High pressure oil seals play a crucial role in the seamless operation of machinery across various industries. As equipment becomes more sophisticated, the demand for robust components capable of withstanding intense conditions grows. This article sheds light on the nuances of high pressure oil seals, offering insights constructed from years of hands-on experience.
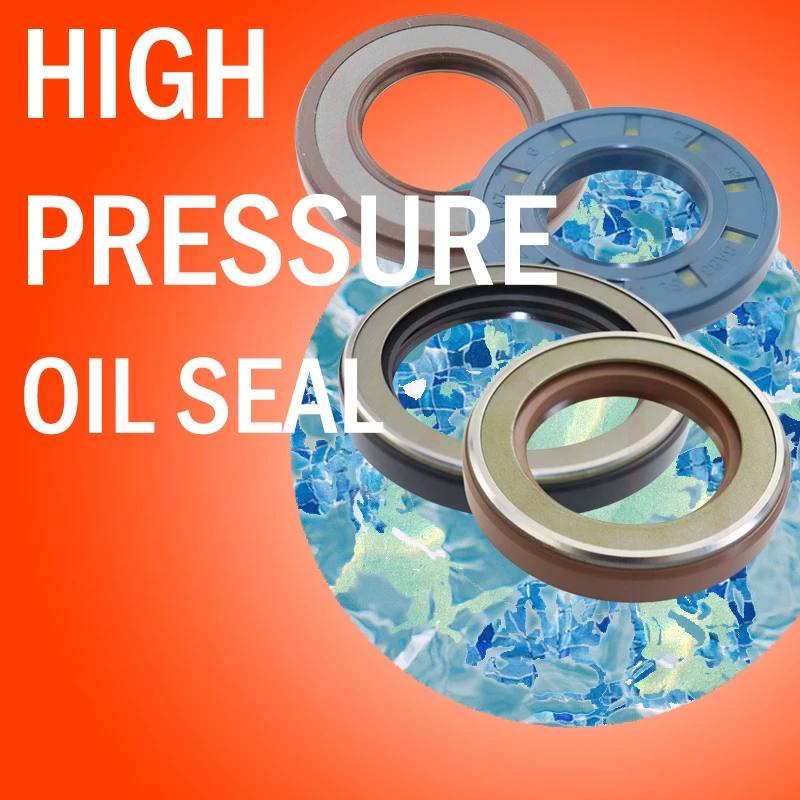
High pressure oil seals, commonly used in sectors such as automotive, aerospace, and manufacturing, are designed to prevent the leakage of lubricants or fluids. A deep understanding of material science combined with mechanical engineering is essential to designing seals that can operate efficiently under high pressure. Seals are crafted from advanced materials such as nitrile rubber, fluorocarbon, and polyacrylate, each offering unique benefits in terms of temperature resistance, durability, and compatibility with different fluids.
One noteworthy aspect of high pressure oil seals is their reliance on precise engineering to fit seamlessly within various mechanical systems. Incorrect fitting can lead to disastrous leakage, causing damage and substantial downtime. As an expert in the field has noted, “The success of these seals lies in the minute tolerances and the quality of the materials used. Even a marginal error in dimensions can compromise the entire system.” This principle underscores the importance of precision engineering.
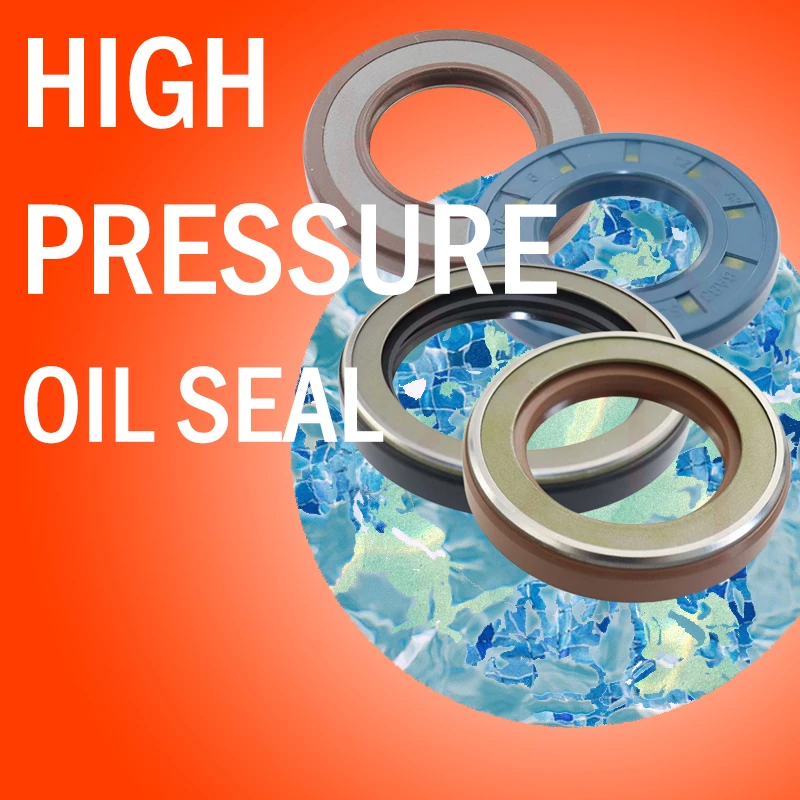
The choice of high pressure oil seal also depends on the specifics of its application. In an environment where machinery is exposed to extreme temperatures, such as in aerospace applications, seals must resist thermal expansion and contraction. Seals used in these scenarios are typically reinforced with a combination of high-performance elastomers and metals, ensuring they maintain integrity under thermal stress. Expertise in the selection process and application knowledge significantly enhances the seal’s effectiveness and lifespan.
high pressure oil seal
Moreover, the very nature of high pressure oil seals calls for reliability. Regular testing and quality assurance checks should be conducted to verify their capacity to withstand expected conditions. Testing methodologies often include pressure cycling and temperature variation tests, which mimic the real-world challenges the seals will face. Companies renowned for their expertise in seals subject them to rigorous testing, enhancing trustworthiness and ensuring that end-users receive products that meet their specifications.
Beyond the technical specifications, brand reputation also influences the credibility of high pressure oil seals. Manufacturers that have been in the industry for decades offer insights not just from past successes, but also from understanding and adapting to failure modes. Their long-standing presence suggests a proven track record of innovation and reliable performance—a critical factor for customers prioritizing trustworthiness in their purchasing decisions.
High pressure oil seals are fundamental to operational efficiency, safeguarding machinery from the adverse effects of leakage. The practical insights mentioned here aim to guide decision-makers toward informed purchases grounded in technical expertise and reliability. As industries continue to evolve, innovations in seal technology will be instrumental in meeting future demands, making a deep understanding of these components invaluable to practitioners and businesses alike.