Oil seals, often referred to as rotary shaft seals or radial lip seals, play a critical role in numerous industrial applications by ensuring the smooth operation of machinery and preventing leaks. The design, material selection, and installation process of oil seals demand not only technical expertise but also practical experience to maximize performance and longevity.
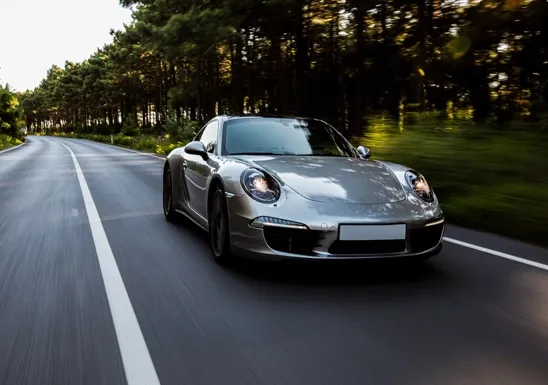
The primary function of an oil seal is to separate environments, retaining lubricants within a chamber while barring contaminants such as dirt and moisture from entering the system. Their importance is paramount in industries like automotive, agriculture, and manufacturing, where machinery uptime and reliability are critical factors for success.
From an expert's perspective, selecting the appropriate oil seal involves a thorough understanding of the operational environment. Temperature, pressure, speed, and the type of lubricant all influence seal performance. For example, in automotive applications, oil seals that withstand high temperatures and high-speed rotations are essential for engine efficiency and durability. Neoprene and Viton are popular materials for these conditions due to their heat resistance and durability.
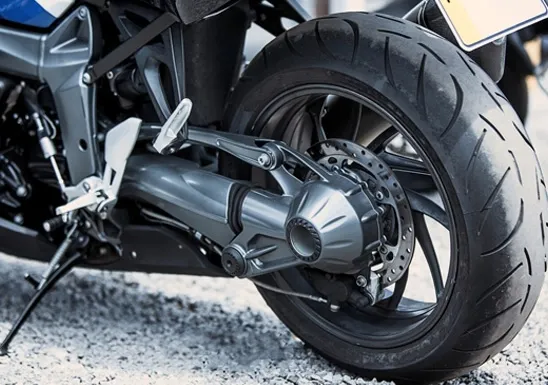
Trustworthiness in oil seal selection also hinges on sourcing from reputable manufacturers known for consistent quality in materials and compliance with industrial standards. Products from established brands often undergo rigorous testing and quality assurance processes, ensuring that they meet the stringent demands of various applications. This guarantees that users not only receive durable products but also attain peace of mind from the reliability and safety provided.
oil seal
The installation process is another critical factor in ensuring oil seals perform optimally.
Even the most expertly chosen seal can fail if improperly installed. Experience teaches that meticulous inspections of the shaft and housing conditions are indispensable before installation. These components must be free from burrs and imperfections to prevent premature wear or failure. Adequate lubrication during installation further ensures that the seal seats properly and begins operations without undue stress.
For professionals and maintenance experts, real-world experiences highlight that regular monitoring and maintenance extend oil seals' lifespan. Observing indicators of potential failure such as oil leaks, unusual noises, or vibrations can prevent costly downtime and repairs. Over time, even perfect installations can be compromised by factors like misalignment or persistent exposure to aggressive chemicals.
To enhance the authoritativeness of decisions regarding oil seals, leveraging technical resources, such as specification sheets and failure analysis reports, can be instrumental. Engaging with industry forums or attending specialized training sessions can also help professionals stay abreast of the latest advancements and troubleshooting techniques.
Overall, the reliable performance of oil seals in various industries is a testament to the blend of experience, expertise, and trust in manufacturing and application. Their role in reducing environmental impact by preventing leakage and contamination aligns with modern industrial sustainability goals, making them indispensable in both current and future technological landscapes.