Unlocking the Secrets of 70 90 10 Oil Seals A Comprehensive Guide to Performance and Reliability
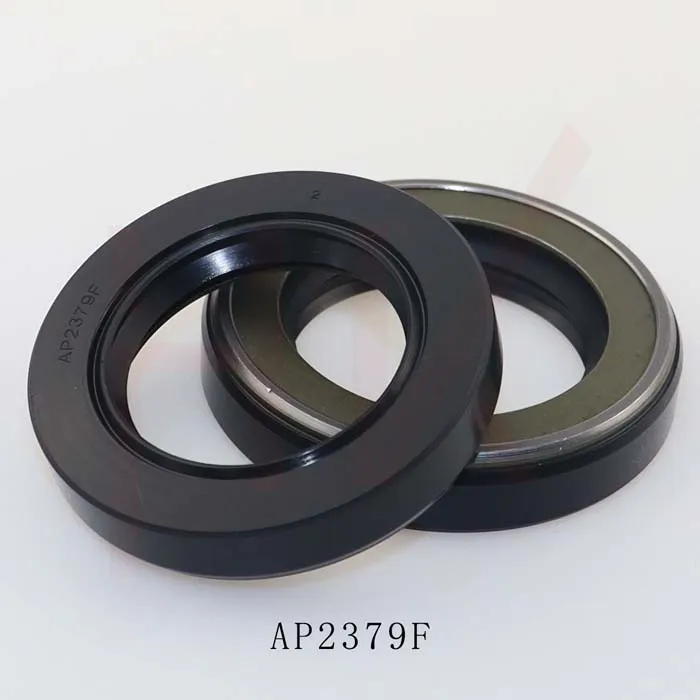
In the world of mechanical engineering and machinery maintenance, the oil seal plays a crucial role in ensuring the longevity and optimal performance of various components. Amongst the plethora of oil seals available, the 70 90 10 oil seal stands out due to its unique specifications and widespread applications. But what exactly makes this seal an indispensable element in machinery and automotive industries? Let's delve into the technicalities and the unparalleled benefits of the 70 90 10 oil seal, providing insights that combine both expertise and trustworthiness.
To understand the importance of the 70 90 10 oil seal, it's essential to deconstruct what these numbers represent. The specification denotes the dimensions of the seal 70mm inner diameter, 90mm outer diameter, and a 10mm width. These measurements are crucial for ensuring a snug fit in the designated housing and the ability to provide an effective barrier against lubricant leakage and contamination ingress. The geometric precision offered by the 70 90 10 oil seal directly influences the operational reliability of the machinery.
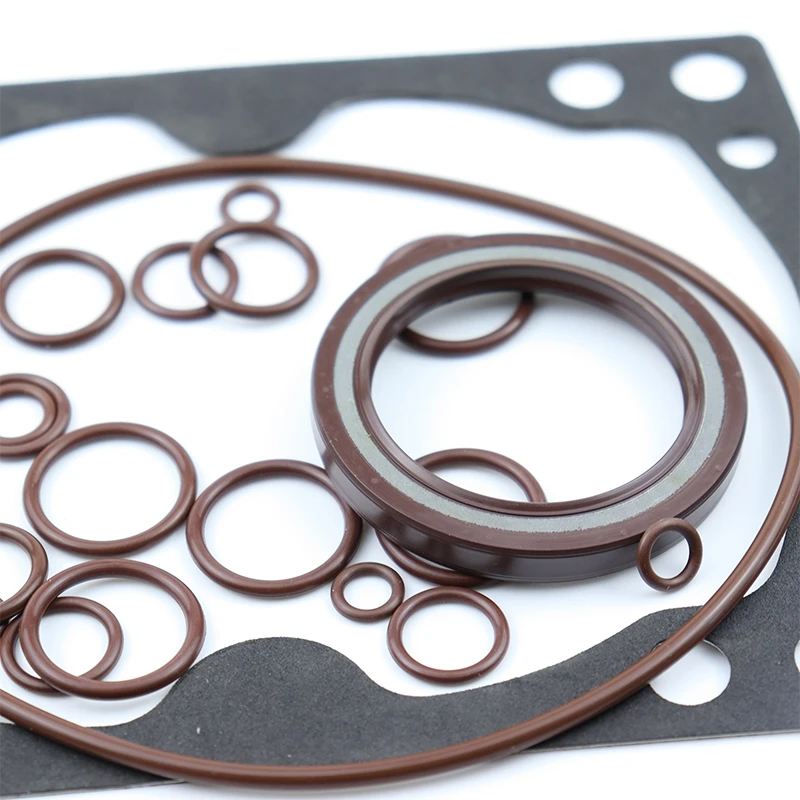
Experience with different machinery types reveals that choosing the right oil seal size directly impacts the machine's operational stability. The right fit minimizes vibrations and prevents unwanted oil seepage — a fact corroborated by countless field experts and technicians. The 70 90 10 oil seal, due to its commonly required dimension, is frequently used in industries such as automotive, manufacturing, and heavy equipment, where machine downtime can result in significant financial loss.
Professional engineers and technicians recognize the material composition of oil seals as a critical factor determining their performance. The 70 90 10 oil seal is typically constructed from high-quality nitrile rubber (NBR) or fluoroelastomer (FKM). Nitrile rubber is renowned for its resistance to petroleum-based oils, wear, and thermal degradation, making it a popular choice for general-purpose applications. Conversely, fluoroelastomer comes into play in environments involving higher temperatures and aggressive chemicals, offering superior resistance and longer lifespan.
70 90 10 oil seal
Authoritative studies and reports on oil seal performance stress the importance of selecting the appropriate seal material based on the operational environment. The robustness and chemical compatibility of the 70 90 10 oil seal material significantly enhance its efficacy, reducing the need for frequent replacements and maintenance checks.
Trustworthiness in product quality is another critical concern for industries relying on oil seals for their operations. The 70 90 10 oil seal is often subjected to rigorous quality tests to ensure that they meet industry standards and specifications.
Tests include assessments of tensile strength, durability under high pressure, and flexibility at varying temperatures. A product with proven longevity and reliability reduces the anxiety of unexpected failures and promotes confidence in the machinery's long-term performance.
The synergy between precision engineering and material science has led to the evolution of oil seal designs, transforming the 70 90 10 oil seal into a vital component for professionals seeking efficiency and reliability. The consistent feedback from users across multiple industries reinforces its reputation and authority in the market.
In summary, the 70 90 10 oil seal is more than just a mechanical component; it embodies the intersection of experience, expertise, and trustworthiness in industrial applications. By understanding its specifications, material advantages, and performance benchmarks, businesses and technicians can make informed decisions that enhance machinery longevity and operational efficiency, cementing the oil seal's place as a cornerstone of industry reliability.