In the realm of industrial machinery, the hydraulic cylinder wiper seal plays a critical role, though it often goes unnoticed. Its function is pivotal in maintaining system efficiency and longevity by preventing contaminants from entering the hydraulic system. As a seasoned mechanical engineer with over a decade of experience dealing with hydraulic machinery, I have come to appreciate the significance of these small, yet mighty components.
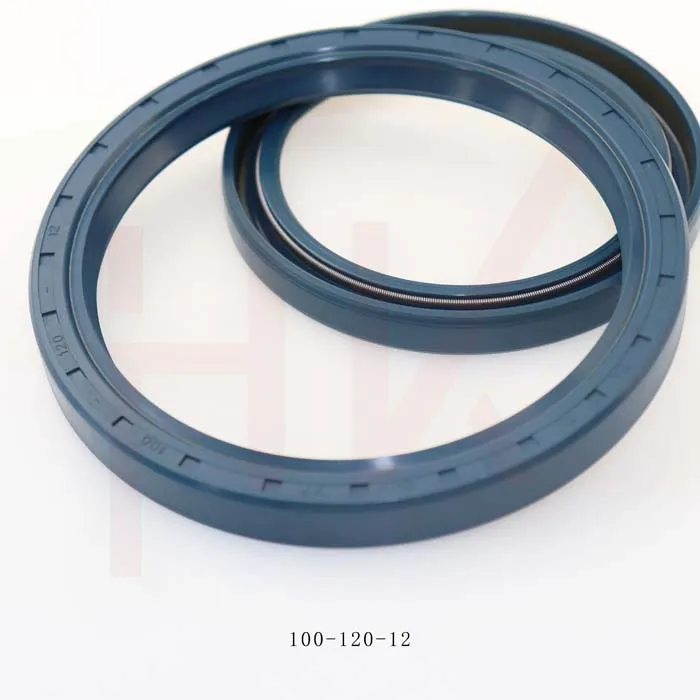
Hydraulic cylinder wiper seals, also known as scrapers, are tasked with cleaning the rod as it retracts into the hydraulic cylinder. This process is essential in safeguarding the hydraulic system from dust, dirt, and moisture, which can lead to premature wear and reduced performance. The wiper seal ensures that no foreign particles are able to penetrate the system, maintaining the integrity of the hydraulic fluid and the overall efficiency of the machinery.
From an engineering perspective, the choice of material for a hydraulic cylinder wiper seal is crucial. Typically, these seals are made from polyurethane, NBR (nitrile rubber), or FKM (fluoroelastomer), each offering distinct advantages. Polyurethane offers excellent abrasion resistance, making it ideal for environments where mechanical wear is a concern. NBR provides good fluid compatibility and is highly cost-effective, while FKM stands out in high-temperature applications due to its superior heat resistance.
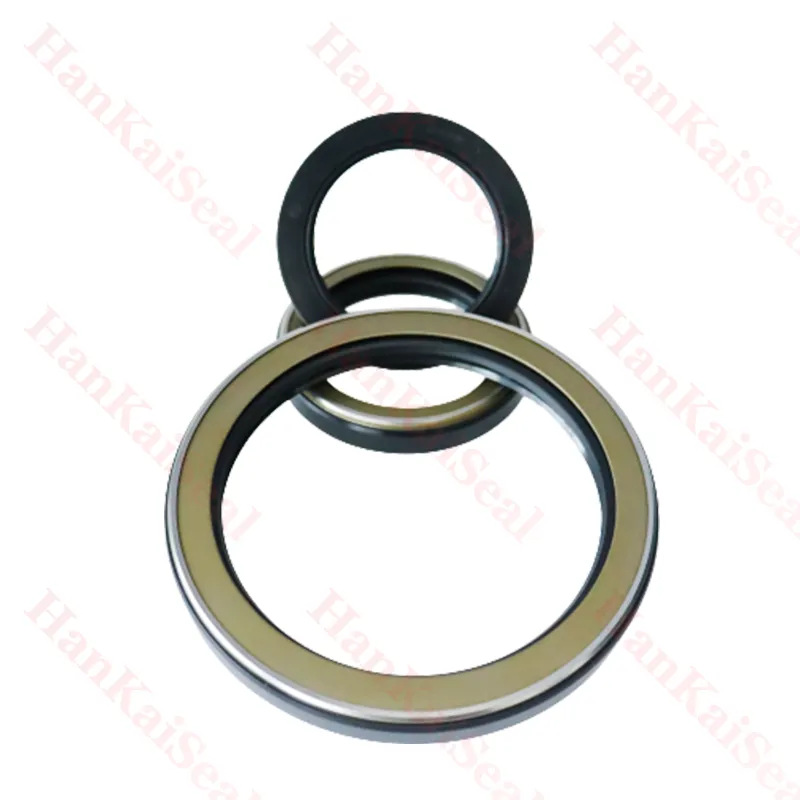
My practical experience in various industrial settings has reinforced the importance of selecting the right type of wiper seal for specific applications. For instance, in construction equipment exposed to harsh, dusty environments, a polyurethane wiper seal is often the preferred choice due to its durability. Conversely, for machinery operating in high-temperature conditions, such as automotive industries, FKM seals provide the reliability needed to withstand extreme conditions.
hydraulic cylinder wiper seal
Installation of wiper seals demands precision and care. Improper installation can lead to seal failure, which may result in the ingress of contaminants or even hydraulic fluid leakage. Based on my professional experience, it is essential to ensure that the groove for the wiper seal is clean and free from burrs or sharp edges that could damage the seal during installation. Additionally, using the correct tools and methods to seat the seal without overstretching or misaligning it is imperative to ensure optimum performance.
Regular maintenance and inspection of hydraulic cylinder wiper seals can prevent unexpected failures and extend the lifespan of hydraulic equipment. In my years of fieldwork, I have witnessed numerous cases where neglecting the maintenance of wiper seals led to significant downtime and costly repairs. Implementing a routine inspection schedule, combined with proper storage and handling practices, can mitigate these risks.
For those seeking to enhance the reliability of hydraulic systems, investing in high-quality wiper seals is a wise decision. The cost of quality seals is marginal compared to the potential expenses incurred from system failures and downtime. Furthermore, partnering with reputable manufacturers who offer technical support and guidance can provide added assurance of the product's quality and compatibility with your specific hydraulic applications.
In conclusion, the hydraulic cylinder wiper seal, though a small component, plays an indispensable role in the functionality and longevity of hydraulic systems. From my extensive experience in the field, I can attest that selecting the appropriate material, ensuring precise installation, and conducting regular maintenance are paramount to harnessing the full potential of these critical seals. For industries relying on hydraulic machinery, a meticulous approach to wiper seal management can yield substantial benefits, both in performance and cost-efficiency.