In the realm of hydraulic machinery, the role of hydraulic cylinder seals is often understated, yet they are the unsung heroes ensuring efficient and reliable operation. An in-depth understanding of these seals not only facilitates optimal equipment performance but also underscores their significance in maintaining the longevity of hydraulic systems.
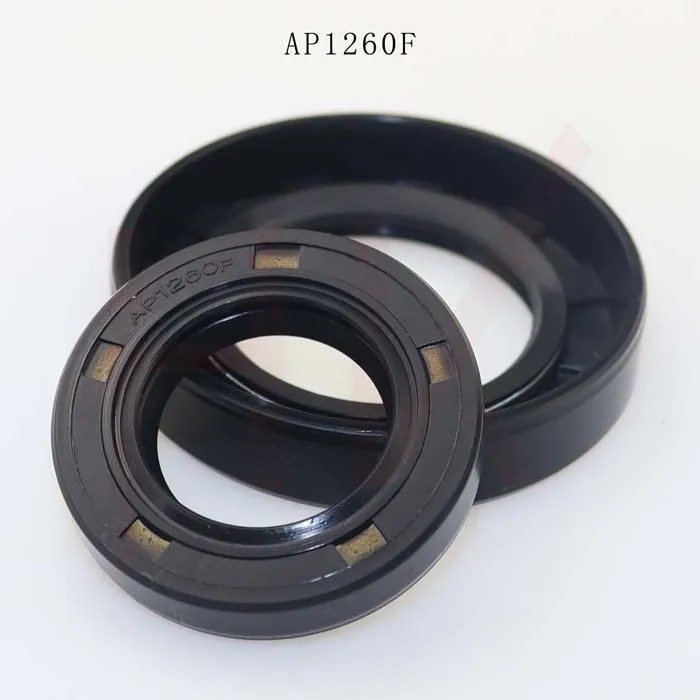
Hydraulic cylinder seals are designed to prevent fluid leakage between the different components within a hydraulic cylinder. Their performance is fundamental to maintaining the pressure required for the cylinder to function properly. Without high-quality seals, hydraulic systems can suffer from inefficiencies, leading to potential system failures, increased maintenance costs, and even operational hazards.
One crucial aspect of hydraulic cylinder seals is their material composition. The choice of material plays a pivotal role in determining the seal's effectiveness and durability. Common materials include nitrile rubber, which is well-suited for general purposes due to its resistance to oil and operating temperature range; polyurethane, known for its high wear resistance and ability to handle higher pressures; and PTFE (Teflon), which is preferred for its low friction and chemical resistance properties. Selecting the right seal material is essential to match the specific application needs and operating conditions.
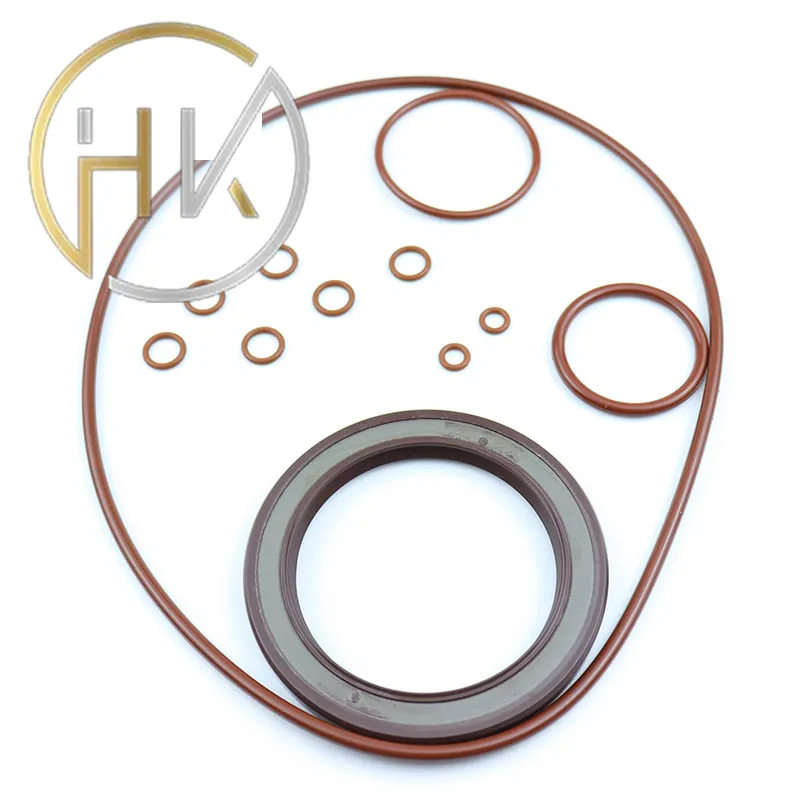
Expertise in the correct installation and handling of hydraulic seals cannot be overstated. A seemingly simple error during installation can lead to premature seal failure, causing downtime and increased operational costs. Employing knowledgeable technicians for the task ensures that seals are handled appropriately, maintaining their integrity. Proper lubrication during installation can also prevent damage and help extend the seal's service life.
hydraulic cylinder seals
The importance of regularly scheduled maintenance checks cannot be ignored. Regular inspection of hydraulic seals allows for the identification of potential wear and tear before they become significant problems. This proactive approach aids in preventing leaks and maintaining the system's operational efficiency. Incorporating a routine seal inspection schedule as part of an overall maintenance program is a sound strategy for any industry relying on hydraulic systems.
From an authoritative standpoint, manufacturers and suppliers of hydraulic seals should be chosen based on their reputation and commitment to quality. Reputable manufacturers often adhere to stringent quality standards, ensuring the reliability of their products. Their expertise and experience in the industry provide a valuable resource when selecting the appropriate seals for specific applications.
Trustworthiness in hydraulic seal performance translates to a dependable hydraulic system. Users rely on seals to keep their machinery running smoothly, and any failure can lead to costly downtime and repairs. Building trust with customers involves not just providing quality products but also offering guidance and support. Customer service that advises on the selection, application, and potential troubleshooting of hydraulic seals strengthens that trust.
Ultimately, the proper selection, installation, and maintenance of hydraulic cylinder seals are fundamental to ensuring that hydraulic systems perform at their peak. Those involved in the operation and design of hydraulic machinery should prioritize the quality and suitability of these seals, as their impact on system efficiency, cost-effectiveness, and safety is profound. By understanding the critical role of hydraulic cylinder seals, businesses can enhance their operational reliability and extend the lifespan of their machinery, realizing significant benefits in both productivity and profitability.