Replacing seals on a hydraulic cylinder can be an intricate task, best navigated with precision and understanding of the system dynamics. With decades of expertise in hydraulic systems, I offer a comprehensive guide to enhance your skills and bolster your confidence in performing seal replacements.
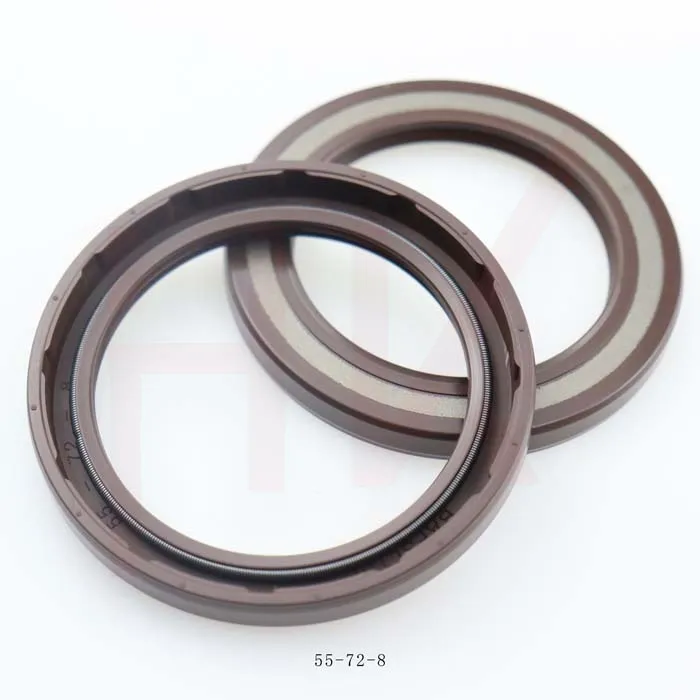
Hydraulic cylinders power the mechanical workhorses in industries ranging from construction to agriculture. The failure of a hydraulic cylinder seal can lead to system inefficiencies, fluid leaks, and eventual system downtime. Ensuring that seals are intact and fully operational is paramount for optimal system performance.
Signs indicating potential seal defects include visual fluid leaks, noticeable slowdowns in hydraulic action, or irregular load pressures. When these occur,
it’s often a clear sign that replacing seals on the hydraulic cylinder is necessary.
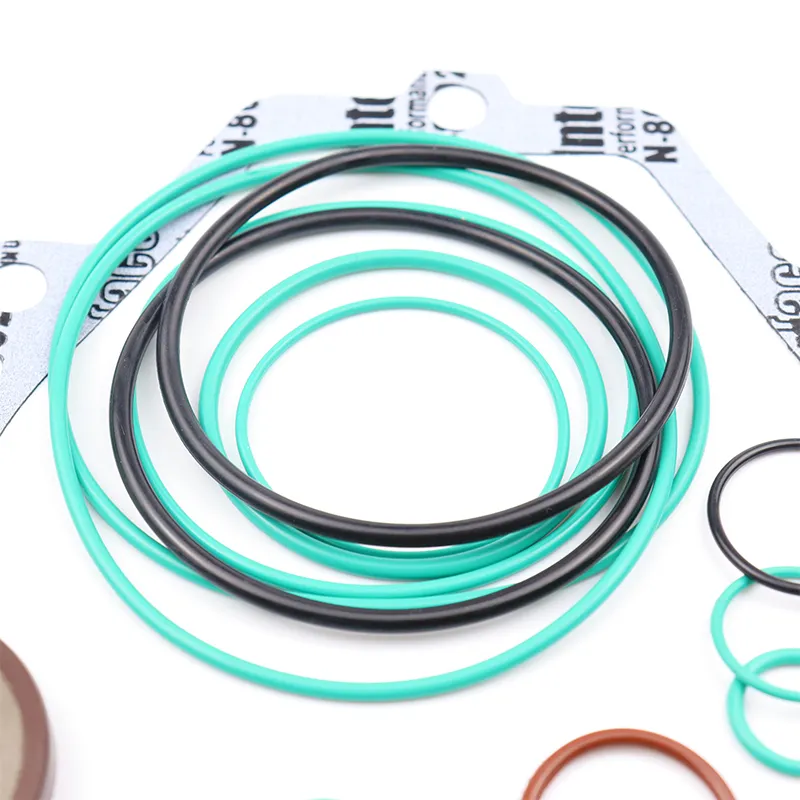
Preparation is critical. Begin with understanding the nuances of your specific hydraulic system and the type of cylinder in use—be it single-acting, double-acting, telescopic, or others. Gather tools such as seal kits appropriate for the cylinder's make, model-specific wrenches, circlips, and cleaning agents to ensure contamination-free operation.
Safety is paramount. Adequately depressurize the hydraulic system before initiation. Failure to do so can result in grave injuries or additional system complications. Uniformly dismantle the areas connected to the cylinder, taking care not to damage existing components intentionally or inadvertently.
Careful inspection should follow. Analyze the rods for any bends or damages; check the tube walls for scratches or scars that could contribute to premature seal failure. With these evaluations, you not only prepare the cylinder for seal replacement but may also identify other related issues warranting attention.
During seal removal, use suitable tools to extract old seals without nicking the seal groove. A clean removal process prevents the introduction of contaminants that could impair the new seals. Pay significant attention to the seal orientation and profiles to guarantee a seamless introduction of new rings.
replacing seals on a hydraulic cylinder
When installing the replacement seals, ensure they are compatible with the hydraulic fluid and pressure conditions typical of your application. Heed the manufacturer's specifications indicated in the product datasheet. Hydraulics professionals typically recommend pre-lubrication of seals with the system’s operating fluid to facilitate easier installation and reduce initial friction once the cylinder resumes operation.
Throughout the reassembly phase, maintain a meticulous approach. Properly torque all fittings to the specified values, preventing uneven pressures that could affect other components. Reassessing alignment is vital since even the slightest misalignment can considerably shorten the service life of seals and related parts.
Once reassembled, cautiously recommission the system. Gradually introduce pressure and monitor for leaks or sound discrepancies that could suggest improper installation. A robust verification phase not only ensures system efficacy but fortifies user trust in your repair methodology.
Preventative maintenance significantly extends the longevity of seals and associated components. Implement routine checks and establish criteria for seal inspection intervals. Enhanced seal material technology now offers advanced wear resistance and chemical compatibility, so consider these options for replacement to outstrip conventional models.
Challenges inevitably present during these operations; however, with each experience, expertise is bolstered, imparting an invaluable depth of understanding in hydraulic systems management. Engaging with hydraulic systems communities and continuous learning through industry seminars consolidates knowledge and broadens proficiency.
Through meticulous practice and improved familiarity with diverse system configurations, the evolving domain of hydraulic repair will be navigated with greater proficiency. Ultimately, systematic approaches underscore not just problem-solving acumen, but also a contributory role in sustaining mechanical systems within various industries worldwide.