Choosing between dust seals and oil seals is a crucial decision for many industries involved in machinery maintenance and performance optimization. Each type of seal serves a unique function, and understanding their differences is vital for ensuring equipment longevity and efficiency.
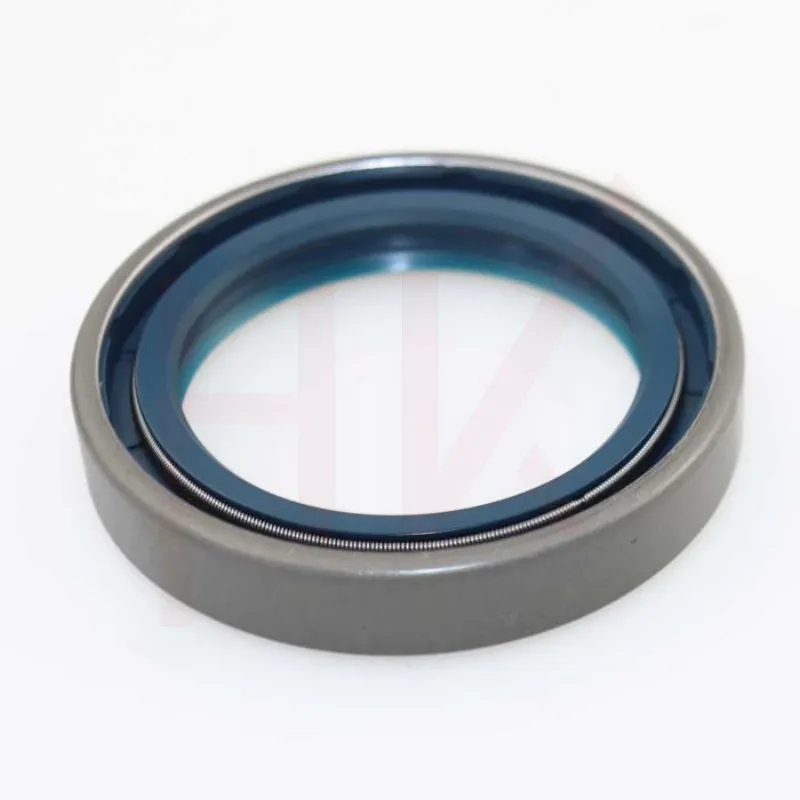
Dust Seals Protecting Against Environmental Contaminants
Dust seals serve as a frontline defense against external contaminants that could otherwise penetrate machinery and cause premature wear or corrosion. These seals are typically used in environments where dust, dirt, or other particles are prevalent. Industries such as construction, mining, and agriculture often deploy machinery in challenging, particle-laden environments, making dust seals essential.
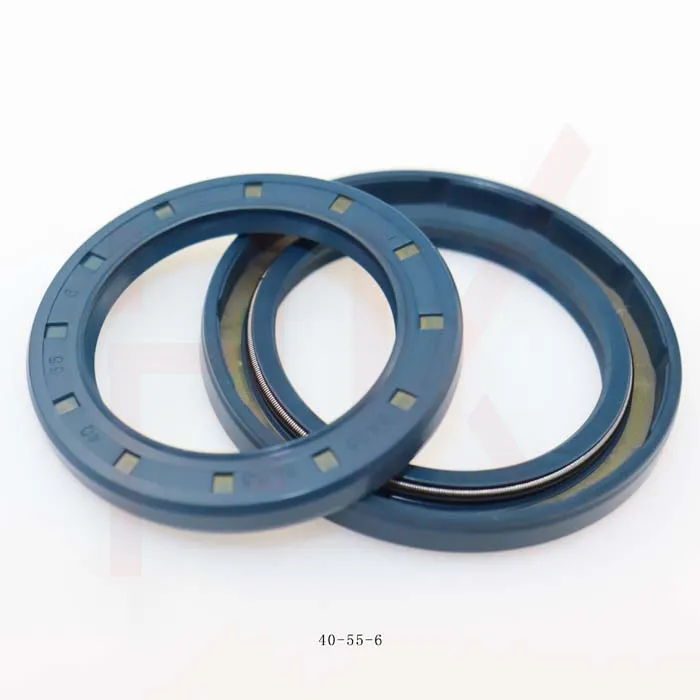
A quintessential feature of dust seals is their ability to prevent particulate ingress without the use of lubrication. This characteristic is particularly beneficial in situations where lubricants could attract more debris, leading to faster accumulation of contaminants. Often made from flexible materials such as rubber or silicone, dust seals form a tight yet dynamic seal around moving parts, allowing for both protection and flexibility.
Oil Seals Ensuring Lubrication Integrity
Oil seals, on the other hand, excel in environments where it is crucial to retain lubricants within a system. Commonly applied in engines, gearboxes, and other assemblies where oil retention is necessary, these seals prevent lubricating fluids from leaking out while simultaneously keeping contaminants from entering.
Constructed from durable materials like nitrile or Viton, oil seals ensure a firm fit between stationary and moving surfaces. Their primary role is to maintain an optimal environment for lubrication, reducing friction between components, thus extending their operational lifespan. In high-speed applications, the precision of oil seals becomes even more critical, making material selection and design paramount.
The Distinct Roles in Industrial Applications
In industrial applications, dust and oil seals fulfill distinct yet complementary roles. Selecting the right seal significantly affects equipment durability and performance, impacting maintenance schedules and operational costs. For instance, heavy-duty vehicles in mining operations face harsh conditions where both dust and lubricants are abundant. Here, using a combination of both dust and oil seals to protect different parts of the machinery might be necessary.
Understanding the specific application scenarios is key. For static applications where the primary concern is contaminant exclusion without regular lubrication, dust seals might suffice. Conversely, in dynamic applications with high-speed movements where lubrication is integral, oil seals become indispensable.
Maintenance and Replacement Considerations
dust seal vs oil seal
Seal maintenance and regular replacement form a critical part of machinery upkeep. For dust seals, regular cleaning and inspections can prevent contaminant buildup, which could compromise the seal's integrity. Oil seals, however, demand a focus on checking for leaks and ensuring no hardening or cracking of the material, which might indicate impending failure.
When replacing seals, ensuring compatibility with existing components and operating environments is vital. Material resilience against temperature variations, chemical interactions, and abrasive wear is crucial to prevent premature failure.
Choosing the Right Seal Factors to Consider
Several factors should guide the selection between dust seals and oil seals, including
1. Operating Environment Evaluate whether the exposure to dust and dirt is more significant than concerns about oil leakage or vice versa.
2. Material Properties Consider the chemical and thermal compatibility of the seal material with the application environment.
3. Seal Geometry Custom geometric considerations, such as the interaction between the seal and the shaft, can influence the effectiveness of the seal.
4. Cost and Availability Cost-effectiveness and the ease of sourcing replacement seals are practical considerations that can influence long-term maintenance strategies.
Innovation and Future Trends
As technology advances, new materials and seal designs continue to emerge, aimed at enhancing the performance and longevity of both dust and oil seals. Advanced composite materials and coatings are now available, offering increased resistance to wear and chemical exposure. Additionally, developments in seal geometry have led to designs that reduce friction and energy consumption, aligning with global sustainability goals.
In conclusion, the choice between dust seals versus oil seals should be guided by a clear understanding of the application's specific environmental and operational demands. Whether it’s protecting machinery in a dusty mine or ensuring oil integrity in a high-performance engine, selecting the right seal can significantly impact the efficiency and life expectancy of the equipment they protect. With continuous innovations, the future of sealing technology promises even more efficient and sustainable solutions, aiding industries in achieving optimal performance and reduced downtime.