Dust seals are an often-overlooked but crucial component in various industrial and mechanical systems. Their primary function is to prevent contaminants such as dust, dirt, and moisture from entering and damaging critical components within machinery or equipment. Their utility extends across a diverse range of industries, including automotive, manufacturing, construction, and more. Understanding dust seals' significance and appropriate usage can vastly improve equipment longevity and performance.
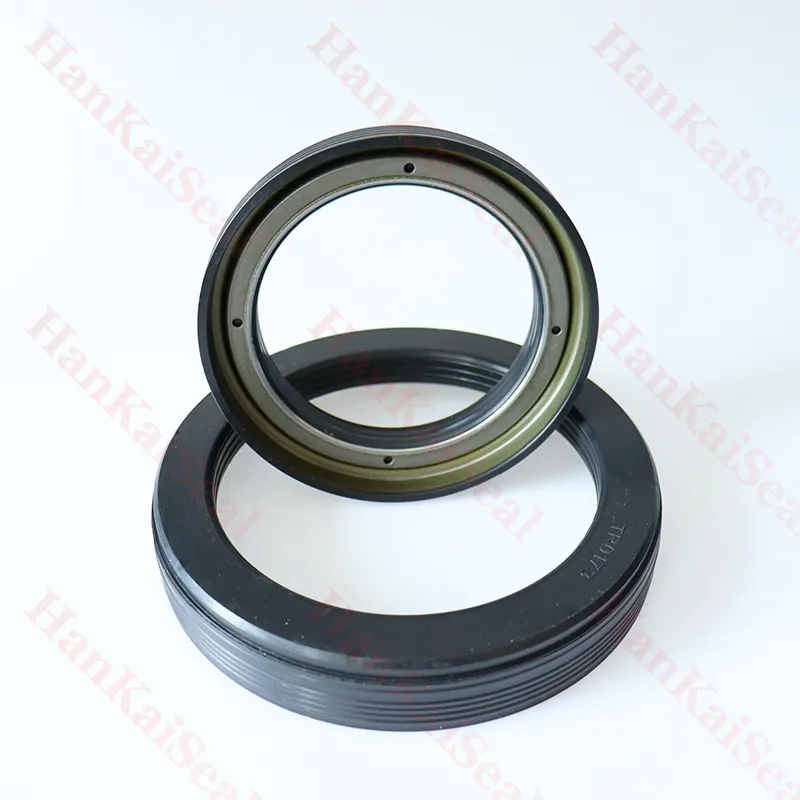
The construction of a dust seal usually involves materials that are robust yet flexible enough to create an impermeable barrier. Common materials include rubber, polyurethane, and other plastics tailored to withstand environmental stressors. The correct material selection is vital for ensuring durability against abrasive particles and resistance to temperature fluctuations. Engineers and maintenance professionals must consider the specific application's demands to select the appropriate dust seal material.
In the automotive industry, dust seals are instrumental in preserving the integrity of shock absorbers and struts. By shielding these components from dirt and grime, dust seals prevent premature wear and corrosion, leading to a smoother vehicle operation and a longer lifespan for shock-absorbing systems. Experienced automotive technicians stress the importance of regular inspections and replacements of dust seals during routine maintenance to enhance vehicle safety and efficiency.
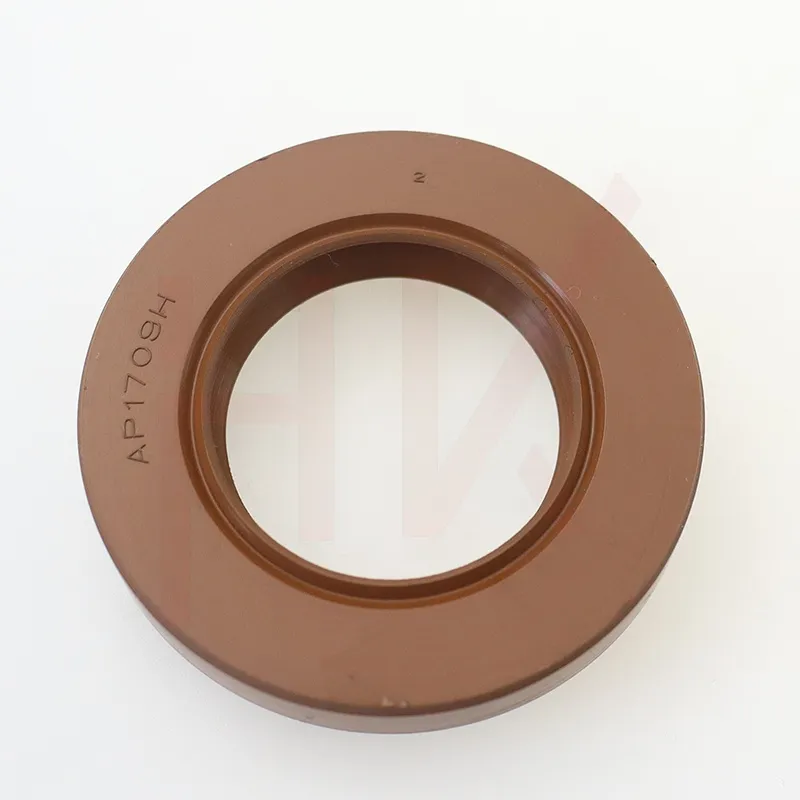
For manufacturing environments characterized by high levels of particulate matter, dust seals play an essential role in safeguarding mechanical equipment. They are often installed in machinery like conveyor systems, pumps, and robotic arms, where contamination could lead to costly downtime and decreased productivity. A well-maintained dust seal can save significant operational costs by minimizing equipment failure and maintenance interventions. Experts recommend scheduling regular inspections of these seals, as their effectiveness can be compromised over time due to material degradation.
In addition to traditional applications, dust seals have found their niche in more specialized fields, such as aerospace engineering, where the stakes of environmental contamination are exceptionally high. Precision machinery used in aircraft must operate flawlessly under variable conditions, and dust seals help ensure this reliability. Aerospace engineers must rigorously test these components under simulated conditions to confirm their performance before deployment.
dust seal
From a technical standpoint, the design of a dust seal can vary to meet different interface requirements. Some seals are designed with a lip configuration, enabling them to maintain contact pressure when components move, thereby not compromising their sealing capabilities. Others utilize a labyrinth design, which provides a tortuous path that is difficult for particles to navigate, hence optimizing the seal's effectiveness without friction-related wear.
The installation of dust seals is a process that demands attention to detail. Proper alignment and application pressure are critical; an incorrectly installed seal can negate its protective function leading to potential system failures. Professionals emphasize utilizing the correct tools and techniques tailored to each application to ensure the seal's optimal performance and longevity.
For businesses looking to integrate effective dust seal solutions, collaboration with manufacturers and suppliers is key. They can offer customized solutions, taking into account specific operational parameters and environmental conditions. Key considerations include factors such as pressure levels, temperature ranges, and the type of contaminants typically encountered. Engaging with suppliers who have a proven track record and expertise can markedly enhance system reliability and performance.
In conclusion, dust seals are an indispensable component of machinery and equipment across multiple industries. Their optimal utilization extends the life of critical components, minimizes maintenance costs, and enhances operational efficiency. To ensure these benefits, regular inspection, appropriate material selection, and precise installation are essential. As the field continues to evolve, advancements in materials and technologies will likely introduce even more effective dust seal solutions, solidifying their importance in industrial and mechanical systems.