In the intricate world of machinery maintenance, the role of metal-cased oil seals often goes underestimated. These silent stalwarts are pivotal in ensuring that machinery functions seamlessly, preventing the ingress of contaminants and the egress of lubricants. For engineers and machine operators aiming to achieve peak performance and longevity of their equipment, metal-cased oil seals offer unmatched reliability.
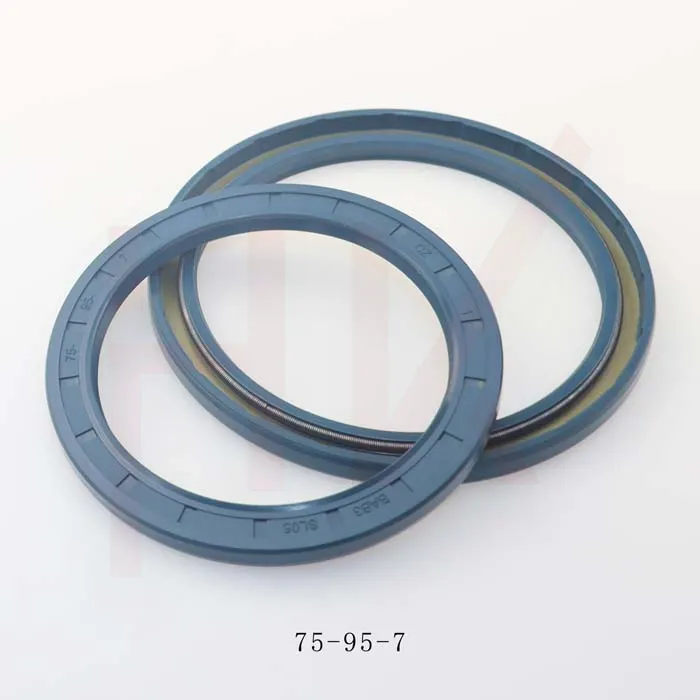
Understanding metal-cased oil seals begins with a grasp of their construction. Typically forged from high-quality metal materials, these oil seals boast a robust structure that withstands extreme operating conditions. This metal casing provides superior resistance to pressure and temperature variations compared to their non-metal counterparts. When integrated into industrial applications, these seals effectively manage the separation of different fluids, which is critical in preventing cross-contamination and ensuring optimal performance.
Moreover,
metal-cased oil seals excel due to their durability. In industries such as automotive, aerospace, and heavy machinery where high-speed rotations and pressures are commonplace, having a seal that can endure such rigorous demands is indispensable. The metal casing serves as a formidable barrier against physical wear and tear, significantly extending the lifespan of both the seal and the machinery it's employed within. This resilience not only reduces downtime due to equipment failure but also diminishes maintenance costs, offering a substantial return on investment.
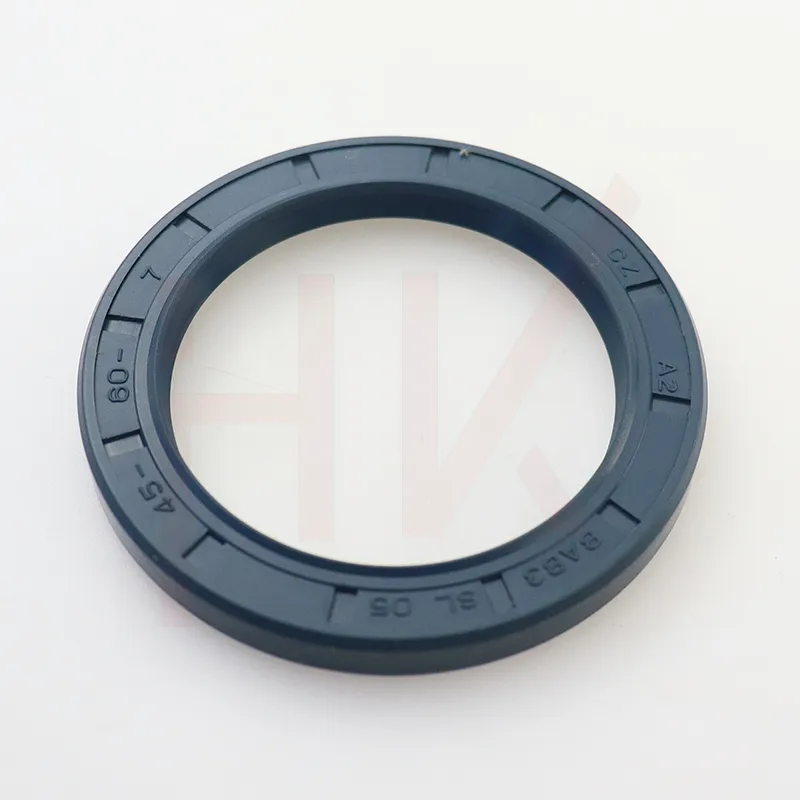
From an expertise standpoint, fitting and selecting the appropriate metal-cased oil seal requires an understanding of specific operational demands. Professionals in the field must consider factors such as shaft speed, environmental conditions, and the type of lubricant being retained. This precision in selection is critical; an ill-suited seal could jeopardize machinery performance, leading to costly repairs and replacements. Thus, manufacturers provide detailed specifications and guidelines, ensuring that users select the correct seal for their particular application.
metal cased oil seals
In terms of authoritativeness, metal-cased oil seals have been endorsed by leading engineering experts and associations. Their efficacy in preserving machine integrity has made them the preferred choice in sectors that place a premium on operational reliability. Industry giants, recognizing the cost-efficiency and durability of these seals, integrate them into their equipment design, further cementing their status as a vital component in the engineering landscape.
When it comes to trustworthiness, user testimonials and case studies abound, showcasing the success of metal-cased oil seals in real-world applications. Reports illustrate consistent performance, even in the harshest environments, bolstered by rigorous quality assurance practices employed in their manufacturing. Trusted globally, these seals have demonstrated their capacity to uphold their integrity over extended periods, providing a reliable solution for industry engineers.
In conclusion, metal-cased oil seals represent a blend of engineering ingenuity and practical application, central to the smooth operation of various mechanical systems. With their robust design, unmatched durability, and proven track record, they offer an indispensable solution for anyone seeking to enhance the efficiency and effectiveness of their machinery. For those invested in maximizing their equipment's potential, the metal-cased oil seal is not merely a component but a cornerstone of operational excellence.