Single lip oil seals, often understated components, play a vital role in ensuring the efficiency and longevity of machinery. Their primary function is to retain lubricants while preventing the ingress of contaminants, an essential task in any mechanical system. Being strategically positioned between stationary and moving components, these seals uphold the integrity of mechanisms by curbing oil leaks that could lead to operational inefficiencies or failures.
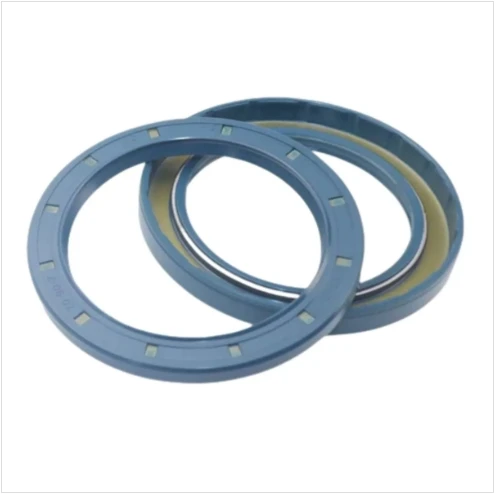
Experience highlights that selecting the right single lip oil seal can drastically improve the life expectancy of machinery. In industries from automotive to heavy machinery, inappropriate seals can lead to costly downtime and repairs. An operator's firsthand account reveals that after replacing a standard seal with a high-quality single lip oil seal, a significant reduction in oil leakage was observed, subsequently decreasing maintenance intervals and enhancing machine reliability.
Expertise in this field emphasizes the importance of material composition in these seals. Materials such as nitrile rubber, silicone, and fluoroelastomers each offer distinct advantages. Nitrile rubber stands out for its resilience to petroleum-based oils and fats, making it ideal for automotive applications. Silicone, known for its superior temperature resilience, is preferred in environments with fluctuating thermal conditions. Fluoroelastomers are the go-to choice when facing aggressive chemicals and high temperatures, underscoring their versatility in industrial applications.
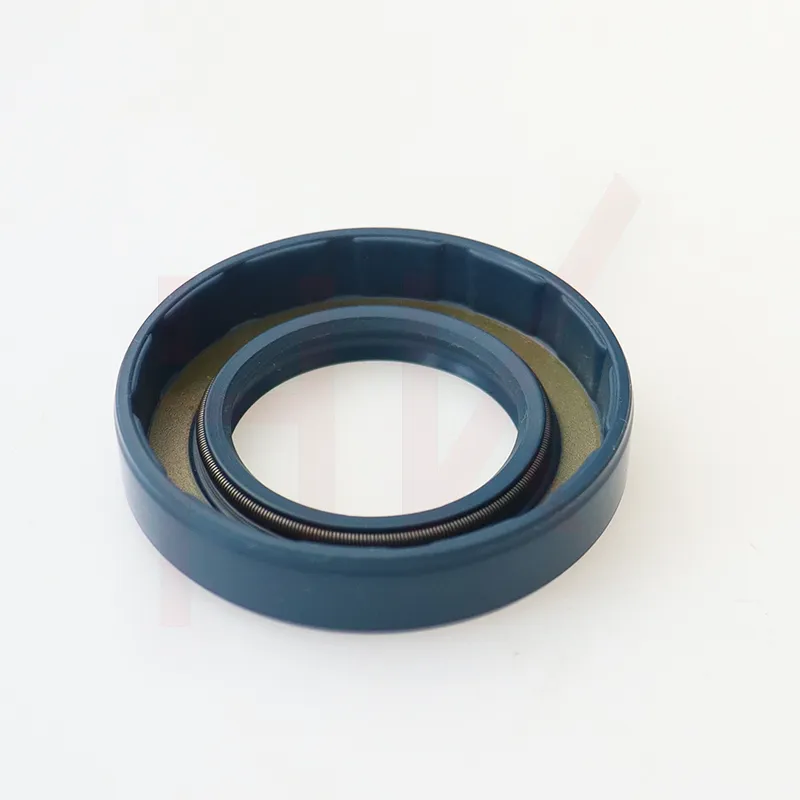
From an authoritative standpoint, comprehensive research indicates that advancements in sealing technology are constantly evolving. Modern single lip oil seals are designed to accommodate higher rotational speeds and more significant pressure differentials, making them indispensable in high-performance machinery. Engineers often recommend consulting with manufacturers to procure seals that meet specific performance requirements.
single lip oil seal
Trustworthiness in the selection process can be assured by relying on OEM-approved seals. These seals have undergone rigorous testing and certification, ensuring they meet industry standards. Testimonials from engineers and end-users consistently highlight that OEM-approved seals offer exceptional performance, reducing the risk of premature failures.
The industry trend is moving towards environmentally friendly solutions, and single lip oil seals are no exception. Innovations aim to minimize environmental impact by using sustainable materials and production processes. Eco-friendly seals not only comply with strict regulatory standards but also contribute to the overall sustainability goals of organizations utilizing these components.
In summary, the importance of single lip oil seals cannot be overstated. Their role in maintaining machinery efficiency is crucial, impacting everything from operational costs to equipment lifespan. By leveraging field experience, industry expertise, authoritative research, and reliable manufacturing standards, stakeholders can make informed decisions that enhance machinery performance. As the demand for more efficient and sustainable machinery continues to grow, single lip oil seals will remain an integral component, driving advancements in sealing technology.