Understanding the importance of the perfect 14x22x5 oil seal can make a significant difference in the performance and longevity of machinery. These seals, often overlooked, are pivotal in maintaining the integrity of various mechanical systems, preventing leaks, and ensuring components remain free from contamination. As an expert in mechanical components, sharing nuanced insights into the importance, selection, and maintenance of oil seals is crucial for anyone looking to optimize machinery performance.
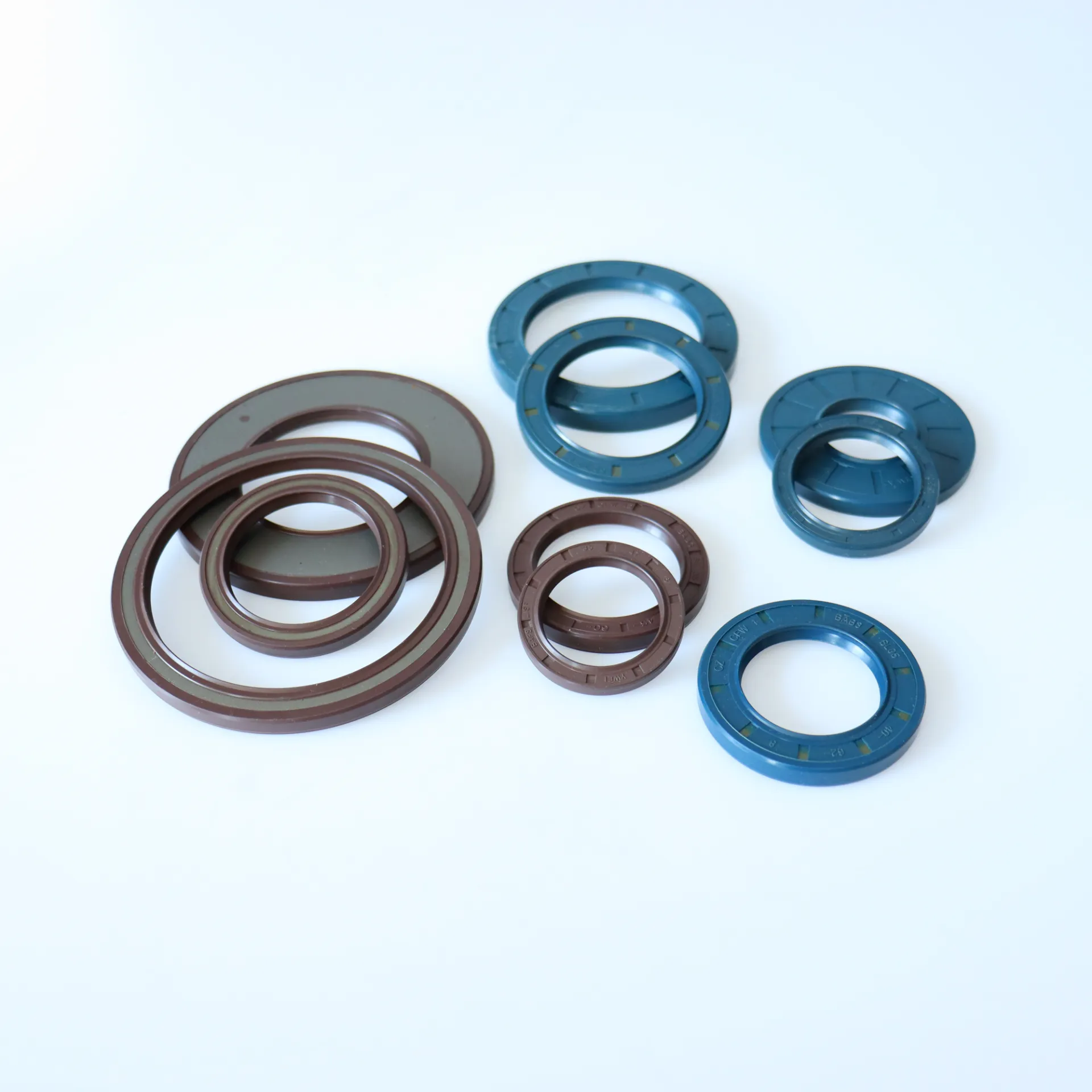
Oil seals are designed to close spaces between stationary and moving components within mechanical equipment, effectively preventing lubricants from escaping. Furthermore, they protect systems from dirt and contaminants which could lead to mechanical failure. The 14x22x5 oil seal, with its specific dimensions, holds a reputation in various industries, particularly automotive and industrial sectors, for its ability to provide reliable sealing over time.
When discussing expertise in oil seals, especially the 14x22x5 size, it is essential to understand the material compositions and designs that best fit specific applications. Common materials include nitrile rubber, known for its excellent resistance to oil and heat, and fluorocarbon, which is chosen for applications requiring higher temperature stability. These materials not only extend the life of the oil seal but also optimize its performance in high-pressure environments.
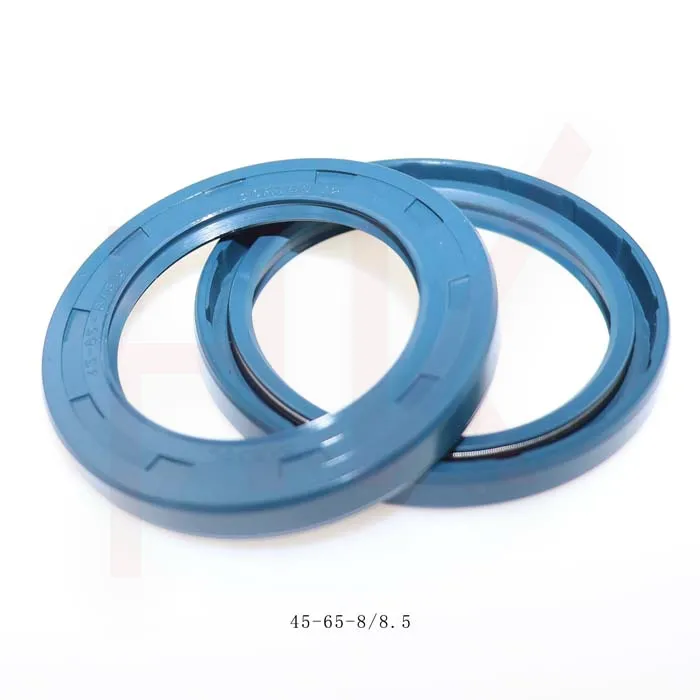
Selecting the right 14x22x5 oil seal goes beyond merely choosing the correct size. Expertise in this domain demands an understanding of the operating conditions, such as temperature ranges, speed, and pressure requirements that the seal will encounter. For instance, nitrile rubber might be suitable for moderate temperatures and general applications, but fluorocarbon might be necessary for more demanding environments with higher thermal stress.
Authoritativeness in the field also implies familiarity with the latest enhancements in oil seal technology. Advances such as the incorporation of polytetrafluoroethylene (PTFE) lip designs have furthered seal capabilities by offering lower friction, increased wear resistance, and improved sealing against aggressive media. An authoritative source acknowledges these innovations and suggests the best use cases for them.
14x22x5 oil seal
Trustworthiness is reinforced by real-world performance and verifiable results from rigorous testing. An authoritative endorsement of a 14x22x5 oil seal often involves referencing industry standards such as ISO 6194 or DIN 3760, which outline the quality, performance, and reliability testing these products should meet. By adhering to such standards, manufacturers ensure that their seals provide consistent performance over time.
Real-world experience further establishes trust and expertise. For example, in automotive applications, significant performance improvements have been noted in engine efficiency and reduced oil consumption after replacing worn-out seals with high-quality 14x22x5 oil seals. Feedback from industry professionals consistently highlights the durability and reliability of these seals in high-stress environments, substantiating their value and functionality.
Finally, regular maintenance is critical in preserving the efficacy of oil seals. Frequent inspections can preemptively identify wear or damage, which might compromise the seal's performance. Implementing a routine maintenance schedule not only extends equipment life but also helps avoid unexpected downtimes, thus affirming the reliability and necessity of the right oil seals in the right applications.
In conclusion, the 14x22x5 oil seal plays a crucial role in the functionality and reliability of mechanical systems. Approaching its selection and application with a sophisticated understanding ensures optimal performance, while innovation and adherence to standards signify its trustworthy nature. In every application, from industrial machines to automotive engines, these seals serve as silent guardians, safeguarding machinery from failure and inefficiency.