The Hidden Potential of 25 47 7 Oil Seals A Comprehensive Guide to Quality and Performance
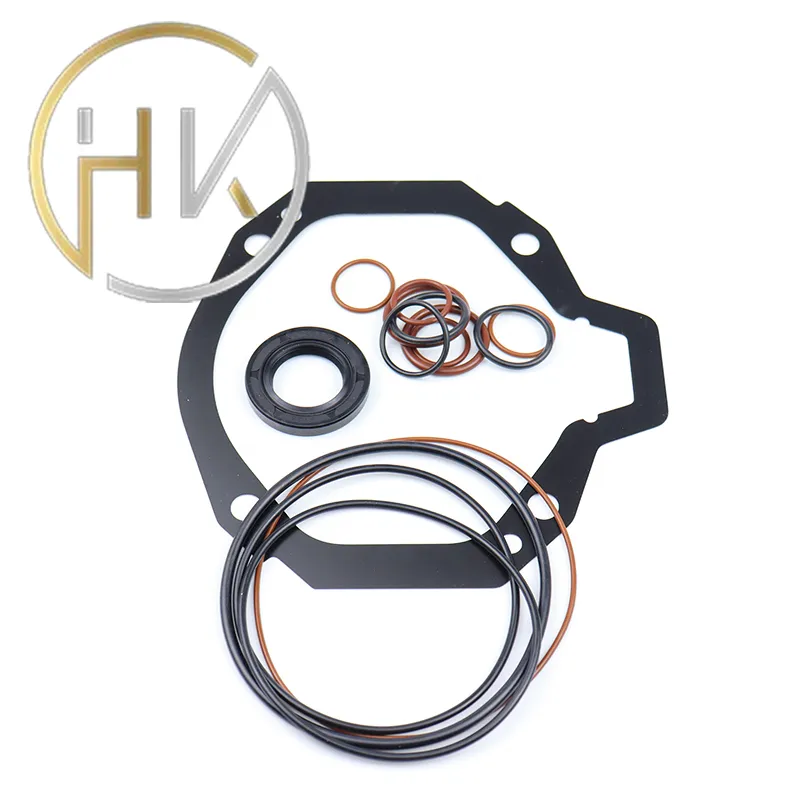
In the realm of machinery and automotive engineering, small components often play an outsized role in determining the overall efficiency and lifespan of a machine. One such component is the oil seal, particularly the 25 47 7 oil seal, recognized for its meticulous design and notable contribution to mechanical reliability. As we delve into the intricacies of these oil seals, understanding their application and benefits not only enhances mechanical performance but also boosts trust in engineering processes.
Oil seals, sometimes referred to as rotary shaft seals, are invaluable in preventing lubricant leakage while also serving to stop harmful contaminants from penetrating the machinery. The dimensions of a specific oil seal, in this case, 25 47 7, indicate the internal diameter, external diameter, and width respectively, suggesting its suitability for specific shaft sizes. This precision in sizing ensures effective sealing and isotropic distribution of pressure, leading to optimal machine performance.
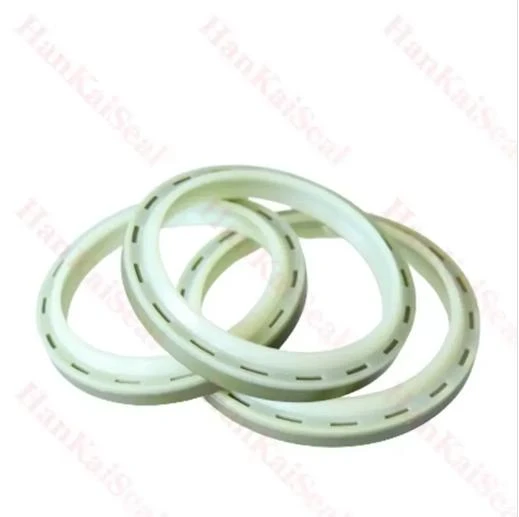
The real-world experience of using 25 47 7 oil seals reveals their robustness in various applications. From automotive engines to industrial machinery, these seals illustrate how accurate specifications can dramatically influence mechanical health. Users have reported prolonged engine life and reduced maintenance costs,
attributing these benefits to effective seal performance. Their ability to maintain consistent lubrication around the shaft leads to reduced friction and wear, hence extending the overall lifespan of the equipment.
Expertise in manufacturing these components demonstrates that the material composition of oil seals—usually consisting of high-quality rubber or thermoplastic elastomers—offers superior thermal and chemical resistance. This resistance ensures that the oil seals can perform in high-temperature environments and with different types of lubricants, an essential feature for maintaining integrity in demanding mechanical systems. Advanced manufacturing techniques have also introduced reinforcement with metals or other composite materials, adding structural strength without compromising flexibility.
25 47 7 oil seal
Authority in discussing oil seals such as the 25 47 7 variant stems from manufacturers who continuously innovate to meet the evolving demands of technology and machinery. By adhering to rigorous quality control standards and regulatory compliances, manufacturers ensure that each seal not only meets but exceeds expectations in real-world applications. Industry certifications further cement the reliability of these products, as they validate the seal's performance under multiple stress tests and lifecycle assessments.
Trustworthiness in the usage of 25 47 7 oil seals can also be attributed to comprehensive testing and validation processes. Engineers and maintenance professionals rely on test data that categorically show the seal's ability to function effectively even in extreme conditions, thereby securing machinery reliability. When machinery is equipped with such reliable components, businesses witness lower downtime and enhanced productivity, showcasing the broader economic impact of quality oil seals.
Moreover, innovations such as self-lubricating seals and smart monitoring systems are said to be the future of oil seals, contributing to predictive maintenance and IoT-based machinery management. These advancements point towards a trajectory where the humble oil seal becomes an integral part of intelligent machinery systems—offering not just sealing but contributing to a holistic understanding of machine health.
In conclusion, the 25 47 7 oil seal represents more than just a component in a machine; it symbolizes the synthesis of precise engineering, material science, and industry standards that promote longevity and efficiency. As machinery and automotive industries continue to evolve, the role of these seals becomes increasingly crucial. By understanding their design, application, and benefits, stakeholders can make informed decisions, ensuring machinery remains efficient, reliable, and cost-effective over its operational lifespan. It is a testament to how meticulous engineering and high-quality materials converge to define the benchmarks of mechanical reliability and performance.