High pressure oil seals are critical components in many mechanical systems, ensuring that oil remains contained within machinery while preventing contaminants from entering. As an integral part of the engineering field, their importance cannot be overstated. Whether used in aerospace, automotive, or heavy machinery applications, understanding their design, materials, and functionality can significantly enhance performance and longevity.
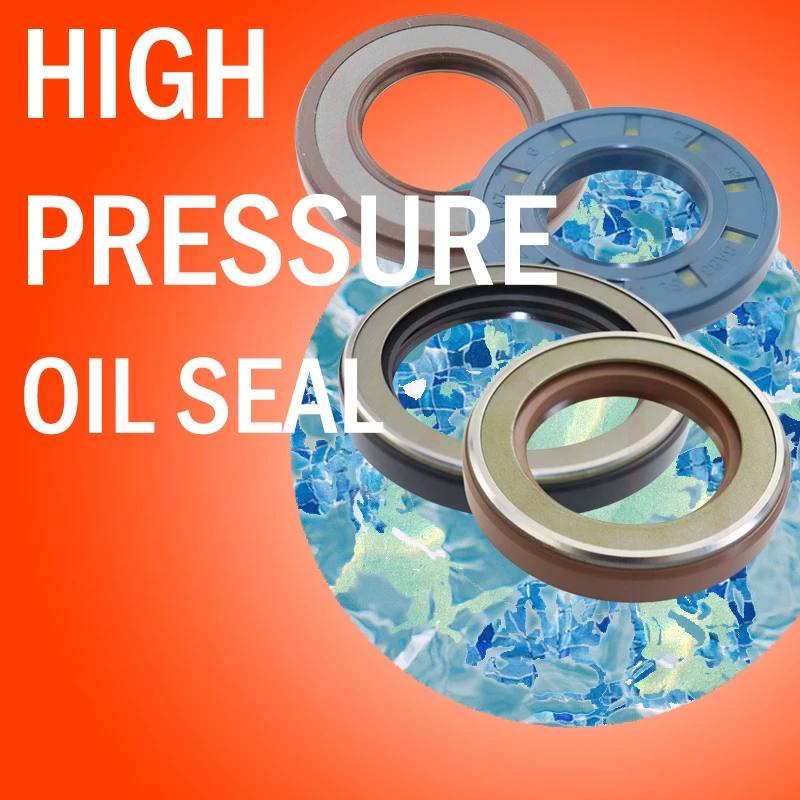
Selecting the appropriate high pressure oil seal begins with understanding the specifics of your application. Factors such as operational temperature, pressure, speed, and the type of fluid being sealed must be taken into account. For instance, oil seals used in automotive engines face very different conditions compared to those in industrial pumps. High pressure oil seals are specialized for environments where not only the pressure is substantial, but there is significant risk of damage from debris or extreme temperatures. By choosing the correct oil seal for your specific application, you can significantly reduce the risk of equipment malfunction and extend the life of your machinery.
A critical factor in the performance of high pressure oil seals is the material composition. Advanced materials such as fluorocarbon (Viton®), nitrile (NBR), and polytetrafluoroethylene (PTFE) are often employed due to their excellent resistance to oil, temperature, and wear. Fluorocarbon is particularly suited for high temperature applications, offering excellent thermal stability and chemical resistance, which makes it ideal for automotive and aerospace industries. Nitrile, on the other hand, is preferred for its cost-effectiveness and versatility in various applications. PTFE seals offer exceptional low friction and excellent chemical resistance, making them suitable for high-speed rotary applications under high pressure.
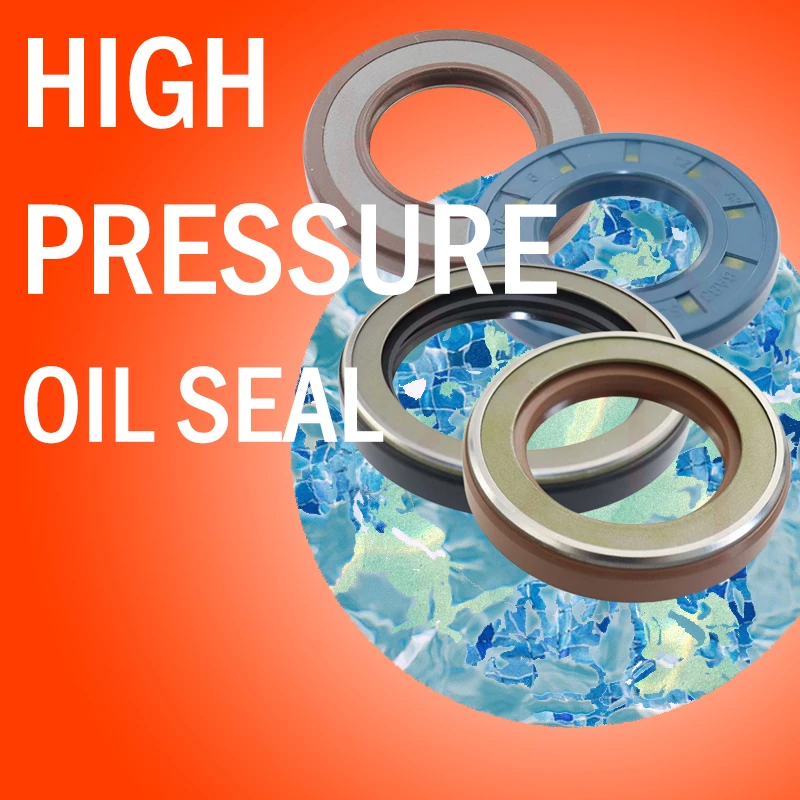
The design of the seal itself plays a crucial role in its effectiveness. A common design element in high pressure oil seals is the use of a lip, which can be either single or dual. Single lip seals are often employed in applications where the pressure is moderate and the primary concern is to keep the oil in while excluding contaminants. Dual lip designs, however, provide additional protection by offering an extra barrier against environmental factors. This is particularly vital in harsh environments where dirt and moisture could compromise the integrity of the seal.
Incorporating advanced features such as helical springs can further enhance the functional efficiency of high pressure oil seals. These springs provide consistent pressure against the shaft, maintaining a tight seal even as components expand and contract with temperature changes. Furthermore, some seals include a garter spring which encircles the lip, ensuring that the seal remains in constant contact with the rotating shaft for optimal functionality.
high pressure oil seal
Installation accuracy is another aspect that significantly affects the performance and lifespan of high pressure oil seals. Proper installation ensures the seal is correctly aligned and secured, preventing premature failure. During installation, it is critical to avoid any damage to the sealing lip or surface, as even minor abrasions can lead to leaks. Precision tools and proper handling techniques should be employed to preserve the integrity of the seal.
Ongoing maintenance and inspection are also necessary to ensure the durability of high pressure oil seals. Regular checks for signs of wear, leaks, or deformities can prevent catastrophic failures. Such inspections allow for early detection of issues that could lead to mechanical breakdowns, thus facilitating timely repairs or replacements.
Recent advancements in seal technology have led to the development of smarter oil seals, incorporating sensors that monitor temperature, pressure, and wear. These innovations provide real-time data and early warning signs of potential failures, enabling proactive maintenance strategies. As technology continues to advance, we can anticipate even more refined solutions designed to handle the increasing demands of modern machinery.
High pressure oil seals serve as indispensable components in ensuring the efficiency and reliability of numerous systems. Selecting the right material, design, and installation approach is paramount in achieving optimal performance. By prioritizing precision and quality in both product choice and maintenance practices, industries can enjoy enhanced machinery reliability and reduced downtime. As an expert in the field, understanding these elements allows one to make informed decisions, leading to greater system efficiency and operational success.