Ensuring your machinery runs efficiently often hinges on something seemingly minor but crucial the pump seal kit. The longevity and optimum performance of pumps in industrial applications heavily depend on the condition and integrity of the seals. Replacing your pump seal kit is not just a routine maintenance task, but a critical step in protecting your machinery and investment.

Understanding the significance of pump seal kits begins with recognizing their role in minimizing leakage and friction within the pump. Seals act as a barrier, preventing fluid from escaping between the rotating and stationary parts of a pump. Over time, these seals wear out due to various operational stresses, resulting in leaks that can reduce efficiency, increase wear, and lead to costly downtime.
Top-notch performance and reliability are contingent upon selecting the appropriate seal kit for your specific pump model. Original Equipment Manufacturer (OEM) seal kits are generally recommended due to their specific design compatibility, ensuring a seamless fit and optimal performance. Non-OEM alternatives might be enticing due to lower costs, but they often lack the precise engineering and durability standards, potentially leading to premature failure and additional costs in the long run.
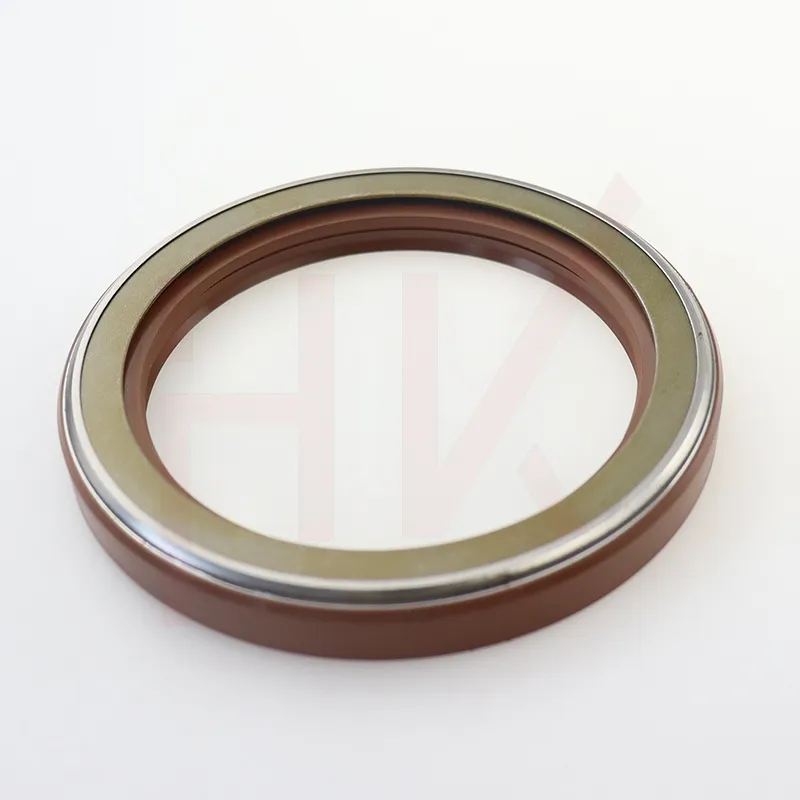
The process of replacing a pump seal kit requires technical expertise to ensure each component is installed correctly. Detailed knowledge of the pump's make and model is essential. Start by consulting the maintenance manual, as it provides the necessary specifications and step-by-step guidance. Gather all required tools before initiating the replacement to avoid interruptions that could compromise efficiency or safety.
One common mistake during replacement is neglecting to inspect new seals for imperfections. Despite being new, always examine them closely for any manufacturing defects or damage. Proper lubrication is also paramount; insufficient lubrication can lead to increased friction, while excess can inhibit their sealing capability. Ensure the sealing surfaces are clean and free from debris to prevent contamination and ensure a secure seal.
pump seal kit replacement
Timing of the replacement also plays a crucial role in maintaining pump efficiency and longevity. Routine inspections should be scheduled in alignment with manufacturer recommendations and adjusted based on the operating environment.
Harsh conditions might necessitate more frequent seal inspections and replacements. An often-overlooked aspect is training personnel on the importance of seal condition and how to recognize early signs of seal failure.
Deploying predictive maintenance techniques, such as vibration analysis and thermal imaging, can further enhance maintenance strategies. These technologies can identify anomalies that indicate impending seal failures, enabling preemptive action before issues escalate. By leveraging such expertise, businesses can reduce instances of unplanned downtime and extend the operational life of their pump systems.
Moreover, the choice of seal materials can significantly impact performance under different conditions. Nitrile, Viton, and EPDM are common materials, each offering distinct advantages. For instance, Viton is renowned for its high-temperature resistance, making it ideal for pumps handling hot fluids. Selecting the right material tailored to the fluid type and operating conditions is pivotal, as it influences the seal's effectiveness and durability.
Building a reputation for trustworthiness involves sharing firsthand experiences. End users who have consistently followed recommended practices report significantly fewer pump breakdowns and extended service life. Case studies illustrating successful seal kit replacements, coupled with testimonials from satisfied operators, strengthen the credibility of a replacement strategy.
In essence, replacing a pump seal kit, though seemingly minor, embodies a critical component of a comprehensive maintenance strategy. By prioritizing proper selection, installation, and maintenance of seal kits, businesses not only protect their equipment but also optimize operational efficiency and cost-effectiveness. With thoughtful consideration and execution, a simple seal replacement transcends its humble nature, becoming an integral aspect of successful industrial operations.