Metric shaft seals are often overlooked components of machinery, yet they play a vital role in maintaining the efficiency and longevity of a wide range of industrial applications. Understanding their functionality, types, and the importance of choosing the right seal can significantly enhance machinery performance, reduce maintenance costs, and prevent unexpected downtimes.
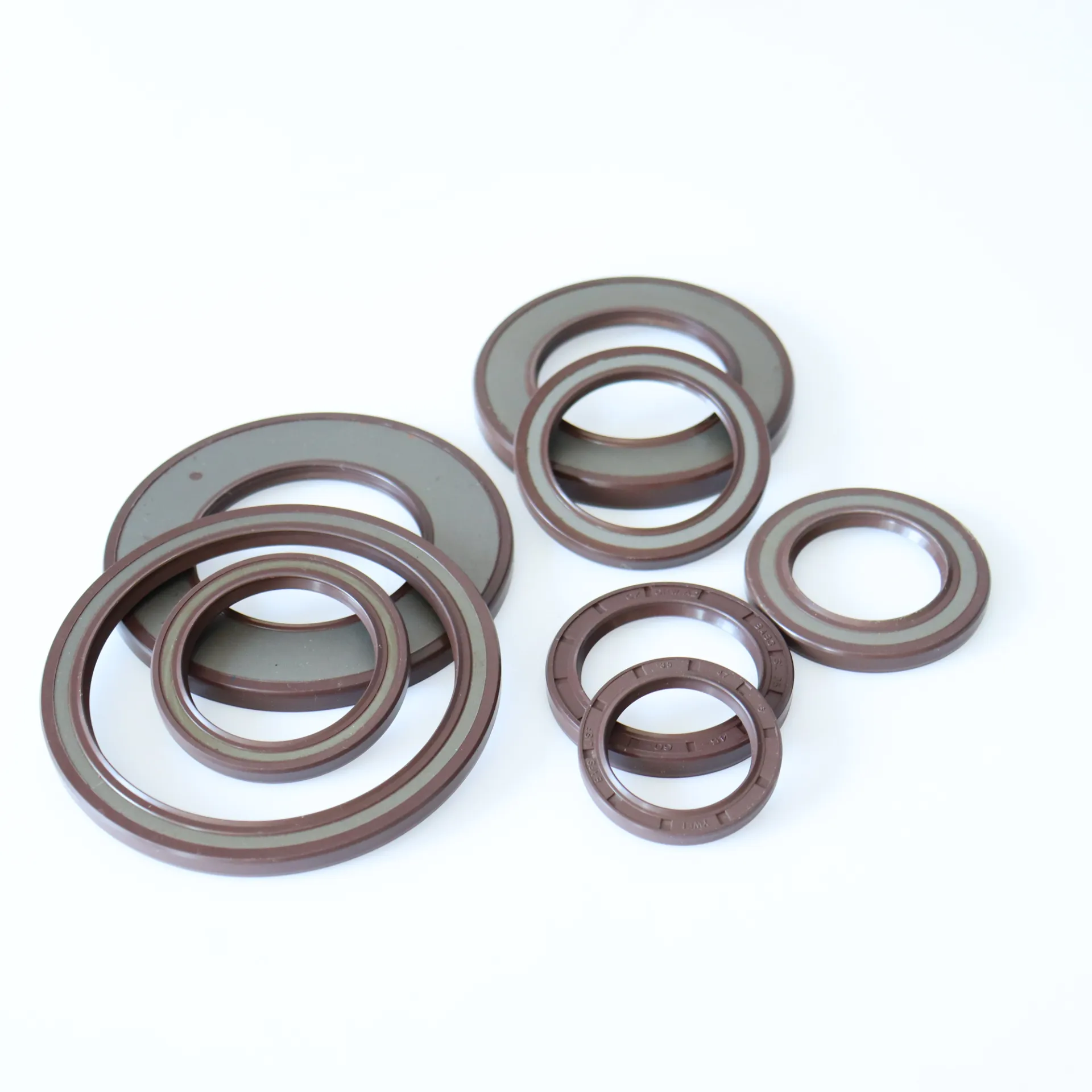
Metric shaft seals are primarily engineered to protect rotating shafts by preventing fluid leaks and keeping contaminants out. Their effectiveness is essential in maintaining the delicate balance within systems such as pumps, gearboxes, and engines. These seals serve as a barrier between the internal and external environments of machinery, ensuring that the lubricants stay within while dirt and debris stay out.
Based on personal experience in the field, metric shaft seals have proven indispensable in environments that demand high precision and reliability. Industries such as automotive, aerospace, and manufacturing heavily rely on these components. One might compare their function to that of a diligent sentry guarding a fortress against the infiltration of detrimental elements, an analogy that highlights their protective role in critical applications.
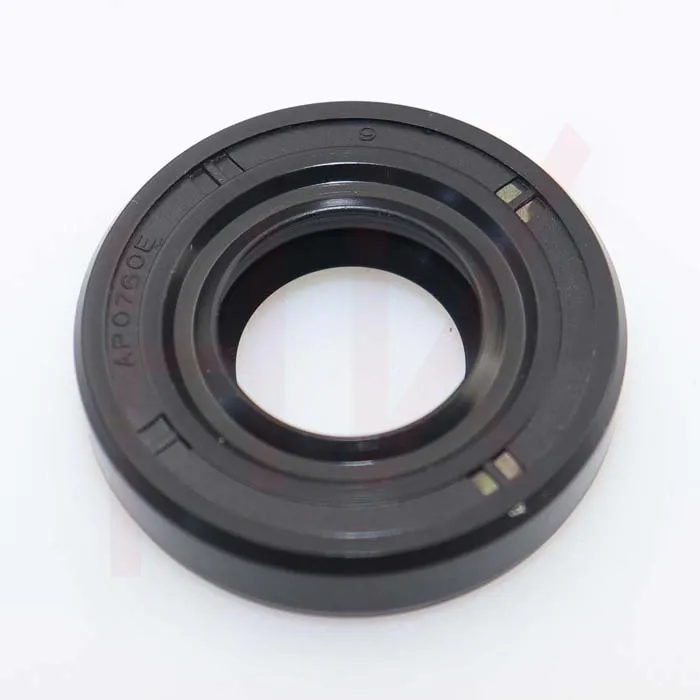
The expertise involved in manufacturing metric shaft seals is substantial. Precision is key, and any deviation during production can lead to suboptimal performance. Material selection is crucial; seals are commonly made from durable compounds such as nitrile rubber, fluorocarbon, or silicone, each suited to specific operational environments. For example, fluorocarbon seals offer excellent resistance to high temperatures and chemical exposure, making them ideal for demanding industrial settings.
metric shaft seals
Authoritative knowledge on the subject suggests that the correct installation of metric shaft seals is as crucial as their design. Incorrect installation can lead to premature seal failure, which might go unnoticed until it results in significant operational disruptions. Therefore, it's paramount to follow manufacturer guidelines meticulously and employ skilled technicians for the task. Moreover, selecting seals from reputable manufacturers is vital to ensure top-tier quality and performance.
Trustworthiness in metric shaft seals is built upon consistent performance over time. Regular inspections and maintenance are recommended to extend their lifespan and prevent unexpected failures. Employing a proactive maintenance schedule, one can identify potential issues before they escalate, saving both time and resources. Routine maintenance tasks should include checking for wear, verifying alignment, and ensuring proper lubrication.
From a product perspective, advancements in technology have contributed to the evolution of metric shaft seals. Today's seals are not only more robust but also designed to cater to specific applications. Innovations such as dynamic seals have revolutionized the way industrial machinery operates, offering enhanced sealing solutions for dynamic movements encountered in modern engineering designs.
In summary, metric shaft seals are critical to the success of numerous industrial operations. Their role in safeguarding machinery, ensuring optimal performance, and extending operational life cannot be overstated. By understanding their importance and investing in high-quality, appropriately selected seals, industries can achieve greater efficiency and reliability. Such strategic choices reflect not only on an organization's commitment to excellence but also on its understanding of the nuances that drive operational success.