Rotary shaft seals are engineering marvels that play a crucial role in a multitude of applications, from automotive engines to industrial machinery. These components are indispensable in preventing leakage of fluids along rotating shafts. Their design, material, and application-specific considerations ensure operational efficiency and longevity in machinery, and understanding these nuances is essential for any professional working in engineering or manufacturing.
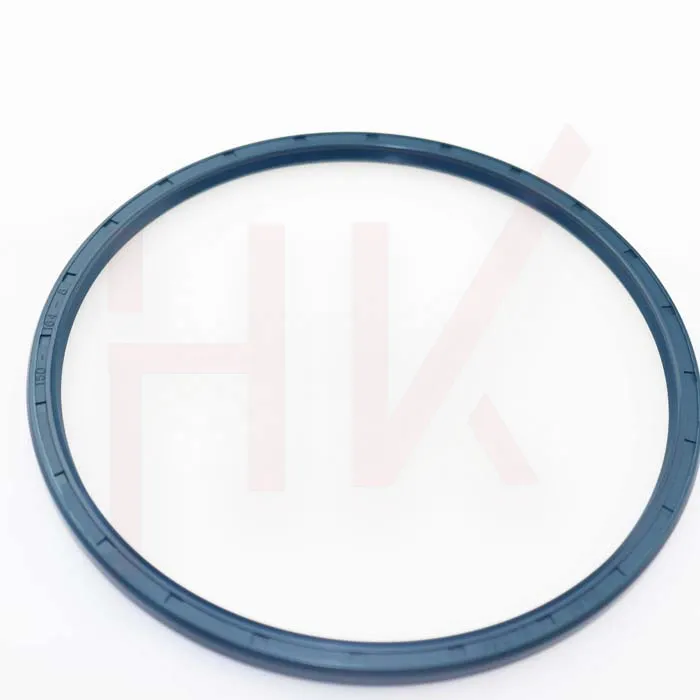
The experience and knowledge of engineers reveal that rotary shaft seals, often dubbed oil seals or radial lip seals, have been meticulously optimized over the years to cater to the demanding environments they operate in. The key elements of a rotary shaft seal include the sealing lip, the metal case, and the garter spring. The sealing lip, typically made from elastomers like nitrile rubber or more advanced polymers like fluoroelastomers, creates the barrier that prevents fluid leakage. The garter spring ensures that the seal maintains the necessary radial force to accommodate shaft misalignments and deflections during operation.
From an expert's perspective, the material selection for the sealing lip can make or break the efficiency of a rotary shaft seal. For example, nitrile is often selected for general-purpose seals due to its balance of cost-effectiveness and performance in moderate temperature and pressure conditions. On the other hand, environments involving extreme temperatures or aggressive chemicals might necessitate the use of silicone or PTFE-based seals, which provide superior resistance to degradation.
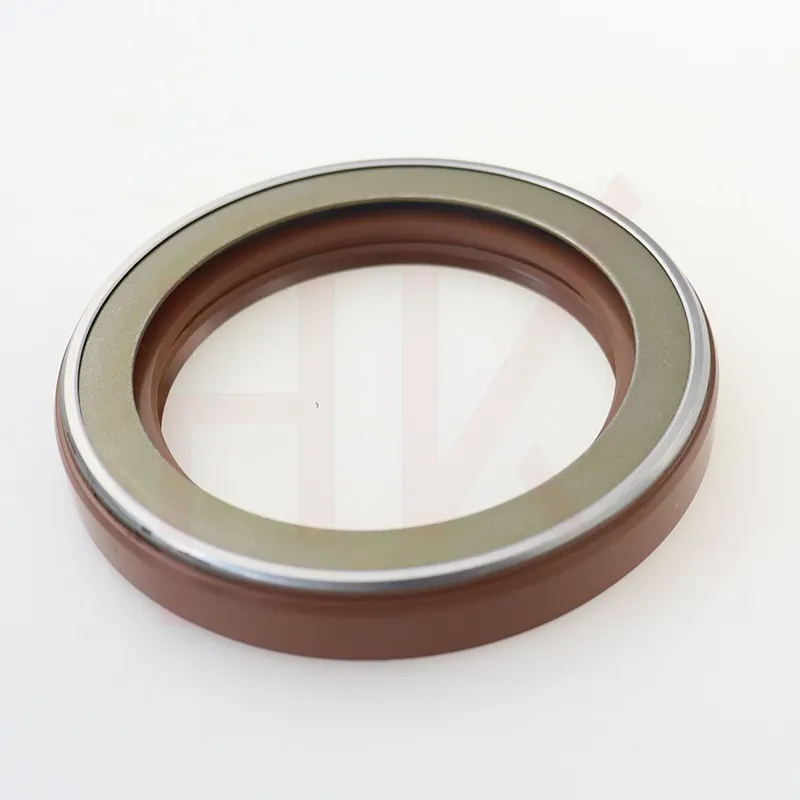
In automotive industries, the experience of both end-users and manufacturers dictates that seal integrity is paramount not only for preventing leaks but also for minimizing contamination. Rotary shaft seals in vehicles prevent oil from leaking out of the engine and transmission assemblies, ensuring the longevity and performance of the vehicle. In such applications, even the minutest detail, such as the quality of the metal case, which provides structural integrity to the seal assembly, is critical to withstand operational vibrations and pressure fluctuations.
rotary shaft seal
Meanwhile, industrial applications demand a higher level of expertise and understanding, as the operational conditions can vary widely. Rotary shaft seals used in hydraulic pumps, for example, must resist high-pressure differentials and maintain their effectiveness over prolonged periods. Here, computational modelling and empirical testing play authoritative roles in fine-tuning designs to accommodate these pressures and motions, which are unique to different industrial processes.
Trustworthiness is another pivotal aspect concerning the manufacturing and application of rotary shaft seals. Industry standards, such as those from the International Organization for Standardization (ISO), provide guidelines on the dimensions, tolerances, and materials suitable for various applications.
Compliance with these standards ensures that the seals perform reliably under specified conditions. Manufacturers often subject their products to rigorous testing, including thermal cycling, pressure pulsation, and chemical exposure tests, to certify their durability and performance over a predetermined lifecycle.
In conclusion, rotary shaft seals are integral components that demand a comprehensive understanding of material science, mechanical engineering, and application-specific challenges. The seamless coordination of these facets results in reliable seal performance, ultimately enhancing machinery efficiency and longevity. As the demands of modern machinery continue to escalate, the expertise and innovations within this domain will undoubtedly evolve, securing the rotary shaft seal's place in the pantheon of essential engineering components.