Bearing dust seals play a critical role in the longevity and efficiency of machinery across various industries, including automotive, aerospace, and manufacturing. These components, while often considered secondary to the bearings themselves, are essential in ensuring that machines operate smoothly over extended periods. Here, we delve into the significance and advantages of bearing dust seals.
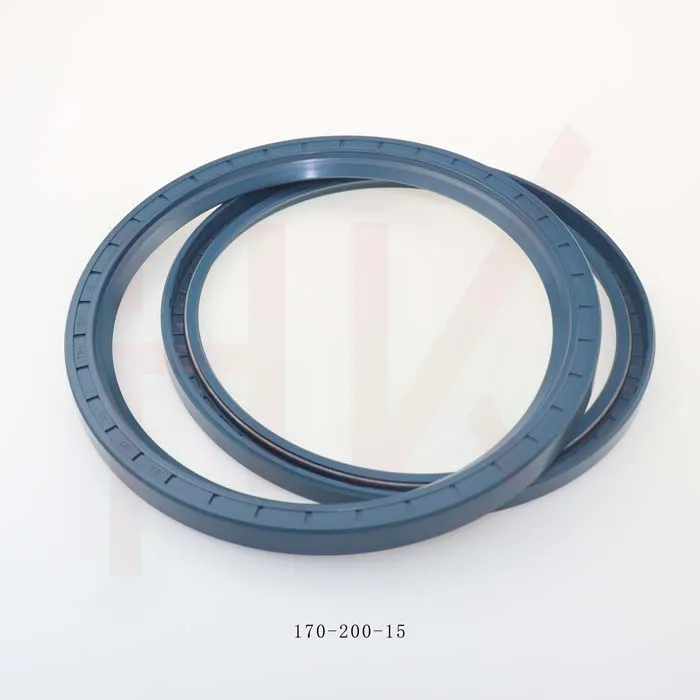
Renowned for their protective capabilities, bearing dust seals serve as the first line of defense against contaminants such as dirt, dust, and moisture. These adversaries, seemingly harmless at first, can wreak havoc on the intricate workings of a bearing, leading to premature wear and eventual failure. By preventing such intrusions, dust seals not only enhance the lifespan of the bearings but also maintain the overall performance of the machinery.
In industries where operational precision is paramount, such as aerospace, the importance of bearing dust seals cannot be understated. Aircraft systems, for instance, are subjected to varying atmospheric conditions, which can introduce contaminants into bearing housings. Dust seals in this context become vital, safeguarding components and ensuring passenger and crew safety.
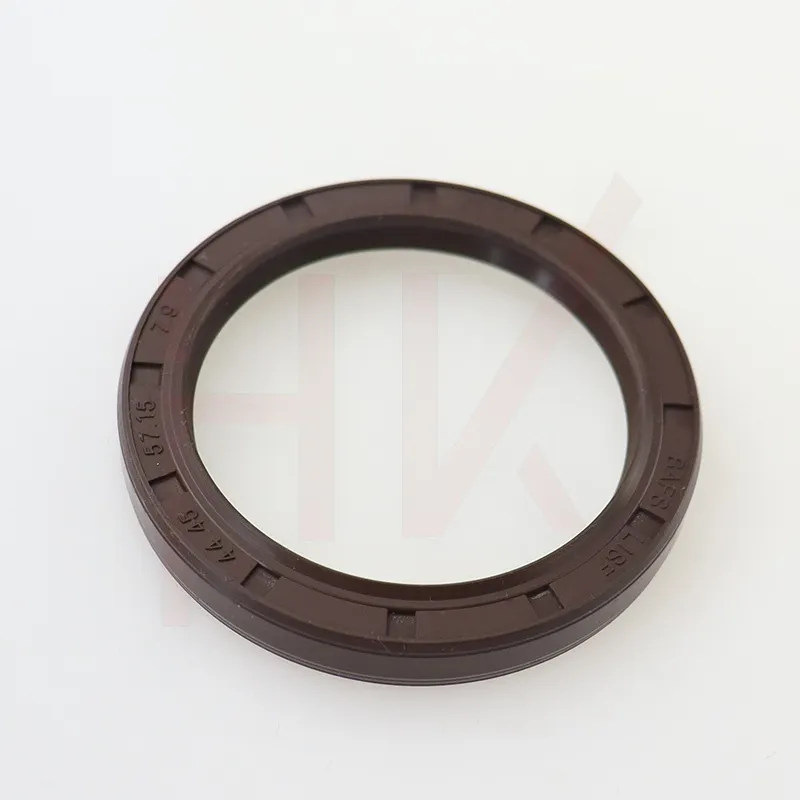
From a practical experience standpoint, many industrial maintenance engineers have witnessed the stark contrasts presented by systems equipped with and without effective dust seals. Machines with robust sealing mechanisms typically boast longer maintenance intervals. This reduction in downtime translates directly to cost savings, reinforcing the financial viability of investing in quality dust seals. Moreover, the peace of mind that comes with reliability cannot be quantified, especially in high-stakes sectors like manufacturing, where unscheduled maintenance can halt production lines.
bearing dust seal
For those in the automotive industry, the expertise surrounding bearing dust seals is indispensable. Wheel bearings, for example, operate in environments exposed to road debris and moisture. Herein, dust seals shield the bearings from external threats, thus maintaining vehicle performance and safety. Mechanics often emphasize the importance of regular seal inspections during routine maintenance, recognizing that any compromise in the seal can lead to cascading mechanical issues.
Authoritativeness in the field of bearing technology frequently calls attention to materials used in the fabrication of dust seals. Advances in polymer science have led to seals constructed from durable synthetic materials resistant to heat and chemical degradation. Such developments reflect a broader trend towards engineering solutions that address the rigorous demands of modern machinery, ensuring that bearings remain protected regardless of environmental challenges.
Moreover,
trustworthiness in product selection is paramount. Engineers and technicians alike rely on seals from manufacturers with proven track records. Companies that provide detailed specifications, backed by stringent testing protocols, inspire confidence in their ability to deliver components that meet industry standards.
In conclusion, bearing dust seals, while simple in function, are indispensable in protecting the integrity of bearings across numerous applications. Their contribution to machinery longevity, operational excellence, and cost-efficiency underscores their value in any mechanical system. By choosing the right seal, investing in quality materials, and adhering to regular maintenance schedules, industries can look forward to extended equipment lifespans and enhanced performance. The ongoing innovation in seal technology promises even greater advancements, solidifying the foundation upon which modern machinery thrives.