Hydraulic pump oil seals play a critical role in ensuring the efficiency and longevity of hydraulic systems across various industrial applications. It's paramount to understand and apply best practices when selecting and maintaining these seals to optimize performance and prevent costly downtime. Drawing from extensive industry experience and a deep understanding of the intricacies involved, this article breaks down the essentials of hydraulic pump oil seals.
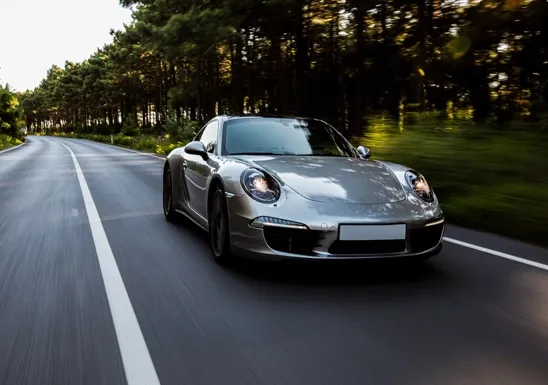
Hydraulic systems rely heavily on fluid pressurization to transmit power, making the integrity of the hydraulic pump oil seals of utmost importance. These seals are used to prevent oil leakage and to keep out contaminants that could potentially impair the system's functionality. Selecting the right oil seal is the first step towards achieving a reliable system performance. One must consider factors such as temperature range, pressure fluctuations, and the types of fluids being used. Oil seals are typically made from durable materials like nitrile rubber, fluoroelastomer, or silicone, each offering varying resistance levels to temperature and chemical exposure.
The expertise required in selecting the appropriate seal extends beyond material selection. One must also assess the operational environment. For example, in applications where there is significant vibration or misalignment, a seal with enhanced flexibility might be required. Conversely, in high-pressure environments, a rigid seal design could be more effective.
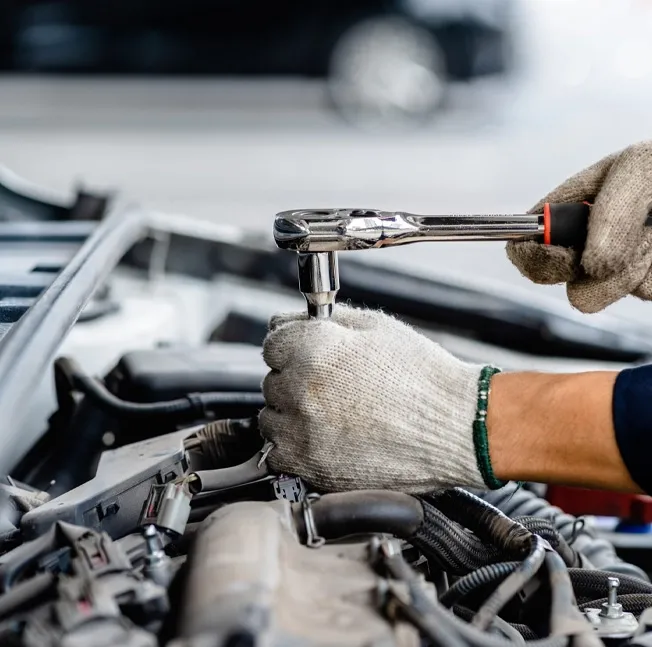
Trustworthiness in hydraulic pump oil seals is often derived from the manufacturer’s credibility and industry certifications. Working with manufacturers that offer comprehensive testing and meet stringent standards such as ISO 6194 for rotary shaft lip seals can significantly reduce risks associated with component failures. Certified seals provide an assurance of quality and durability, offering peace of mind during system operation.
hydraulic pump oil seal
Regular maintenance is another critical aspect of managing hydraulic pump oil seals. Even the most reliable seals need periodic inspection to check for wear and tear. Routine checks can help detect early signs of seal degradation, such as oil leakage or unusual noises during operation. Implementing a proactive maintenance strategy not only extends the seal's life but also avoids sudden system failures, thereby enhancing system reliability and cost efficiency.
Expert knowledge in hydraulic systems advocates for a strategic approach to oil seal replacement. It is often more advantageous to conduct a complete system review periodically rather than replace individual components reactively. This approach ensures all parts are operating at peak efficiency and can prevent unforeseen disruptions to operations. Keeping detailed logs of replacement schedules, materials used, and environmental conditions can serve as a valuable reference to fine-tune future selections and maintenance routines.
The authoritative voice in hydraulic components often emphasizes the importance of innovation and continual improvement. As technology advances, so do the materials and designs of hydraulic pump oil seals, incorporating features such as enhanced abrasion resistance, greater flexibility, and improved temperature tolerance. Staying informed about the latest developments and updates from leading manufacturers keeps professionals ahead of the curve.
In conclusion, hydraulic pump oil seals are indispensable components that demand careful selection and diligent maintenance to ensure optimal performance of hydraulic systems. Building a reliable system requires more than just the right parts—it requires an informed and strategic approach grounded in experience, expertise, authority, and trustworthiness. By following these principles, industries can achieve sustained efficiency and resilience in their hydraulic operations.