Oil seals, often overlooked in the world of machinery and automobiles, play an indispensable role in ensuring the optimal functioning and longevity of various mechanical systems. Without them, machinery would be more prone to leaks, contaminations, and eventual breakdowns, making oil seals critical components in numerous industries.
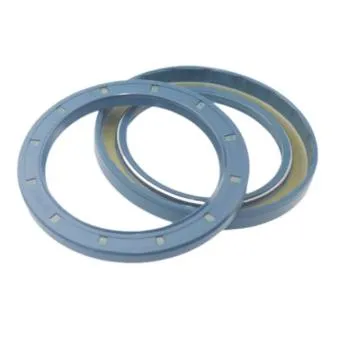
At its core, the function of an oil seal is to close the spaces between stationary and moving components in mechanical equipment, effectively preventing lubricant from escaping. In doing so, oil seals keep contaminants such as dirt, dust, and moisture from entering the machinery, which can cause considerable damage over time. This dual action of retaining lubrication while keeping out harmful contaminants ensures that machinery operates smoothly and efficiently.
Imagine an automotive engine—complex and powerful yet highly susceptible to wear and tear if not properly maintained. Oil seals are paramount here as they prevent oil leakage from the crankcase, a compartment housing the crankshaft. By maintaining the necessary lubrication within the crankcase, oil seals ensure that the engine's moving parts operate with minimal friction. This friction reduction not only enhances performance but significantly extends the engine's life by preventing excessive wear.
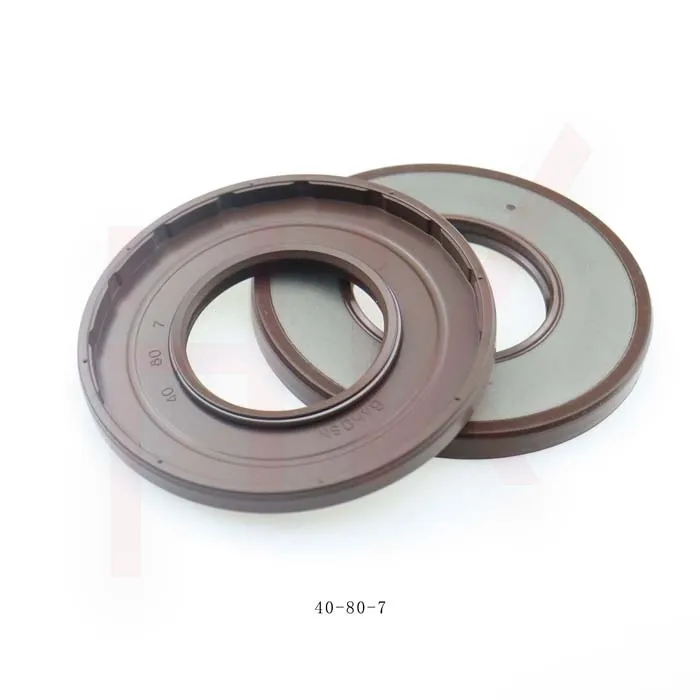
Furthermore, oil seals help in maintaining pressure levels within closed systems, such as hydraulic pumps, which are sensitive to changes in pressure. These seals hold hydraulic fluid in while providing a barrier against external elements. When hydraulic systems have the correct pressure and are free from contaminants, they perform optimally, which is essential for industries reliant on precision such as aerospace and heavy machinery.
From a manufacturing standpoint,
the choice of oil seal material greatly influences its efficacy. Common materials include nitrile and silicone, each with properties suited to different working environments. Nitrile, for instance, is favored for its resilience against petroleum-based oils and its durability under high temperatures. Silicone, on the other hand, offers flexibility and resistance to extreme temperature variations, making it suitable for automotive applications and food processing equipment where sanitary conditions must be maintained.
what is the function of oil seal
Installation of oil seals directly impacts their performance—a fact that's well-backed by experienced technicians across the industry. An improperly fitted seal can lead to early failure, leading to costly repairs and downtime. It's essential to ensure seals are not only installed correctly but matched appropriately to the application in terms of size and material composition. Training and regular maintenance checks are vital, allowing for early detection of seal failures and preemptive measures to avoid system breakdowns.
Technological advancements have ushered in an era of innovation for oil seals, with improvements focusing on enhancing durability, reducing friction, and increasing seal life. High-performance seals, reinforced with advanced materials such as polytetrafluoroethylene (PTFE), offer enhanced wear resistance and lower permeability. These innovations are essential as industries push the boundaries of speed and efficiency, demanding components that can keep up with such rapid advancements.
For product developers and industry professionals, understanding the nuances of oil seal selection and application is crucial. The wrong choice can snowball into inefficient machines and hefty maintenance costs. This expertise in selecting the right seal, backed by a deep understanding of equipment demands, underpins high-performing machines across industries.
In conclusion, the humble oil seal, while not perhaps the most visible of machine components, is fundamental to the durability and efficiency of mechanical operations. Its critical function of maintaining lubrication and keeping out contaminants underscores why it is such an essential part of machinery. Through a combination of expert selection, appropriate material choice, and accurate installation, oil seals can significantly enhance machinery performance and longevity. For engineers and industry professionals, mastering the use of oil seals is both a science and an art, pivotal to unlocking the full potential of their systems.