Navigating the landscape of industrial components often feels like mapping uncharted territories. Among these crucial parts, the oil seal hub stands out as pivotal, particularly in automotive and heavy machinery industries. These hubs are fundamental in ensuring that machinery operates efficiently and safely, acting as the barrier that keeps lubricants within components while preventing contaminants from infiltrating crucial systems.
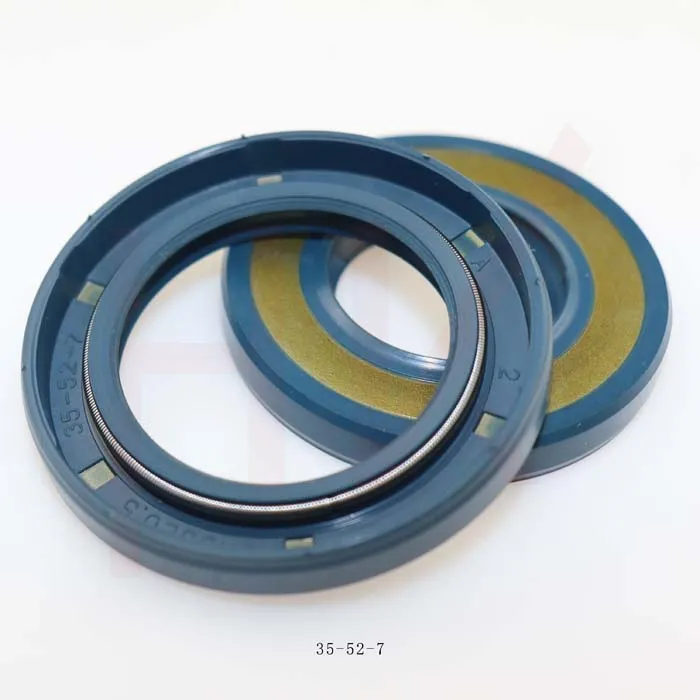
Oil seal hubs are crafted with precision, involving sophisticated manufacturing processes that blend engineering prowess with cutting-edge technology. This product's importance cannot be overstated it mitigates the damage that can arise from friction and environmental exposure, enhancing the lifespan and reliability of machinery. To those who rely on industrial equipment daily, these pieces symbolize the frontline defense in mechanical efficiency and protection.
Drawing from extensive experience in the field, it's clear that not all oil seal hubs are created equal. Different environments and applications demand variations in design,
materials, and constructions. For instance, high-temperature zones often require hubs made from advanced synthetic materials known for their resilience against heat degradation. Similarly, environments rich in corrosive materials call for seals constructed from specialized alloys and compounds capable of enduring chemical exposure without losing structural integrity.
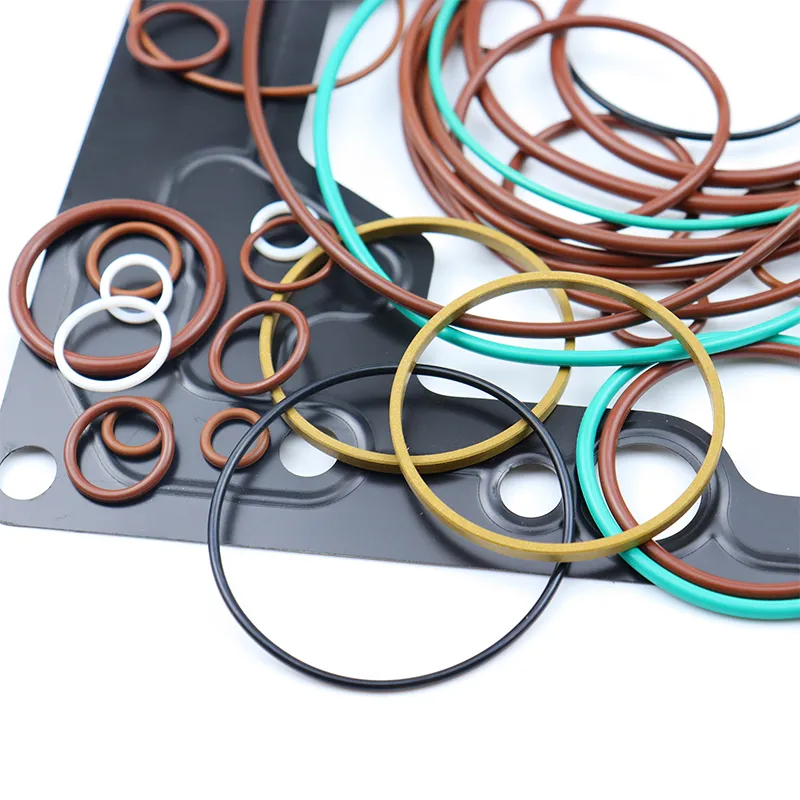
In terms of expertise, choosing the right oil seal hub requires a comprehensive understanding of both the operational context and the mechanical designs of the systems in question. It's vital to consider the dynamics of the application, including the rotational speed, pressure differentials, and thermal conditions the oil seal will encounter. This knowledge informs not just selection but also maintenance routines that prolong the effectiveness and efficiency of the seal.
oil seal hub
The authority of a trusted manufacturer often speaks volumes when selecting an oil seal hub. Top-tier companies invest heavily in research and development, constantly innovating to improve performance and durability. They emphasize stringently controlled manufacturing environments to produce seals with precision tolerances, capable of performing consistently under varied conditions. These manufacturers are typically ISO-certified, ensuring their products meet international quality standards—an essential marker of trust and reliability in the industry.
Trustworthiness in encounters with oil seal hubs is built through comprehensive testing and quality assurance procedures. A reliable seal should undergo rigorous trials simulating real-world conditions, with results verified by third-party organizations to ensure accuracy. Offering warranties and clear maintenance guidelines further underscores a manufacturer's commitment to their product's enduring performance.
Critically, the role of oil seal hubs is inexorably linked to the functional endurance of machinery systems. Without these components, systems run the risk of lubricant leakage, leading to increased wear and tear, overheated systems, and ultimately, costly downtime. As such, their financial and operational value is immense, often reflected in metrics such as extended uptime, decreased repair costs, and enhanced operational safety.
For industries ranging from automotive to aerospace, oil seal hubs are more than mechanical components—they are essential contributors to the smooth and efficient operation of complex systems. When selecting and implementing these seals, considerations around materials, environmental conditions, and manufacturing integrity are not merely best practices; they are necessities in ensuring long-term success and mechanical health. By investing in quality oil seal hubs and adhering to expert-guided maintenance protocols, businesses can safeguard their equipment investments, fortify operational efficiency, and sustain competitive advantages in their respective fields.