The skeleton oil seal, often overlooked yet indispensable in diverse industrial applications, plays a critical role in machinery reliability and efficiency. Unlike decorative skeletons associated with Halloween, this component serves a functional purpose that demands technical understanding and precision. Everyday, industries ranging from automotive to manufacturing rely on the unyielding performance of skeleton oil seals to maintain operational fluency and prevent costly downtimes.
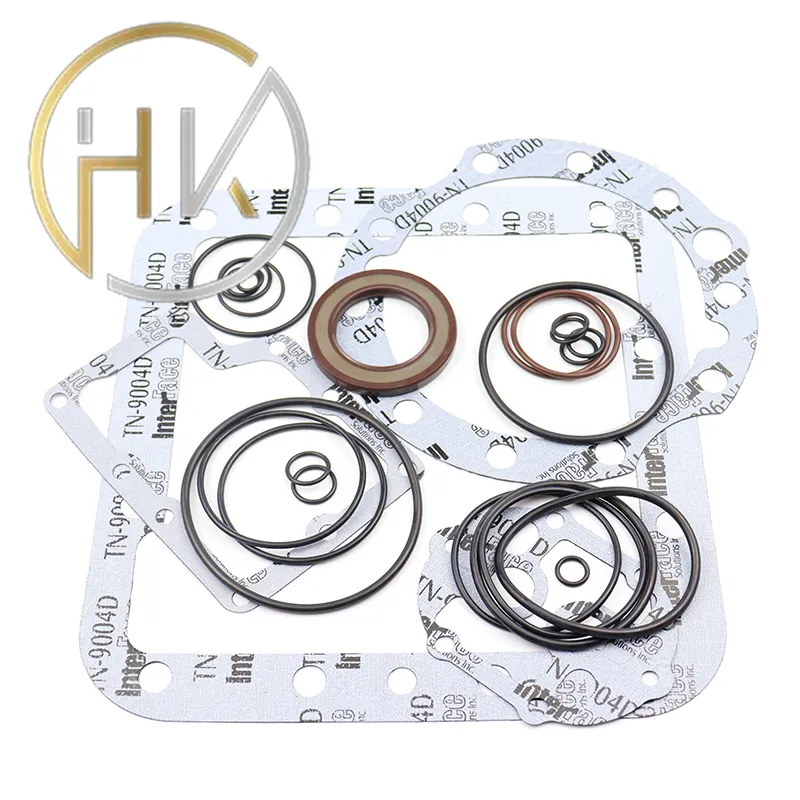
A skeleton oil seal performs the essential task of sealing lubricants within a machine's gearbox, engine, or any system operating under conditions that require tight fluid containment. By preventing leakage, it ensures that the equipment functions at optimal efficiency, thereby extending the machinery's service life. Equally important, the seal acts as a barrier against contaminants such as dirt and moisture, which could otherwise compromise the machinery's components. Such capability underpins its necessity in maintaining equipment longevity and minimizing maintenance costs.
Hailing from decades of engineering expertise, the design of skeleton oil seals is a testament to precision craftsmanship. These seals typically comprise a metal ring, often made from high-grade steel or other robust alloys, which acts as the support structure. Encasing the metal is a rubber or polymer-based elastomer that conforms to the shaft, creating the critical sealing barrier. This composite structure ensures durability and resilience, even in challenging environments characterized by extreme temperatures and pressures.
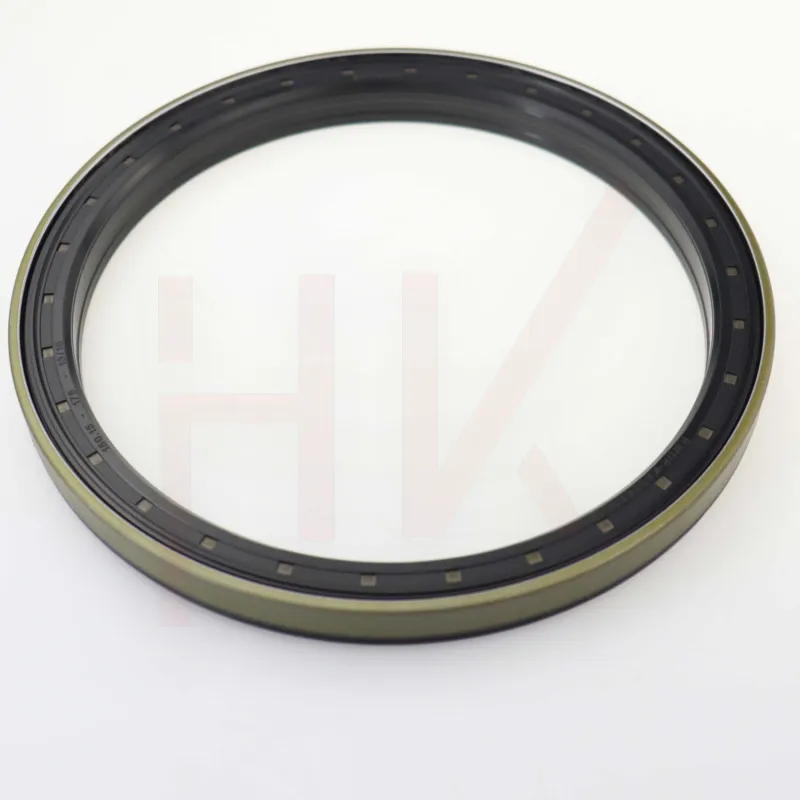
An essential feature that highlights the skeleton oil seal's superior functionality is its lip design. This design is meticulously engineered to exert an optimal force on the rotating shaft, balancing the need for effective sealing with minimal friction. The result is a component that can withstand rotational speeds, varied viscosities of lubricants, and even the corrosive nature of certain fluids.
In terms of market relevance, the skeleton oil seal stands out as a preferred choice amongst engineers and maintenance professionals globally, a testament to its authoritative role in industrial settings. As equipment becomes more sophisticated, the demand for reliable sealing solutions escalates, making the skeleton oil seal's contribution all the more critical.
skeleton oil seal
Evaluation by industry experts and rigorous testing in line with ISO certifications further attest to its credibility and trustworthiness. For those in the procurement department or maintenance crew, choosing a skeleton oil seal manufactured by a reputable company is imperative. This decision is supported by years of research and development dedicated to enhancing its material properties and performance benchmarks.
Despite its critical role, the skeleton oil seal should not be mistaken for a one-size-fits-all solution. Different machinery specifications necessitate tailored solutions regarding size, material composition, and lip geometries. Understanding these variables and consulting with technical specialists can significantly enhance operational efficiency and machinery performance.
The ascent of Industry 4.0 has further underscored the reliance on traditional components such as the skeleton oil seal, urging manufacturers to innovate and adapt these products for new tech-driven environments. Advanced materials, including high-performance elastomers, are being developed to tandem with digital twin models, allowing for predictive maintenance — a leap toward smarter and more reliable machine operation.
In conclusion, while the skeleton oil seal might silently do its job behind the scenes, its influence on machine performance and maintenance cannot be overstated. As industries evolve, its foundational role as a barrier against wear and inefficiency only continues to grow, cementing its status not only as a crucial component but also as a strategic investment in prolonging machinery lifespan and reducing operational costs.