High-pressure seals are critical components across various industries, ensuring the reliable containment of liquids and gases in high-pressure environments. These industrial seals are expertly designed to withstand extreme pressures and challenging conditions, making them essential in sectors like oil and gas, chemical processing, automotive, aerospace, and manufacturing.
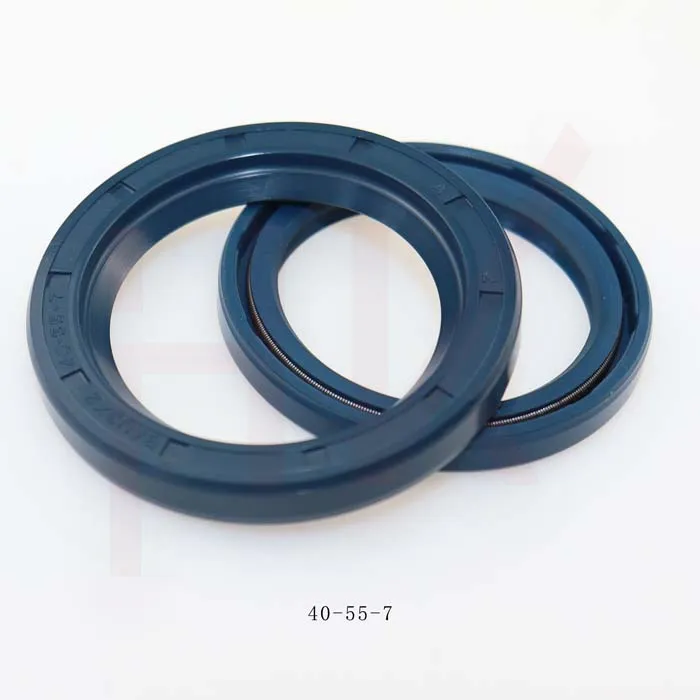
Experience with high-pressure seals often underscores their crucial role in maintaining system integrity. Engineers who have worked with these components understand that without robust sealing solutions, systems could suffer leaks, leading to costly downtime, environmental hazards, and safety risks. High-pressure seals are engineered to provide optimal performance, even under the most demanding conditions, by utilizing high-grade materials such as PTFE, elastomers, and advanced composites, each chosen for its unique properties such as temperature resistance and chemical compatibility.
Expertise in the field of high-pressure seals encompasses a profound understanding of their design and application. These seals are not one-size-fits-all; they must be meticulously selected and tailored to meet specific operational requirements. This involves analyzing parameters including pressure, temperature, type of fluid, and the mechanical conditions of the system. Engineers leverage sophisticated design software to model performance scenarios, ensuring that each seal delivers unparalleled reliability and durability. The engineering process is marked by iterative testing and optimization, always seeking to push the boundaries of seal performance.
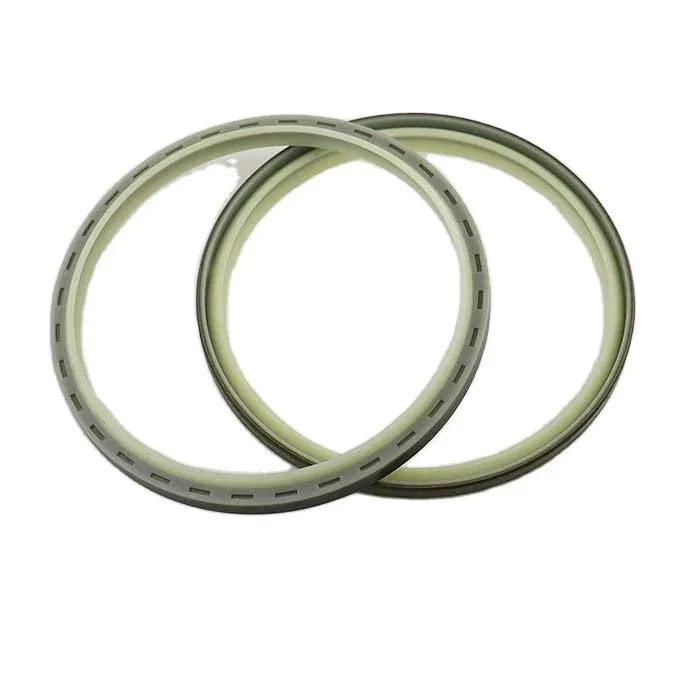
Authoritativeness in the manufacture and selection of high-pressure seals comes from a commitment to quality and innovation. Leading manufacturers invest heavily in research and development to pioneer new materials and technologies that enhance seal performance. They maintain stringent quality control processes certified by international standards such as ISO 9001, ensuring each seal meets rigorous specifications. These industry leaders contribute to technical papers and participate in global conferences, sharing insights and advancements that shape the future of sealing technology.
high pressure seal
Trustworthiness is the hallmark of high-pressure seal suppliers committed to customer satisfaction through exceptional services and reliable products. Trust is built on a proven track record of seals that perform reliably under specified conditions, backed by detailed technical support and warranties. When choosing a seal supplier, companies often look for partners who not only provide superior products but also offer comprehensive after-sales support, including troubleshooting and guidance. A trustworthy supplier stands by its products and is responsive in addressing client needs, ensuring long-term relationships and customer peace of mind.
In the landscape of high-pressure seals, continuous innovation is key. As industries evolve, so do the demands placed on sealing technologies. New developments such as self-lubricating seals, seals with enhanced load-bearing capabilities, and environmentally friendly materials are transforming the way industries operate, offering cost reductions, improved efficiency, and a smaller ecological footprint. Staying at the forefront of these advancements requires vigilance and commitment to learning and adaptation.
Moreover, digital tools are revolutionizing how seals are designed and monitored. Smart seals equipped with sensors provide real-time data on seal performance, enabling predictive maintenance and reducing unexpected failures. This marriage of traditional engineering and modern technology empowers businesses to achieve greater operational efficiency and reliability.
Ultimately, high-pressure seals are indispensable to the smooth operation of many industries. By combining experience, expertise, authoritativeness, and trustworthiness, the industry continuously elevates the standards of performance and safety. For any professional involved in systems that operate under high-pressure conditions, understanding and choosing the right seal is crucial for operational excellence and innovation.