The hydraulic cylinder dust seal is a critical component in various industrial and heavy machinery applications, ensuring optimal functionality and durability. These seals serve as the first line of defense, protecting hydraulic cylinders from external contaminants like dust, dirt, and moisture, which can significantly hamper machine performance and longevity. Understanding their importance, installation, and maintenance can ensure efficiency and prevent costly repairs or replacements.
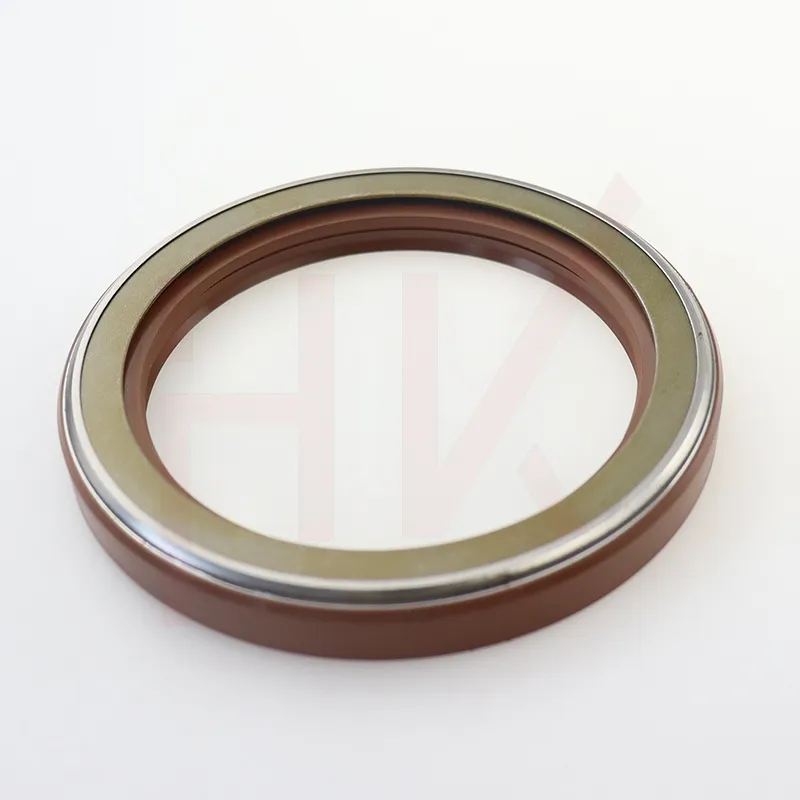
Hydraulic systems are prevalent across numerous sectors, from agriculture to construction and mining. Each of these industries relies heavily on machines that experience harsh operating environments. The dust seal, though small, plays a vital role in preserving the integrity and performance of these hydraulic systems. Its primary function is to prevent foreign particles from entering the system, which could otherwise mix with hydraulic oil, leading to abrasion and damage to the internal components.
The choice of material for hydraulic cylinder dust seals is pivotal. Modern dust seals are usually made from flexible yet resilient materials such as nitrile rubber, polyurethane, or polytetrafluoroethylene (PTFE). These materials are chosen for their ability to withstand high temperatures, pressure, and the chemical nature of hydraulic fluids while maintaining their elastic properties to effectively contain contaminants.
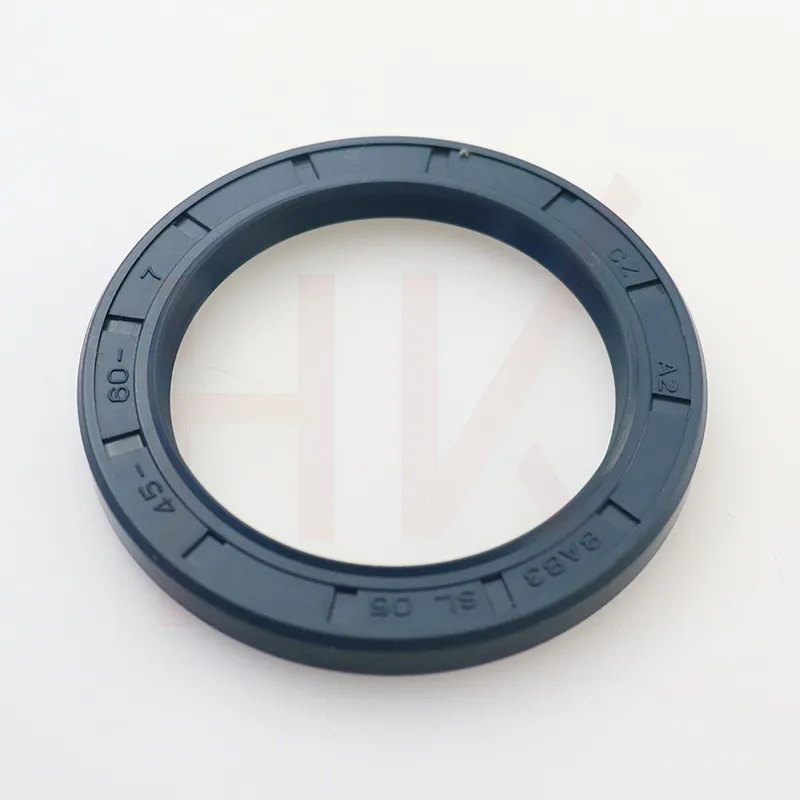
Proper installation of a hydraulic cylinder dust seal ensures optimal performance. Incorrect installation can lead to premature wear and tear, resulting in potential system failures. It is crucial to follow the manufacturer’s specific guidelines when installing these components. The process typically involves cleaning the gland and rod thoroughly, inspecting the groove dimensions, and using the appropriate tools to avoid seal deformation. Implementing these steps ensures a tight fit and prolonged seal life, which directly translates to fewer maintenance requirements and greater cost efficiency.
hydraulic cylinder dust seal
Regular inspection and maintenance of dust seals can significantly enhance the lifespan of hydraulic systems. Regular checks for signs of wear, such as brittleness or cracking, can help prevent a malfunction. If a seal shows any signs of deterioration, it should be replaced immediately. Additionally,
ensuring the hydraulic fluid is clean and free of contamination is essential. Using high-quality oils and regularly replacing filters can complement the effectiveness of dust seals, providing a robust defense against contamination.
For industries operating in particularly harsh environments, investing in high-performance dust seals can have substantial benefits. Enhanced dust seals often have additional features like double lip designs or stronger materials specifically designed to withstand more aggressive conditions. Though these may incur higher upfront costs, the long-term savings on maintenance and increased machine uptime provide a favorable return on investment.
An understanding of the failure modes of hydraulic cylinder dust seals is also crucial for professionals in the field. Common failure modes include hardening due to heat, as well as physical damage from debris knock-ons. Recognition of these issues can lead to better diagnosis and preventative measures, reducing the likelihood of unscheduled downtimes.
In summary, hydraulic cylinder dust seals are a vital yet often overlooked component of hydraulic systems that contribute greatly to the reliability and efficiency of machinery. Ensuring their proper selection, installation, and maintenance is essential to keep systems running smoothly. By investing in quality seals and adhering to a rigorous maintenance routine, industries can significantly enhance system longevity and performance, thereby maintaining a competitive edge in their operations. Implementing these strategies, businesses can not only save on costs related to repairs and replacements but also optimize the productivity and safety of their operations.