Oil seals, often overlooked in mechanical assemblies, are vital components that ensure operational efficiency and longevity in machinery. These unsung heroes mitigate friction and prevent leakage in various systems, embodying the epitome of engineering precision. Their role in safeguarding machinery against contaminants cannot be overstated, making them indispensable in industries ranging from automotive to aerospace.
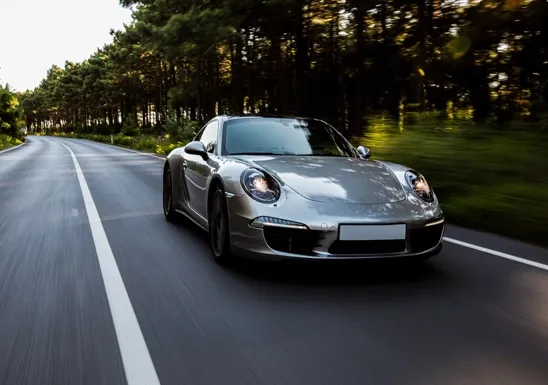
Understanding the nuances of oil seals goes beyond their basic definition. At their core, oil seals are crafted from high-quality materials such as nitrile rubber, fluoroelastomers, and silicone, each chosen for its specific properties and compatibility with the operating environment. This expertise in material selection reflects the industry's commitment to optimizing performance across different applications.
Oil seals are engineered to perform under the most challenging conditions. Their primary function is to prevent the escape of lubricants from machine parts while simultaneously blocking contaminants that could cause wear and tear. For instance, in the automotive industry, oil seals are crucial in engine systems where they prevent oil leaks, ensuring that the engine components are adequately lubricated, thus enhancing performance and reducing maintenance costs.
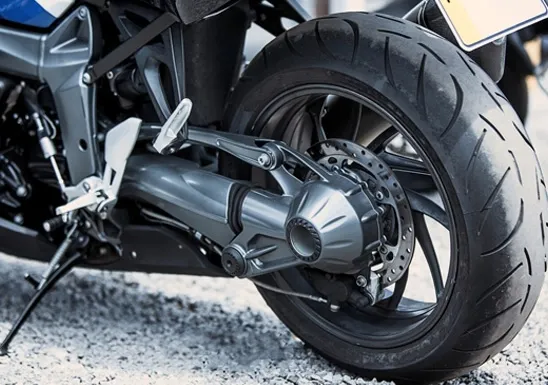
One might wonder about the science behind these seals' effectiveness. The answer lies in their intricate design, which incorporates a sealing lip, a metal case, and a spring. The sealing lip is the part that makes contact with the rotating shaft, maintaining an optimal seal under variable temperatures and pressures. The precision with which these components are manufactured speaks to the industry expertise that guarantees their reliable function.
For professionals in industries that rely heavily on machinery, understanding the different types of oil seals is imperative. There are radial lip seals, rotary seals, and labyrinth seals, each designed for specific applications. Radial lip seals, for example, are prevalent in situations requiring high-speed rotation, offering excellent resilience against leaking even under high-pressure environments. The expertise required to choose the correct type of oil seal for an application can significantly affect machinery’s operational life and efficiency.
The authoritative manufacturing of oil seals involves rigorous testing and quality control. Leading manufacturers adhere to international standards like ISO and DIN, ensuring that each oil seal meets stringent performance criteria before reaching the market. This authoritative approach instills confidence in end-users about the product's reliability and durability.
oil seal
Trustworthiness is a cornerstone of the oil seal industry, with manufacturers placing a premium on transparency and communication. Technical specifications, performance data, and maintenance guidelines are typically provided, allowing users to make informed decisions about their machinery and system requirements. This openness facilitates a trust-based relationship between manufacturers and consumers, ensuring that oil seals meet the highest expectations.
Additionally, sustainability has become a focal point in oil seal production. Many manufacturers are now focusing on creating seals from environmentally friendly materials and processes, reducing waste, and improving recycling efforts. This shift not only underscores the industry's dedication to global sustainability goals but also enhances the trust consumers place in these vital components.
Experience shared by machinery experts and engineers highlights that regular inspection and replacement of oil seals are crucial for preventing unexpected system failures. Worn seals can lead to contamination and subsequent damage to machinery, underscoring the importance of preventative maintenance regimens. Techniques such as visual inspections and leak detections are reliable methods for identifying issues before they escalate.
Furthermore, technological advancements have introduced smart oil seals embedded with sensors capable of monitoring seal condition in real-time. These innovations provide real-time data on parameters like temperature, pressure, and vibration, enabling predictive maintenance strategies that preemptively address potential failures. The advent of such technologies signals a paradigm shift in how traditional components integrate with modern machinery systems, showcasing the industry's continuous pursuit of cutting-edge solutions.
In conclusion, oil seals, though small, play a critical role in the seamless operation of machinery across various industries. Their design, manufacture, and application reflect a high level of specialization and expertise. By understanding the multifaceted nature of oil seals and acknowledging the innovations shaping their future, industries can maintain operational efficiency, uphold safety standards, and achieve new levels of sustainability and trust. As advancements continue to emerge, the role of oil seals will invariably expand, further cementing their status as fundamental components in mechanical systems.