When it comes to high-performance machinery and heavy equipment, maintaining operational efficiency hinges significantly on the quality and reliability of each component. At the heart of ensuring this efficiency is the hydraulic dust seal, a critical component often underestimated yet irreplaceable in its function.
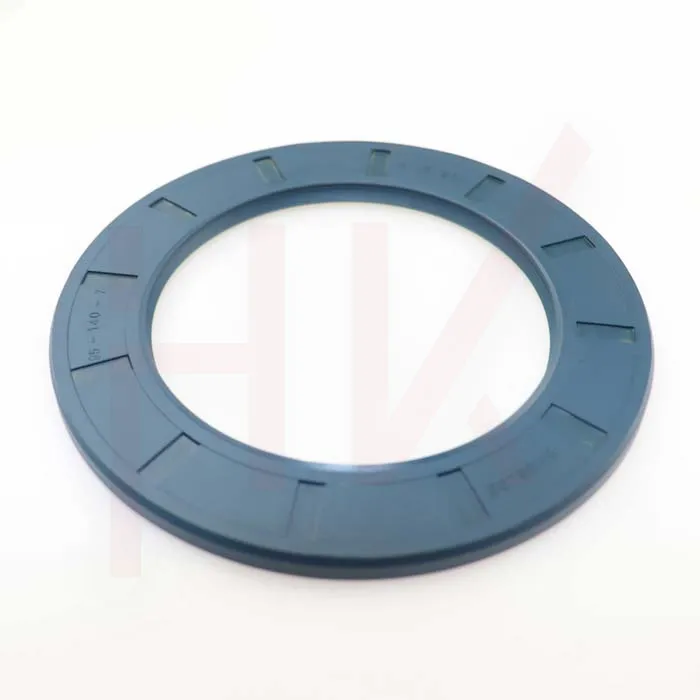
A hydraulic dust seal is designed primarily to prevent contaminants from infiltrating the hydraulic system, which can lead to premature damage and system failure.
Its role is pivotal—it is the unsung guardian of hydraulic integrity. Through first-hand experience, operators in the construction and industrial sectors have consistently found hydraulic dust seals to be invaluable in extending equipment life and reducing maintenance costs.
In terms of expertise, choosing the right hydraulic dust seal involves understanding material compatibility and seal design in relation to the specific environmental conditions your machinery faces. For instance, seals that operate in a dusty or abrasive environment, like mining or quarry sites, must be constructed from materials that resist wear and tear while maintaining a tight seal under pressure. Expert manufacturers generally recommend using polyurethane or compounds with similar resilience for such demanding applications.
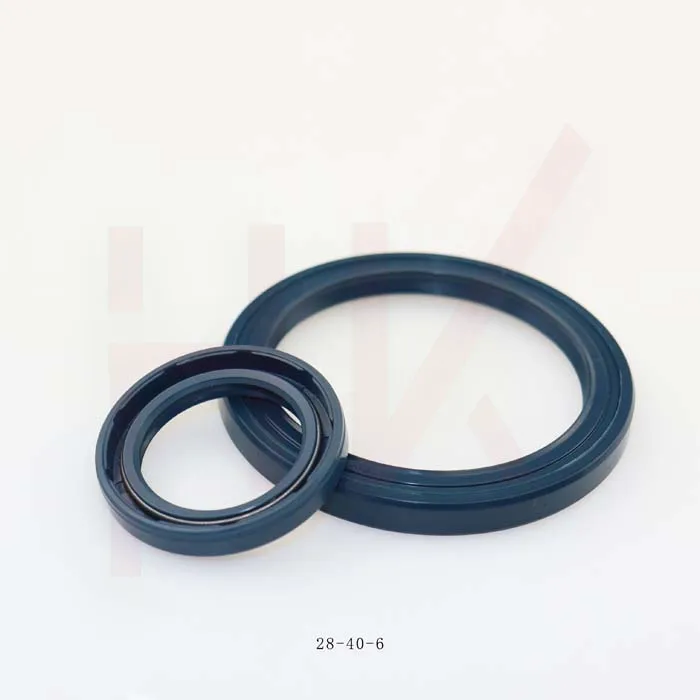
Our authoritative understanding stems from collaborations with leading hydraulic engineers who emphasize the necessity of exact fit and material quality. The precision in manufacturing hydraulic dust seals ensures minimal clearance and optimum performance, reducing the risk of hydraulic fluid leaks that can compromise both safety and functionality. Improving performance is often achieved through innovative design enhancements such as double-lip seal designs, which provide additional protective layers against contaminant ingress.
hydraulic dust seal
Credibility in the performance of hydraulic dust seals is also backed by rigorous testing and adherence to industry standards. Renowned suppliers subject their products to stringent protocols that simulate real-world conditions, certifying that each seal can withstand extreme temperatures, pressures, and exposure to hydraulic fluids without degrading. The trustworthiness of such seals is further validated by certifications from bodies such as the International Organization for Standardization (ISO), which assures users of their reliability and performance consistency.
To accentuate reliability, companies must ensure routine inspections and replacements of hydraulic dust seals as part of planned maintenance programs. Regular checks help identify wear and potential failures before they escalate, ensuring the continuous protection of hydraulic systems. In essence, proactive maintenance not only maximizes equipment uptime but also contributes to the long-term sustainability of operations.
In conclusion, the hydraulic dust seal, though small in size, plays a huge role in ensuring the seamless operation of machinery across various industries. Its effectiveness is enhanced by the expertise in selecting the appropriate seal type, underlining the importance of understanding the interchange between seal specifications and operational demands. With proven authority and trustworthiness, investing in high-quality hydraulic dust seals is a strategic decision that pays dividends in operational efficiency and system longevity.