In the world of hydraulics, precision and reliability are of utmost importance.
Oil seals, often underappreciated, play a critical role in the functionality of hydraulic systems. These small but mighty components ensure peak performance by preventing fluid leakage and contamination, crucial to maintaining system integrity.
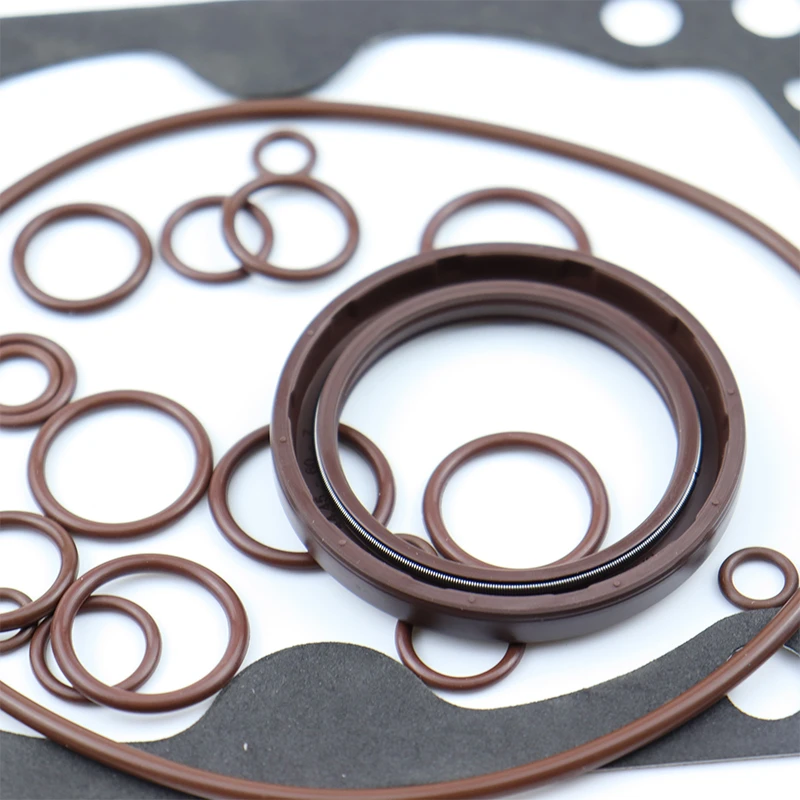
Oil seals are essential in hydraulic systems, acting as barriers that separate different substances while containing lubricants within the machinery. Composed primarily of high-grade rubber or elastomers, sometimes paired with metal reinforcements, oil seals boast a construction that withstands extreme pressures and temperatures. The choice of material is not arbitrary; it is meticulously selected based on the intended application, aligning with the system’s parameters to ensure longevity and efficiency.
Craftsmanship backed by expertise in engineering and material science stands at the core of oil seal production. The intricate manufacturing process, guided by precise specifications, reflects an understanding of the myriad challenges hydraulic systems encounter. A significant factor that contributes to the dependability of oil seals is their design versatility, catering to various applications across industries, from automotive to aerospace.
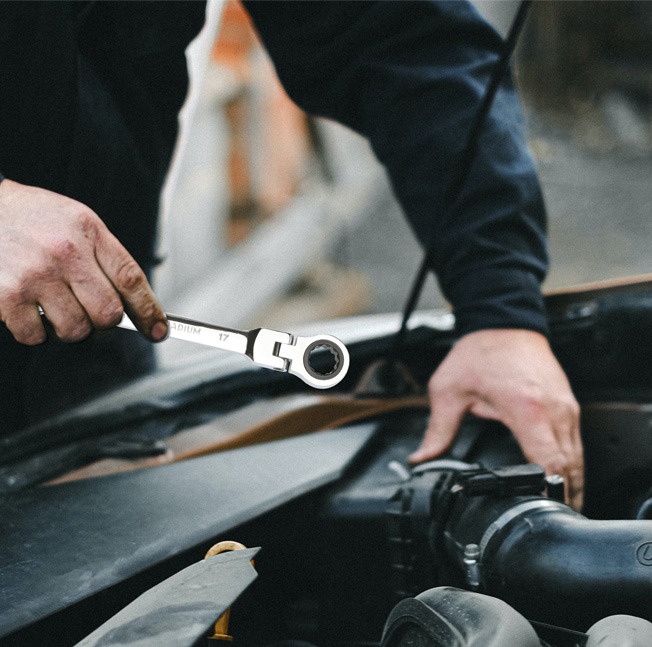
Experience in utilizing high-grade oil seals has consistently underscored their importance in hydraulic systems. One of the most prominent examples is their use in excavators, where they must perform under continuous pressure cycles and extreme environmental conditions. Failure to use quality oil seals often results in operational downtime, increased maintenance costs, and premature wear of hydraulic components. Professionals with decades of experience attest to the fact that investing in reputable oil seal products can save thousands in repair and maintenance costs.
oil seal hydraulic
Besides mechanical reliability, the role of oil seals in maintaining ecological compliance is noteworthy. In response to tightened environmental regulations across the globe, industries are recognizing the value of oil seals in preventing hydraulic leaks that can result in soil and water contamination. Utilizing advanced sealing solutions exemplifies a commitment to sustainability, setting industry standards and commanding respect for responsible operation.
Authoritativeness in the realm of oil seal technology is underscored by constant innovation and adherence to rigorous testing standards. Reputable manufacturers invest heavily in research and development, exploring new materials and designs to push the boundaries of performance. Engineers are tasked with aligning product innovation with feedback from field applications, ensuring each new iteration of oil seals meets or exceeds industry requirements.
With trust becoming a critical factor in supplier relationships, the transparency and reliability demonstrated by leading oil seal manufacturers cement their position as indispensable partners in hydraulic system design. From providing detailed product specifications to supporting engineers with installation guidance and troubleshooting, the level of customer support is unparalleled. Testimonials from industry veterans highlight the peace of mind gained from such partnerships, reinforcing the notion that quality oil seals contribute significantly to the overall success of hydraulic operations.
In conclusion, the journey of integrating oil seals into hydraulic systems is marked by a blend of art and science. Their significance transcends basic functionality, offering a confluence of performance benefits that enhance system integrity, operational efficiency, and environmental compliance. By selecting the right oil seal solutions, industries not only avert unnecessary operational setbacks but also embrace a future oriented towards innovation and sustainability. In this regard, oil seals are not just components—they are linchpins of industrial excellence.