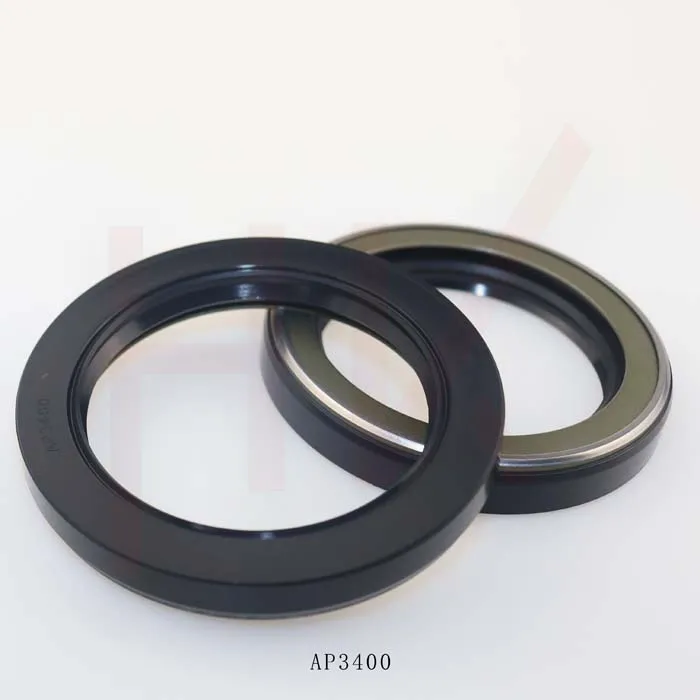
In the realm of industrial design and maintenance, understanding the nuance of rotary shaft oil seals is paramount. High-quality seals function efficiently under varying temperatures and rotation speeds, a testament to their engineering prowess. These seals must endure extreme conditions and continue to offer optimal performance without frequent replacements, thereby safeguarding expensive machinery components from premature wear.
When selecting a rotary shaft oil seal, the material composition is a foremost consideration. Premium seals often use nitrile rubber (NBR) for its affordability and moderation between temperature resistance and mechanical performance. However, for applications demanding exceptional thermal and chemical resistance, fluorocarbon elastomers (FKM), renowned for their durability and performance in harsh environments, are preferred. Choosing the right material directly influences the seal’s life span and efficiency.
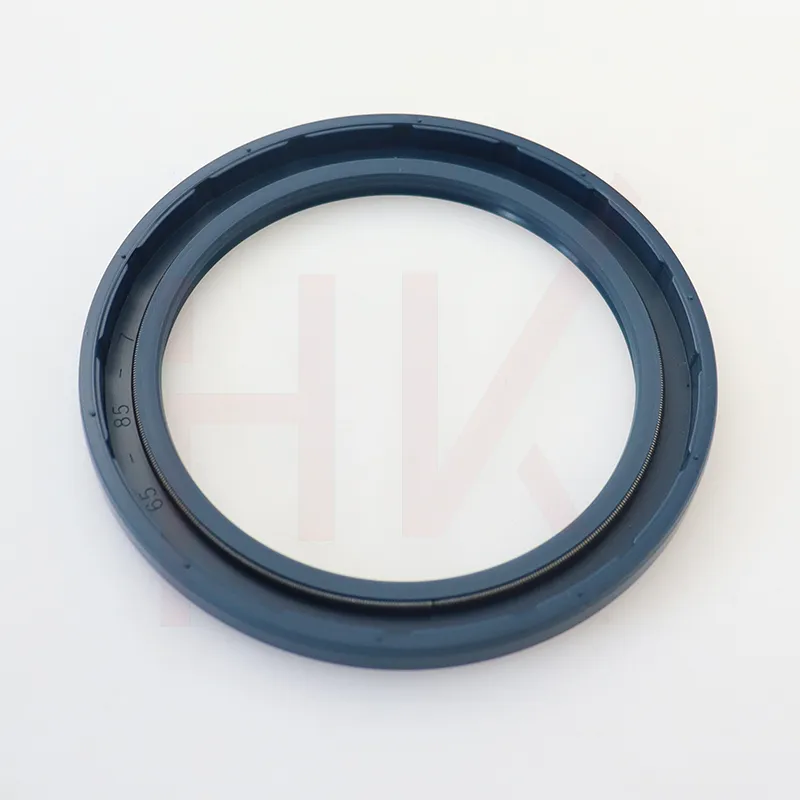
Precision in the design and installation of these seals cannot be overstated. A meticulously engineered seal should align perfectly with the shaft, maintaining a stable rotational axis and minimizing frictional losses. Calibrated dimensions and tight tolerances ensure that the seals provide the necessary barrier without causing undue wear to the shaft. It’s the interplay of these precision factors that determines the reliability of rotary shaft oil seals in conjunction with fluctuating operational parameters.
The application of these seals extends beyond simple containment of fluids. In dynamic applications, such as in automotive transmission or aerospace turbine engines, they must contend with high-speed rotational forces and sudden directional changes. This requires an advanced understanding of fluid dynamics and material science, making it essential for manufacturers and engineers to remain informed about the latest advances in seal design and technology.
rotary shaft oil seals
Real-world experience underscores the critical nature of comprehensive maintenance regimens. For instance, regular inspection of seal integrity can proactively identify potential failures indicated by vibration, unusual noises, or visible leaks. Seals that seem perfectly functional can degrade without visible signs, leading to catastrophic failures if not periodically monitored. Adopting such strategic maintenance routines maximizes equipment uptime and results in significant cost savings.
From an expertise standpoint, professionals dealing with these components should possess an in-depth understanding not only of the mechanical requirements but also of the environmental variables that affect seal performance. Knowledge of industry-specific requirements, such as the specialized needs of food-grade machinery versus heavy-duty construction equipment, informs better decision-making and product selection.
Authoritative information on rotary shaft oil seals is often disseminated through technical manuals, industry publications, and certifications that assure design compliance with international standards such as ISO or SAE. Leveraging these resources helps in making informed decisions tailored to specific industrial contexts, thereby assuring operational safety and efficiency.
Trustworthiness in product sourcing is equally essential. Partnering with reputable manufacturers known for their robust quality control and innovation can mitigate risks of acquiring substandard seals. Another layer of trust is developed through transparent communication and advice from industry-vetted professionals providing guidance tailored to unique operational challenges, thus ensuring optimal product performance and longevity.
In summation, rotary shaft oil seals are a cornerstone of operational effectiveness across multiple industries. Mastery in choosing and maintaining these seals not only hinges upon material selection and precision engineering but also requires continuous experiential learning and adaptation to evolving technological advancements. Through a commitment to quality and maintenance excellence, businesses can uphold equipment integrity, thereby enhancing productivity and consequent profitability.