In the vast landscape of industrial machinery and equipment, hydraulic systems play an integral role, enabling the transfer of energy through fluids. One of the crucial components ensuring the efficiency and reliability of hydraulic systems is the piston seal. If you're in the field of engineering or maintenance, understanding the hydraulic piston seal kit is paramount to maintaining optimized system performance.
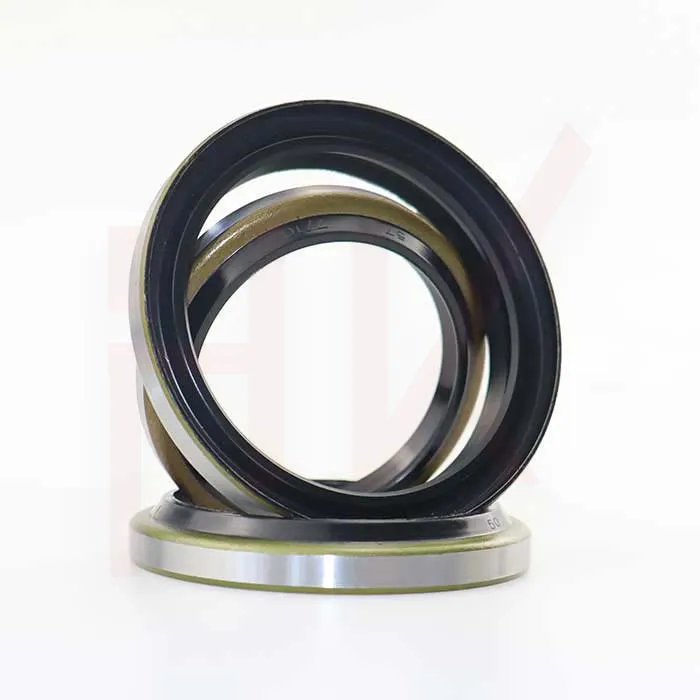
Hydraulic piston seals are crucial for maintaining a tight barrier between fluid and environmental contamination. They are specifically designed to prevent leakage and manage the pressure applied within a hydraulic cylinder. Recognizing the nuances of a hydraulic piston seal kit and its components can drastically impact the operational efficiency and longevity of your equipment, thus enhancing productivity and minimizing downtime.
Expertise in selecting the right hydraulic piston seal kit requires knowledge of the materials, environmental conditions, and specific machinery requirements. A key factor to consider is the compatibility of the seal material with the fluid used in the hydraulic system. For instance, seals made from materials like nitrile rubber (NBR), polyurethane (PU), or polytetrafluoroethylene (PTFE) offer different levels of durability and resistance to temperature and chemical exposure.
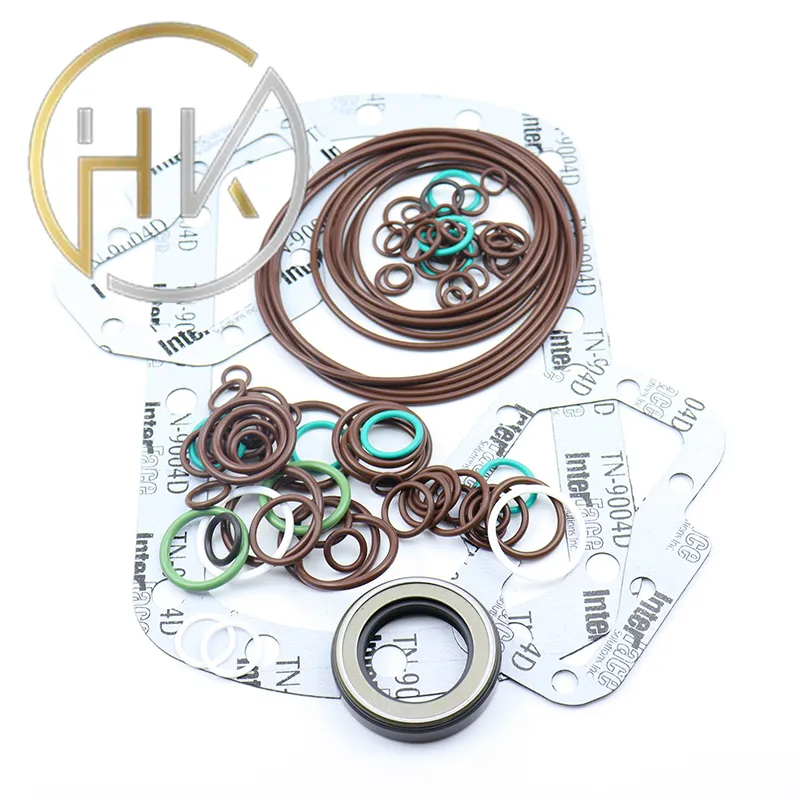
Nitrile rubber is often favored for its balance of cost-effectiveness and robustness against oil-based fluids and grease. It is an excellent option for systems where temperature variations are moderate. Conversely, polyurethane stands out for its high tear and abrasion resistance, making it ideal for more demanding applications where mechanical stress is a concern. PTFE seals, renowned for their excellent performance under extreme temperatures and chemical resistance, are best suited for high-intensity environments.
When dealing with hydraulic systems, the environment in which your equipment operates is essential. Factors such as temperature extremes, contamination risk, and exposure to chemicals or moisture must be evaluated to select the appropriate seal. Understanding these elements helps prevent premature wear and potential system failures.
hydraulic piston seal kit
An experienced technician will also recognize the importance of proper installation and inspection routines. A hydraulic piston seal kit typically includes a variety of seals such as wiper seals, rod seals, and static seals, each serving a unique purpose. Ensuring these seals are correctly installed minimizes the possibility of leaks and optimizes performance. Regular inspection and maintenance schedules, guided by equipment manufacturers, can greatly enhance the seal’s lifespan and functionality.
Authoritativeness in the field requires staying informed about industry advancements. For instance, the development of enhanced seal designs and materials, such as the integration of advanced composite materials, offers improved performance capabilities. Keeping abreast of such technological advancements allows professionals to make informed decisions that enhance system resilience and efficiency.
Trustworthiness stems from sourcing hydraulic piston seal kits from reputable manufacturers. Partnering with providers that adhere to high manufacturing standards and offer comprehensive technical support ensures the reliability of their products. This decision not only affects immediate operational needs but also contributes to long-term relationship building with suppliers and clients.
A trusted source will generally offer extensive documentation on product specifications, installation, and maintenance practices. Such resources are invaluable for training new personnel and ensuring consistent service delivery. Additionally, they often provide technical support services for troubleshooting unexpected issues that may arise, reinforcing their commitment to customer satisfaction.
In conclusion, the role of a hydraulic piston seal kit in industrial applications cannot be understated. By focusing on areas such as material compatibility, environmental factors, proper maintenance, and engaging with trusted suppliers, professionals can significantly boost system reliability and performance. Such comprehensive attention to detail not only reduces operational risks but also enhances the overall efficiency and life cycle of hydraulic machinery.