Understanding the intricacies of single-acting piston seals unveils a realm of mechanical efficiency and reliability essential for various industrial applications. These seals play a pivotal role in ensuring the optimal performance of machinery, particularly in hydraulic systems, where maintaining effective pressure control and preventing fluid leakage are paramount.
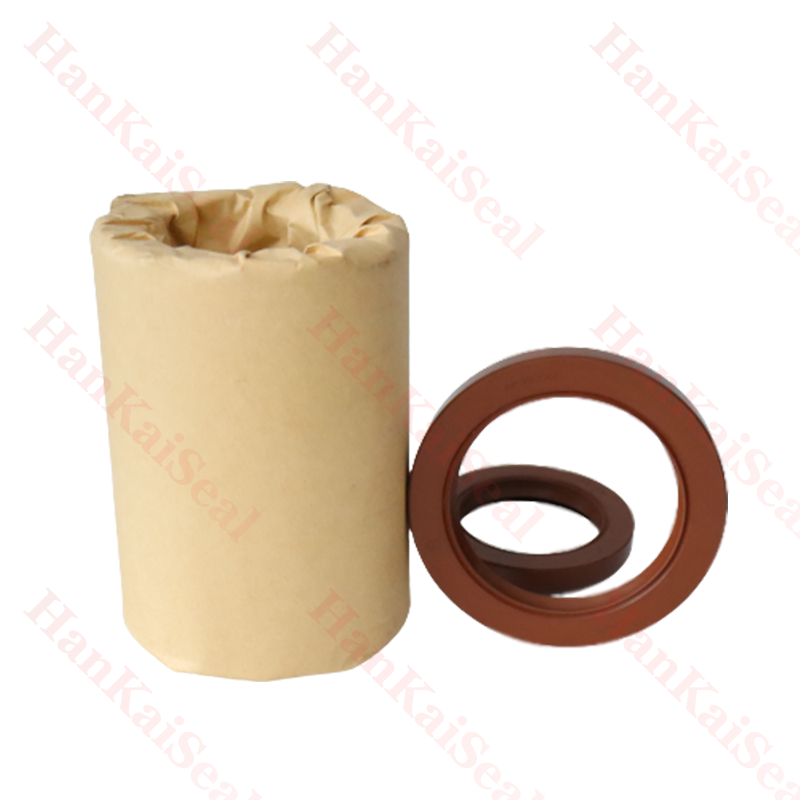
Single-acting piston seals are designed to facilitate linear motion by creating a seal between the piston and the cylinder bore. Their unique function revolves around sealing in one direction only, making them indispensable in uni-directional hydraulic systems. When utilized appropriately, these seals enhance the longevity and efficiency of mechanical systems, minimizing downtime and reducing maintenance costs.
In practical applications, the choice of a single-acting piston seal is influenced by several factors including pressure ratings, temperature ranges, and the type of fluid it will encounter. Experts consistently advise selecting materials and designs tailored to specific operational environments to maximize seal performance. Common materials like polyurethane, rubber, and PTFE are often chosen for their specific attributes such as flexibility, heat resistance, and chemical compatibility. Engineers and technicians prioritize compatibility with hydraulic fluids to prevent degradation, which could otherwise lead to system failures.
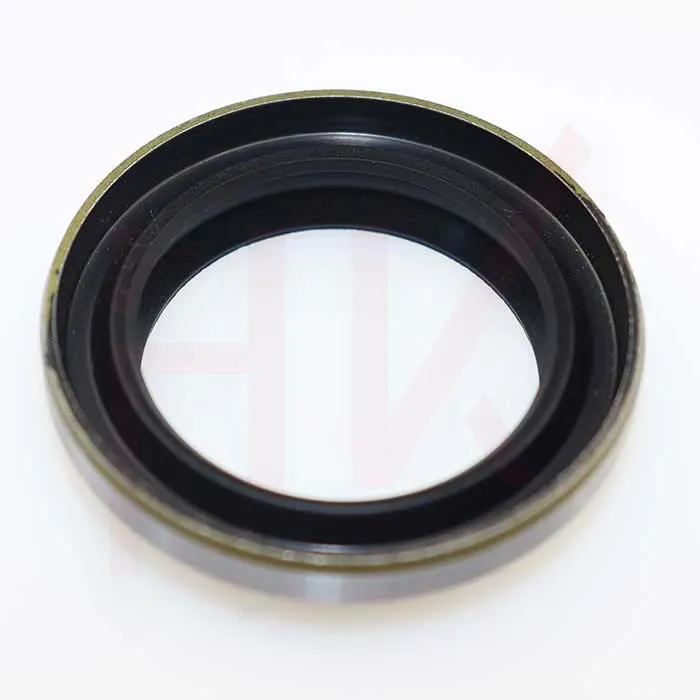
The performance of single-acting piston seals is heavily contingent upon their physical and mechanical properties. Precision engineering ensures these seals provide the necessary frictional forces to prevent leaks while allowing the piston to navigate efficiently within the cylinder. High-quality seals are characterized by minimal wear and consistent performance over extended periods, even under fluctuating pressures and extreme conditions.
In terms of authority and reliability, industry leaders continuously refine seal designs to meet evolving technological demands. Companies specializing in seal manufacturing employ advanced technologies and testing methodologies to produce seals that meet international standards of quality and durability. This commitment to excellence establishes their products as trustworthy solutions in the market.
single acting piston seal
User experience plays a crucial role in the ongoing evolution of single-acting piston seals. Field data provides invaluable insights into real-world performance, leading to iterative improvements. Feedback from engineers and end-users is instrumental in enhancing material compositions and seal configurations. It’s not uncommon for field reports to highlight areas for improvement, such as the need for greater pressure thresholds or enhanced resistance to hazardous chemicals.
Expertise in the field of single-acting piston seals is marked by a deep understanding of hydraulic system dynamics. Professionals in this domain leverage theoretical knowledge and practical experience to devise sealing solutions that optimize machinery performance. Specialized training in fluid dynamics, materials science, and mechanical engineering underpins the design and application of these seals, ensuring they meet the specified requirements for various applications from heavy industrial machinery to precision medical devices.
Trust in single-acting piston seals is cultivated through rigorous testing and certification processes. Reliability tests simulate real-world conditions to validate seal integrity, performance, and lifespan. Manufacturers often engage in partnerships with independent testing agencies to verify product claims, bolstering consumer confidence. These certifications not only affirm the quality of the seals but also enhance their market reputation.
In conclusion, single-acting piston seals are fundamental components in the quest for mechanical precision and efficiency. Their adept design and application reflect a confluence of expertise, experience, and reliability, integral to a wide array of industrial operations. As technology continues to advance, so too will the innovation surrounding these seals, reinforcing their status as trusted elements within the mechanical and engineering sectors. Pioneering research and development in this area promise continued enhancements, underlining the critical importance of these components in modern machinery.