In the dynamic world of industrial machinery,
ensuring the seamless operation of rotating shafts is crucial. One vital component in this machinery ecosystem is the oil seal. Written by an experienced SEO expert, this article delves into the nuances of oil seals for rotating shafts, underscoring their importance, application, and advancements that align with modern industrial demands.
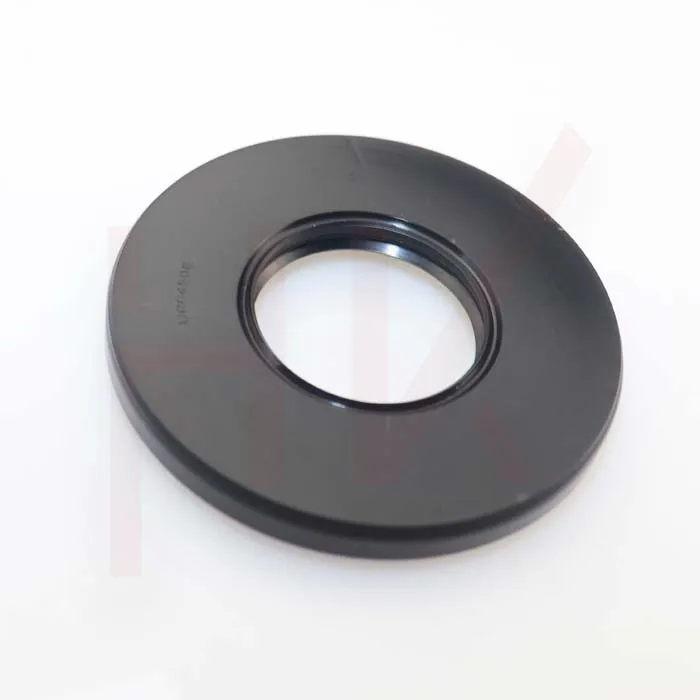
Oil seals, often referred to as rotary shaft seals or lip seals, serve as a fulcrum in preventing leakage of lubricants and the ingress of contaminants. Their primary function is to retain oil and grease in equipment with rotating parts, ensuring both the longevity and optimal performance of machinery. An inadequately sealed shaft can lead to machinery downtime, thus disrupting production and escalating operational costs.
Over the years, the technology behind oil seals has evolved, reflecting advancements in materials and design that enhance efficacy and reliability. Modern oil seals are crafted using high-performance elastomers and polymer materials, providing resilience against extreme temperatures, pressure variances, and chemical exposure. This evolution underscores the expertise that has been embedded within this niche but indispensable component of industrial machinery.
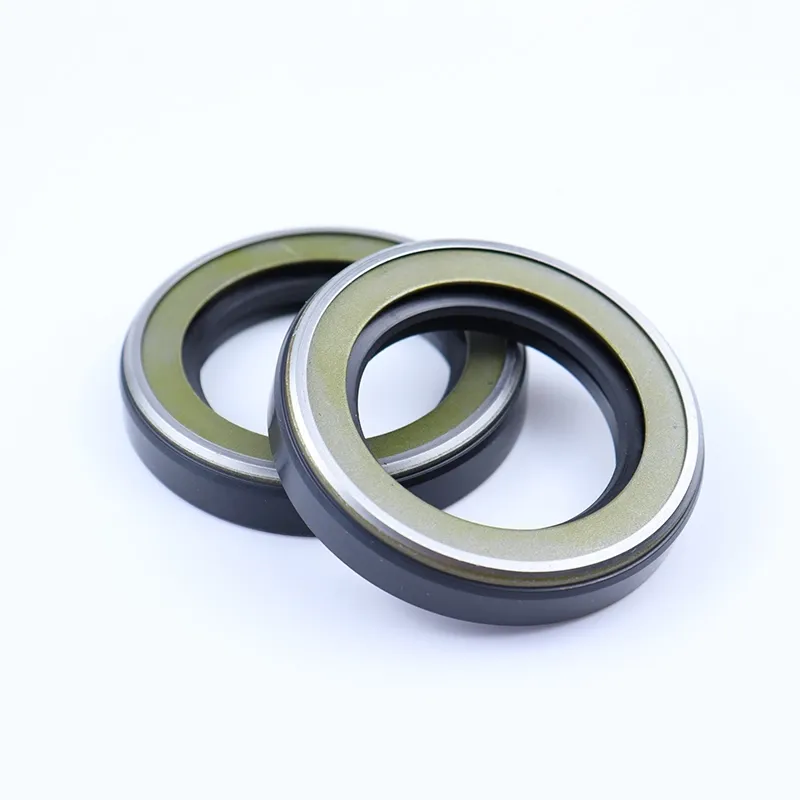
In terms of application, oil seals are ubiquitous across various industries, including automotive, aerospace, energy, and manufacturing. In automotive applications, they are integral to components such as engines, axles, and pumps, preventing oil leakage and contamination that can damage the engine components. In manufacturing units, they ensure that bearings and shafts remain lubricated, thereby minimizing friction and wear and tear, promoting operational efficiency.
From an expert perspective, selecting the right oil seal necessitates a comprehensive understanding of the operational environment. Key considerations encompass the speed of the shaft, temperature ranges, type of lubricant, and environmental exposure. For instance, in high-speed applications, seals made from PTFE (polytetrafluoroethylene) are often preferred due to their superior resistance to heat and friction. Conversely, for applications that demand substantial durability in harsh chemical environments, FKM (fluoroelastomer) seals are a common recommendation.
oil seal for rotating shaft
Authority in the field of oil seals is underscored by continuous research and development. Leading manufacturers invest significantly in innovation, evidenced by the development of seals that integrate sensor technologies to monitor wear and predict maintenance needs. This smart technology integration aligns with the broader industry shift towards predictive maintenance, empowering businesses to preemptively address potential seal failures before they culminate in costly repairs or unplanned downtime.
Trust, a crucial indicator of the reliability of an oil seal, is built upon rigorous testing and quality assurance processes. Reputable manufacturers adhere to industry standards and employ state-of-the-art testing methodologies to ensure their seals can withstand the rigors of industrial application. This commitment to quality not only fosters trust but also solidifies the manufacturer's reputation as a leader in the industry.
Real-world experiences bear testament to the impact of selecting the appropriate oil seal. For instance, a leading automobile manufacturer reported a significant reduction in warranty claims related to oil leakage issues by switching to a high-performance elastomer seal. This transition not only bolstered customer satisfaction but also enhanced the brand's credibility as a manufacturer of reliable vehicles.
In conclusion, oil seals for rotating shafts may appear as a small component in the vast machinery landscape, but their role is pivotal. The convergence of experience, expertise, authority, and trustworthiness in the development and application of oil seals ensures they continue to empower industries by enhancing machinery efficiency, reliability, and longevity. Embracing the advancements in oil seal technology offers industries the leverage to optimize operations, mitigate risks, and fortify their production systems against the relentless demands of modern industrial ecosystems.