Hydraulic ram oil seals play a critical role in the smooth and efficient operation of hydraulic systems, particularly those found in heavy machinery and industrial applications. The importance of these components cannot be overstated, as they ensure the proper containment of hydraulic fluids, thus maintaining system pressure and preventing leaks. Understanding the intricacies of hydraulic ram oil seals is essential for anyone involved in maintaining or operating hydraulic machinery.
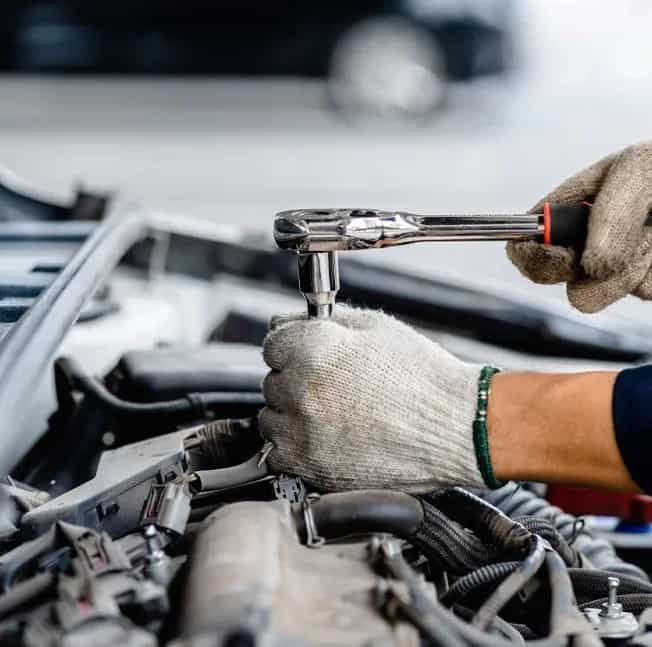
At their core, hydraulic ram oil seals are designed to prevent fluid leakage by creating a barrier between the moving parts within the hydraulic cylinder. This is critical not only for maintaining the operational pressure within the system but also for minimizing the risk of contamination. Contaminants can significantly reduce the efficiency of hydraulic systems and lead to premature wear and tear. Selecting the appropriate seal for a specific application involves considering factors such as the type of hydraulic fluid used, operating temperature ranges, pressure conditions, and the speed of moving parts.
From a technical perspective, hydraulic ram oil seals are crafted from durable materials that provide the necessary resistance to extreme conditions. Common materials include nitrile rubber, fluorocarbon, and polyurethane, each offering distinct advantages. For instance, nitrile rubber is often chosen for its cost-effectiveness and good compatibility with petroleum-based oils, whereas fluorocarbon seals are ideal for high-temperature applications due to their excellent heat resistance.
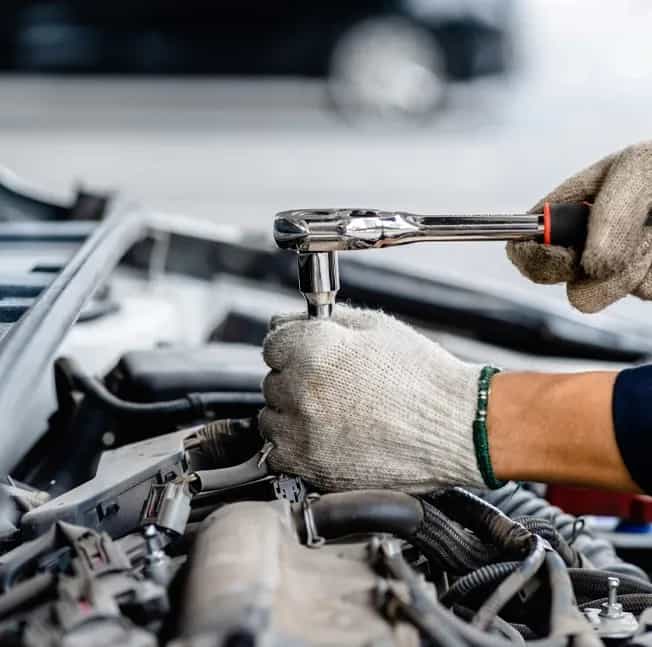
hydraulic ram oil seals
When it comes to installation, ensuring the correct fit and alignment of hydraulic ram oil seals is paramount.
Misalignment can lead to seal failure, resulting in costly downtime and repairs. It's crucial that those responsible for the maintenance of hydraulic systems are equipped with the expertise to recognize the signs of seal wear and understand the procedures for replacing seals efficiently. This includes inspecting the surface finish of the cylinder rod, which should be smooth and free from defects to prevent seal damage.
Regular maintenance checks can enhance the longevity and performance of hydraulic ram oil seals. This involves monitoring for signs of leakage, checking system pressure levels, and replacing seals at the first indication of deterioration. Moreover, utilizing high-quality seals from reputable manufacturers can considerably boost the reliability of hydraulic systems. These manufacturers invest in research and development to improve seal designs, delivering products that offer better seal integrity and reduced friction, which in turn extends the service life of the hydraulic system.
In conclusion, hydraulic ram oil seals are vital components that warrant careful selection, installation, and maintenance. Those who oversee the operation of hydraulic systems should be well-versed in the attributes and limitations of various seal materials, as well as the operational requirements of their specific machinery. By prioritizing regular inspections and using high-quality products, businesses can avoid unnecessary operational disruptions and enhance the overall efficiency and reliability of their hydraulic systems. The performance of these seals has a far-reaching impact on the productivity and sustainability of operations relying on hydraulic power.