The shaft oil seal plays a critical role in a wide range of mechanical systems, serving as a vital component that prevents the leakage of fluids along rotating shafts. Tailored to fit the dimensions and requirements of various industrial applications, the shaft oil seal is indispensable in maintaining the integrity and operational efficiency of machinery. Drawing from years of experience and expertise in engineering and product design, this article delves into the essential attributes of shaft oil seals and their relevance across different industries.
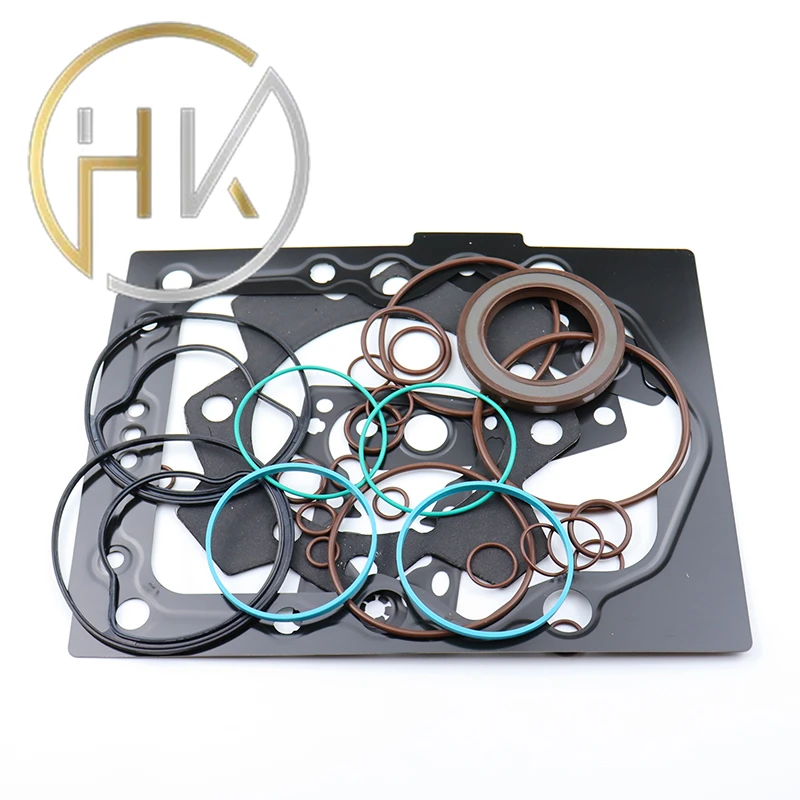
Shaft oil seals primarily prevent the ingress of contaminants such as dust, dirt, and moisture while retaining lubricants within the machinery. This dual functionality is pivotal in prolonging the lifespan of bearings and internal components. Utilizing a shaft oil seal with the wrong specifications can lead to increased wear and tear, compromising the equipment's performance and potentially leading to costly repairs.
The engineering behind shaft oil seals involves advanced materials that provide resistance to thermal stresses, chemicals, and abrasive particles. Nitrile rubber, fluoroelastomers, and silicone are among the commonly used materials. Nitrile rubber, known for its excellent oil resistance and affordability, is extensively used in automotive and light industrial applications. Fluoroelastomers, with superior heat and chemical resistance, are favored in applications involving elevated temperatures and aggressive fluids, such as aerospace and chemical processing industries.
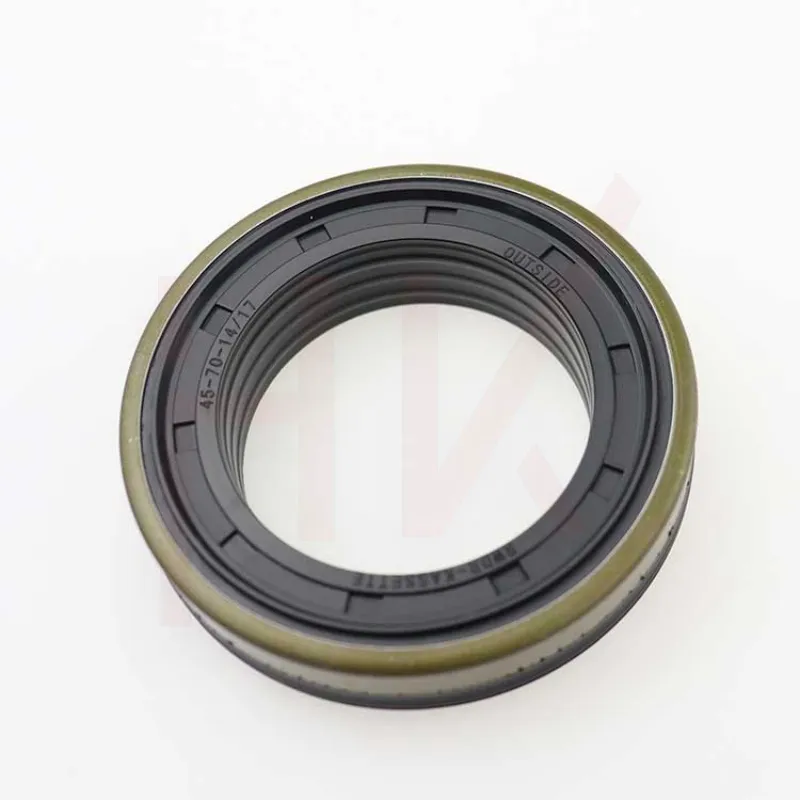
Precision in the design of shaft oil seals is paramount. It requires an understanding of the shaft diameter, rotational speed, temperature ranges, and the type of lubricant utilized within the system. Incorrect sizing or material selection can result in leakage, or worse, total seal failure, which might lead to operational downtimes. Therefore, working closely with engineers and suppliers to ensure the correct specifications is crucial.
shaft oil seal
Expert knowledge in maintenance practices is another critical area. Regular inspection of shaft oil seals for signs of wear, such as hardening, cracking, or loss of elasticity, is necessary. Replacing shaft oil seals at the earliest sign of wear can prevent unscheduled downtime and protect the machinery from significant damage.
Authoritativeness in the selection process of shaft oil seals cannot be overemphasized. Relying on trusted manufacturers and suppliers, who adhere to industry standards and certifications, ensures high-quality products. Manufacturers with rigorous testing protocols and certifications like ISO 90012015 offer added assurance of reliability and performance.
Trustworthiness is enhanced by manufacturers who also provide detailed installation guides and troubleshooting support. Proper installation techniques involve ensuring the sealing lip is accurately positioned and not damaged during the assembly process. Misalignment or improper installation can lead to premature failure,
undermining the seal’s effectiveness.
In conclusion, the importance of choosing the right shaft oil seal reflects in the seamless operation of diverse mechanical systems. Emphasizing precision in material selection, adherence to industry standards, and regular maintenance are the cornerstones of an effective sealing strategy. Leveraging expertise and maintaining a collaborative approach with reliable suppliers further fortifies the operational integrity of your machinery. Understanding these factors solidifies the reliability and trustworthiness of shaft oil seals in enhancing the longevity and performance of industrial equipment.