Replacing seals in a hydraulic cylinder is an essential task to ensure the efficiency and longevity of hydraulic systems, which are pivotal in numerous industries, from manufacturing to agriculture. A hydraulic cylinder functions as the muscle of any hydraulic system, converting fluid energy into mechanical energy. When a cylinder seal fails, it can lead to inefficiency, safety issues, and equipment downtime, making it crucial to address seal replacement promptly and correctly.
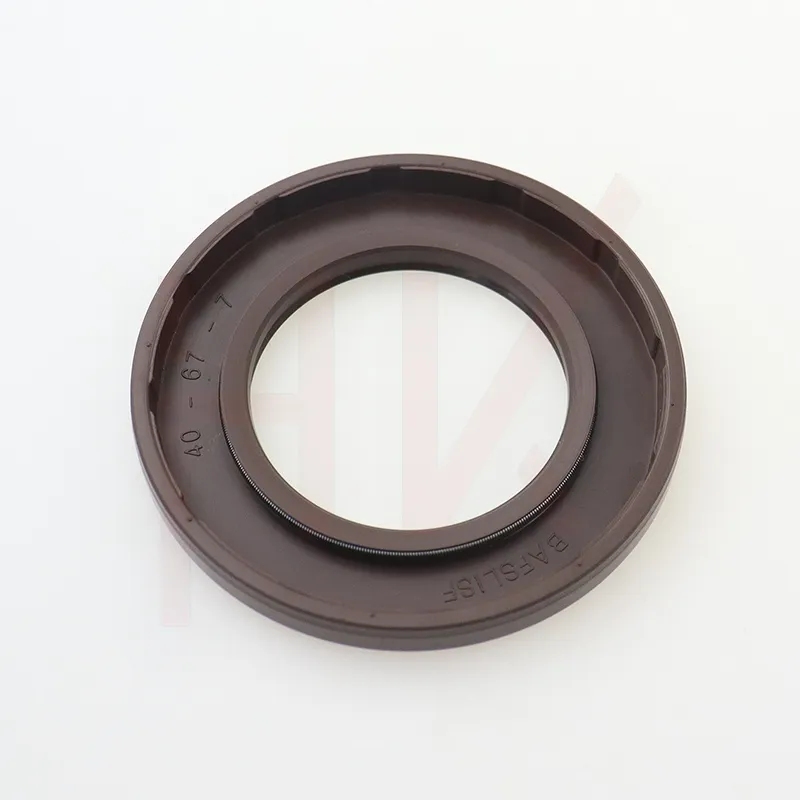
Before diving into the seal replacement process, it’s important to understand the different types of seals used in hydraulic cylinders, including rod seals, piston seals, wiper seals, and wear bands. Each type plays a specific role; for instance, the rod seal prevents leakage from inside the cylinder to the outside, while the piston seal prevents fluid from passing through the piston within the cylinder. Knowing the function of each seal helps in diagnosing problems and understanding replacement needs.
The first step in replacing hydraulic cylinder seals is a thorough inspection. Begin with a visual assessment to identify any visible damage or wear. Look for signs of leakage, which might indicate a worn or damaged seal. If the system exhibits erratic operation or reduced performance, these too can be indicators of seal degradation. Accurate diagnosis is essential to ensure that only the necessary components are replaced, saving both time and resources.
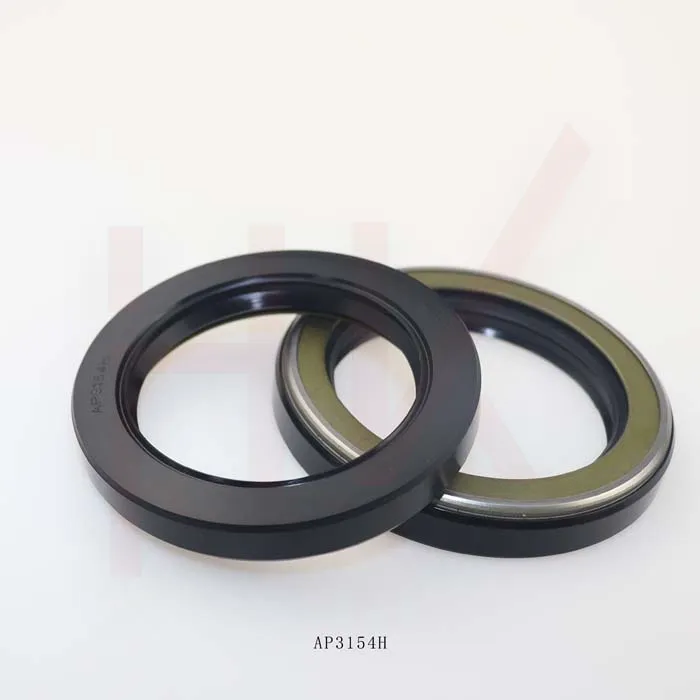
Once the need for seal replacement is confirmed, the hydraulic cylinder should be safely removed from the system. This involves depressurizing the system and securing the machinery to prevent accidents. Safety cannot be overstated; even a small hydraulic system contains tremendous pressure capable of causing serious injury.
With the cylinder removed, the next step is disassembly. This process begins by loosening and removing the locking ring or flange bolts to access the rod assembly. As you withdraw the piston rod, take care to protect the surface from scratches or dings, which could affect the seal’s effectiveness. During disassembly, it’s wise to lay components out in order as they are removed, creating a visual map that aids in reassembly.
replacing seals hydraulic cylinder
After gaining access to the seals, carefully remove them using appropriate tools. Avoid using sharp objects that could damage the grooves or the cylinder itself. Examine each seal to understand its condition, and compare it with new seals to ensure the correct type and size are used. Investing in high-quality seals is recommended, as these are more resistant to wear and damage, extending the maintenance interval.
The actual replacement process involves thoroughly cleaning all parts to eliminate old lubricants and debris, which could compromise the new seals. Once cleaned, install the new seals carefully, ensuring they sit properly in their grooves. Lubricating the seals with a manufacturer-recommended oil helps with installation and enhances initial performance.
Reassembly must be done with equal attention to detail. Ensure all parts are aligned correctly to prevent uneven wear and corresponding failure. Tighten all fittings to the specified torque requirements to prevent leaks and maintain structural integrity.
Lastly, once the hydraulic cylinder is reassembled and reinstalled, test the system under load to confirm the repair was successful. Check for leaks and ensure the cylinder operates smoothly. Routine checks thereafter can extend the life of the seals and the cylinder, contributing to consistent system performance.
Replacing seals in a hydraulic cylinder, when done right, restores the system’s efficiency and reliability. A successful replacement demands careful preparation, attention to detail, and a commitment to safety, underscoring the critical nature of expertise and experience in hydraulic repair tasks. Whether you are a seasoned technician or learning the ropes, these practices will guide you to execute effective maintenance, enhancing trust with clients or stakeholders relying on these powerful systems.