For those delving into the world of mechanical engineering or automotive maintenance, understanding the invaluable role of the 35 52 7 oil seal is crucial. An oil seal, often regarded as a fundamental component, plays a critical role in preventing lubricants from escaping the bearings or a specific area in machinery, ultimately ensuring efficient and smooth operation of mechanical parts.
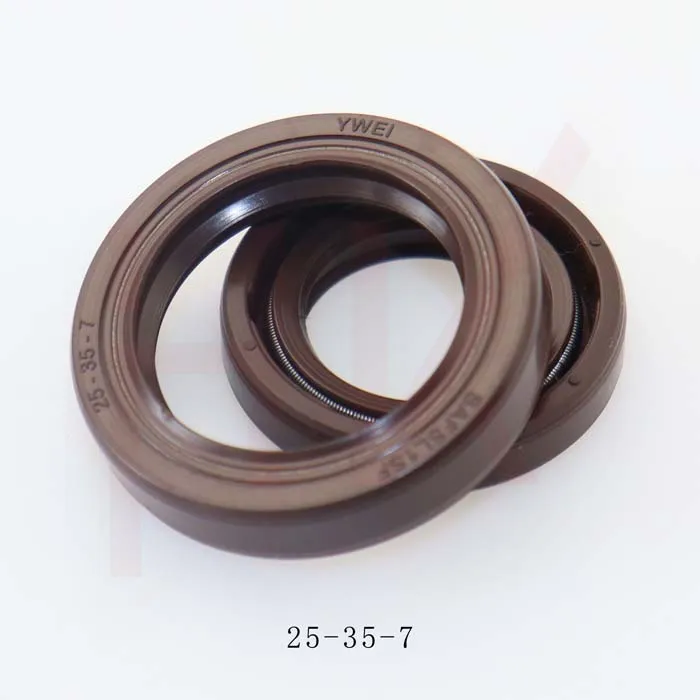
The 35 52 7 designation provides specific insights into the oil seal’s dimensions, a critical aspect for ensuring a precise fit and functionality. The first number, 35, denotes the inner diameter of the oil seal in millimeters, ensuring a snug fit around a shaft or rod. The second number, 52, represents the outer diameter, and the final number, 7, indicates the thickness or width of the seal. These measurements are essential for professionals and hobbyists alike, allowing them to select the correct seal, thereby preventing water, dust, or any other contaminants from infiltrating the oil.
Throughout history,
the concept of sealing has evolved remarkably. The development and innovation in oil seal technology have been driven by an ever-increasing demand for enhanced performance in various sectors, including automotive, aerospace, and manufacturing industries. The 35 52 7 oil seal, with its precise dimensions, exemplifies this advanced evolution, specifically designed to accommodate stringent requirements of contemporary industrial applications.
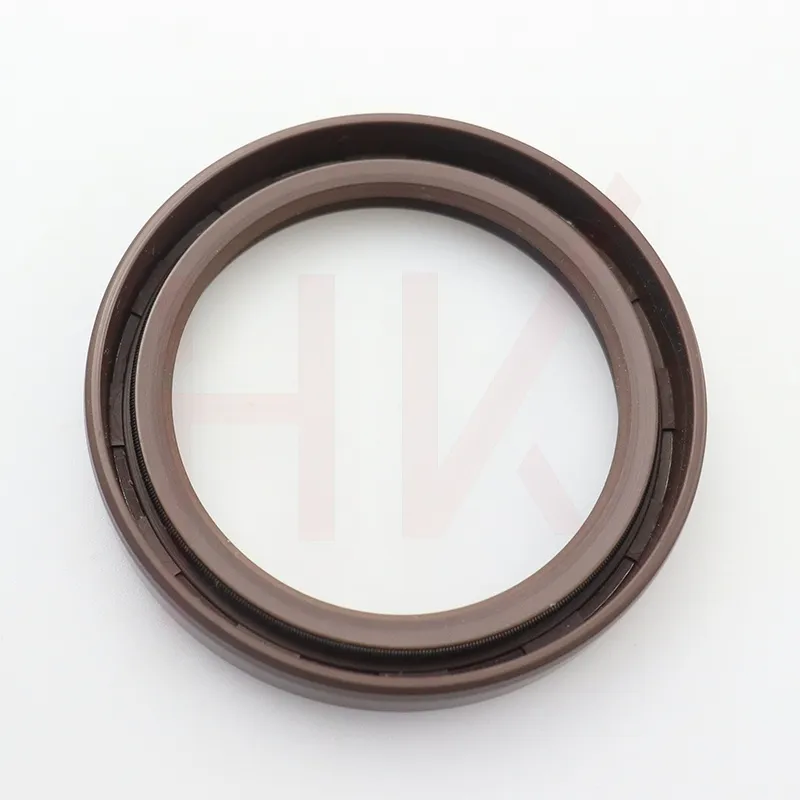
The engineering behind these oil seals incorporates superior materials that offer resistance to high temperatures, chemical corrosion, and wear. Typically made from nitrile rubber, silicone, or fluoroelastomer, these materials provide excellent durability and elasticity, crucial for enduring the rigorous demands of high-speed rotational environments. The choice of material is pivotal, as it impacts the seal’s longevity and effectiveness, which defines the difference between uninterrupted operation and costly downtime.
Moreover, the design of the 35 52 7 oil seal involves a lip configuration that enhances its sealing capabilities. The lip or edge of the seal is engineered to maintain a consistent contact with the rotating shaft, adapting to any shaft misalignments, thereby maintaining a robust sealing surface. This innovative design reduces friction, minimizes wear, and prevents lubricant leakage—a vital function that industry professionals heavily rely upon.
35 52 7 oil seal
The real-world application and success of the 35 52 7 oil seal in industrial settings are testament to its reliability and efficiency. In automotive engines, for instance, it is instrumental in maintaining the engine oil within the crankshaft, preventing it from leaking into the surrounding environment, which could otherwise lead to reduced performance or even severe mechanical failures. Its application extends to pumps, compressors, and a variety of rotating machinery, where maintaining the integrity of the lubrication system is paramount.
Professionals seeking to procure the 35 52 7 oil seal must ensure that they source from reputable manufacturers known for adhering to quality standards. Ensuring authenticity and quality in oil seals is vital as sub-standard seals may lead to premature failure, risking damage to machinery and increased maintenance costs. Trusted suppliers will provide certifications and quality guarantees that reinforce the reliability of their products.
The importance of understanding the 35 52 7 oil seal lies not just in its dimensions but in the broader context of its application and critical role in machinery maintenance. It represents a blend of engineering innovation, material science, and mechanical necessity. By maintaining lubricant integrity and preventing contamination, the 35 52 7 oil seal enhances machinery longevity, promotes efficiency, and is integral to maintaining operational excellence across various sectors.
In conclusion, whether you are a seasoned mechanical engineer or a dedicated DIY enthusiast, comprehending the specifics of the 35 52 7 oil seal is indispensable. It exemplifies the interplay of precision engineering and practical application—qualities that solidify its standing as an authoritative component in mechanical systems. As technology progresses, the principles that define the utility of oil seals will continue to evolve, yet the essential need for such precise, reliable components remains unchanged in the pursuit of mechanical efficiency and durability.