The enigmatic world of oil seals, particularly the 17x30x7 oil seal, offers unparalleled utility and indispensable functionality in a myriad of industrial applications. Understanding this crucial component requires an examination of its design, material composition, and specific applications to fully appreciate its role in maintaining machinery efficiency.
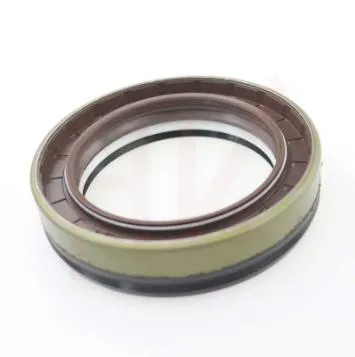
The 17x30x7 oil seal is meticulously crafted to create a perfect barrier, ensuring that lubricants remain within their designated areas while preventing detrimental contaminants such as dirt, moisture, and other particulates from permeating sensitive machinery components. The dimensions - 17mm inner diameter, 30mm outer diameter, and 7mm width - perfectly fit a range of shafts and housings, reinforcing their applicability in diverse mechanical systems.
From construction equipment to automotive engines and beyond, the role of oil seals, especially those with a dimension of 17x30x7, is nothing short of essential. In automotive applications, they are frequently employed in gearboxes and axles, where maintaining proper lubrication is crucial for the longevity and efficiency of moving components. Similarly, in industrial machinery, these seals ensure that hydraulic systems operate without leakage, maintaining optimal pressure and avoiding contamination that could lead to costly breakdowns.
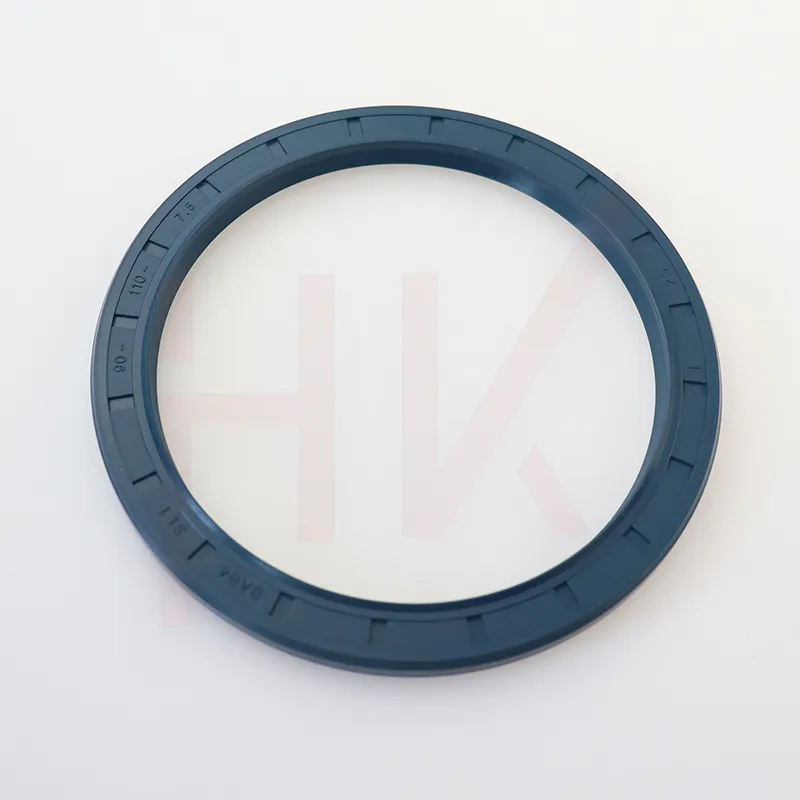
The expertise behind designing these seals is profound. Engineers meticulously select materials such as nitrile rubber, silicone, or fluoroelastomer based on the operational environment the seal will encounter. For instance, nitrile rubber exhibits excellent resistance to petroleum-based oils and hydrocarbons, making it a popular choice for automotive applications. Meanwhile, silicone or fluoroelastomer seals are favored for high-temperature or chemically harsh environments due to their superior resilience and longevity.
17x30x7 oil seal
Incorporating the right oil seal is not only about the physical dimensions but also about understanding the conditions it will face. This involves evaluating temperature ranges, fluid compatibility, and rotational speed, all of which influence material choice and seal design. Such thorough considerations underscore the authoritative knowledge engineers apply to ensure these components meet rigorous industrial standards.
Trustworthiness in oil seal performance is crucial, especially given that failure can result in catastrophic mechanical breakdowns, leading to significant downtime and repair costs. Hence, manufacturers conduct stringent testing, including dynamic and static tests, to ensure seals can withstand operational stresses. They simulate real-world conditions to evaluate performance, ensuring that each seal meets the proposed specifications and exceeds client expectations.
Experience reveals that investing in high-quality oil seals is economically prudent, as they extend machinery service life and reduce maintenance needs. Experienced operators report enhanced machinery performance and lower operational costs as direct benefits of utilizing high-quality 17x30x7 oil seals. These testimonials are backed by empirical data, highlighting decreased incidents of oil leakage and improved overall efficiency.
The narrative surrounding the 17x30x7 oil seal is a testament to its indispensable role in industrial machinery. Through combining thorough expertise, rigorous standards, and evidence-based performance, these oil seals exemplify the pinnacle of engineering achievement. Their integral function in protecting machinery, optimizing performance, and ensuring reliability speaks volumes of their importance, making them a non-negotiable component in any setting where mechanical precision and efficiency are prioritized.