Understanding the importance of 25 40 7 oil seals in mechanical applications is crucial for ensuring optimal performance and longevity of machinery. These oil seals play a pivotal role in preventing leakage of lubricants, thereby safeguarding the integrity of various mechanical systems. With expertise in mechanical engineering, let's delve deep into the multifaceted aspects of 25 40 7 oil seals, ensuring a comprehensive understanding of their function, application, and maintenance.
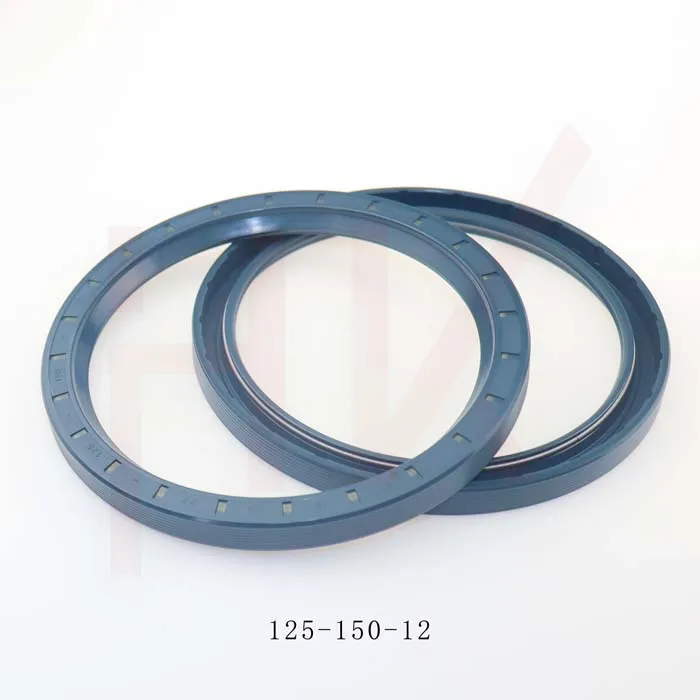
The dimensions of an oil seal, in this case, 25 40 7, indicate its inner diameter (25mm), outer diameter (40mm), and thickness (7mm). Selecting the correct seal for any machinery requires precise measurements, as even the slightest deviation can lead to equipment failure. These seals are essential in industries such as automotive, aerospace, and manufacturing, where the machinery's efficiency depends heavily on the reliability of its components.
Precision engineering is at the core of creating effective oil seals. These components are designed to operate under various temperatures and pressures, providing an uninterrupted barrier against contaminants like dust and dirt, while retaining lubricants inside the machinery. This is where expertise in materials science comes into play. Oil seals are typically constructed from materials like nitrile rubber, silicone, or fluorocarbon, each offering unique properties that make them suitable for specific applications.
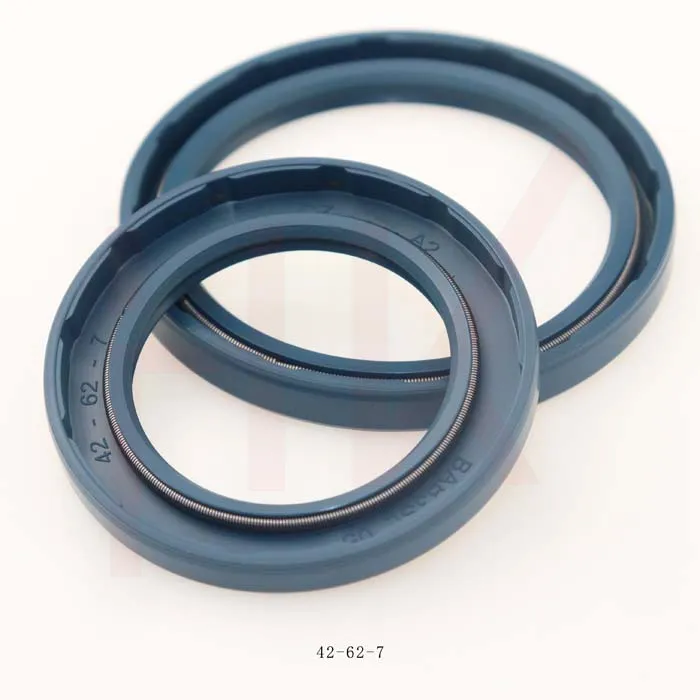
Nitrile rubber, for example, is known for its resistance to oil, fuel, and other chemicals, making it a popular choice for general-purpose oil seals. Silicone, on the other hand, offers exceptional thermal stability, which is ideal for applications involving extreme temperature fluctuations. Meanwhile, fluorocarbon seals provide superior resistance to heat and aggressive chemicals, often used in high-performance automotive or industrial scenarios. Choosing the right material is not just about matching specifications but understanding the environmental conditions the seal will face.
25 40 7 oil seal
Expertise in mechanical systems is incomplete without acknowledging the significance of proper seal installation and maintenance. Incorrect installation can lead to misalignment, which might cause undue stress on the seal and result in premature failure. Therefore, it's imperative to follow the manufacturer's guidelines during installation. Lubricating the seal and sleeve during installation helps in reducing friction and extending the seal life. Furthermore, regular checks and replacements are recommended to avoid sudden machinery breakdowns.
For maintaining the reliability and trust of your systems, it’s crucial to source oil seals from reputable manufacturers. Trusted brands generally adhere to strict quality control measures, ensuring their products meet industry standards and perform consistently. This reflects directly on the machinery’s performance, where substandard components could compromise the entire system's Readiness and efficiency.
Moreover, leveraging real-world experience can significantly enhance the understanding of oil seal applications. This includes collaborating with engineers and technicians who work on-site, addressing common challenges like dealing with high-pressure leaks or counteracting environmental wear and tear. These insights can be indispensable, informing better design and choice of materials for future oil seal development.
In conclusion, the critical role of 25 40 7 oil seals in attaining mechanical efficiency cannot be overstated. Through a combination of precise measurements, expert materials selection, and strategic maintenance practices, the performance and lifespan of these oil seals can be optimized. For all professionals in the field, continuous learning and adaptation to new technologies and materials are essential in maintaining an authoritative and trustworthy presence in the domain of mechanical engineering and machinery upkeep. Leveraging expertise and real-world experiences will ensure that your machinery operates with the utmost precision and reliability, meeting the demands of modern applications.