Dust lip seals play an integral role in safeguarding machinery against contaminants and enhancing the longevity of equipment. In today's industry, where machinery precision is paramount, utilizing the right dust lip seal can mean the difference between optimal performance and mechanical failure.
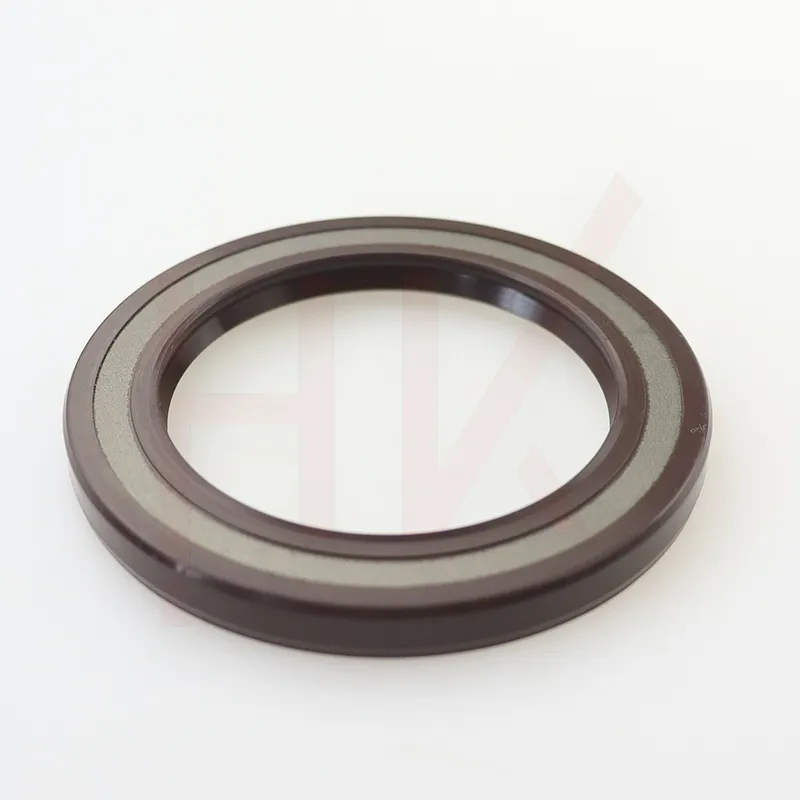
When considering the inclusion of dust lip seals in machinery, firsthand experience underscores their effectiveness in sealing out dust, dirt, and grime. Implementing dust lip seals in various industrial settings has demonstrated a noticeable improvement in equipment performance and reduced maintenance requirements—a testament to their practical value. Operators often report longer intervals between service due to the reduced ingress of particles that can cause abrasive wear.
From an expertise standpoint, dust lip seals are engineered with a keen eye on material science, selecting polymers and elastomers that withstand harsh operating conditions. For example, these seals are often fabricated from nitrile, silicone, or Teflon materials, each offering unique properties tailored to specific environments. Nitrile seals excel in applications involving exposure to petroleum-based oils, while silicone provides superior performance in wide temperature ranges, and Teflon is renowned for its chemical resistance. This variety allows for customization based on machinery needs, ensuring that the seals not only fit but also enhance machinery efficiency.
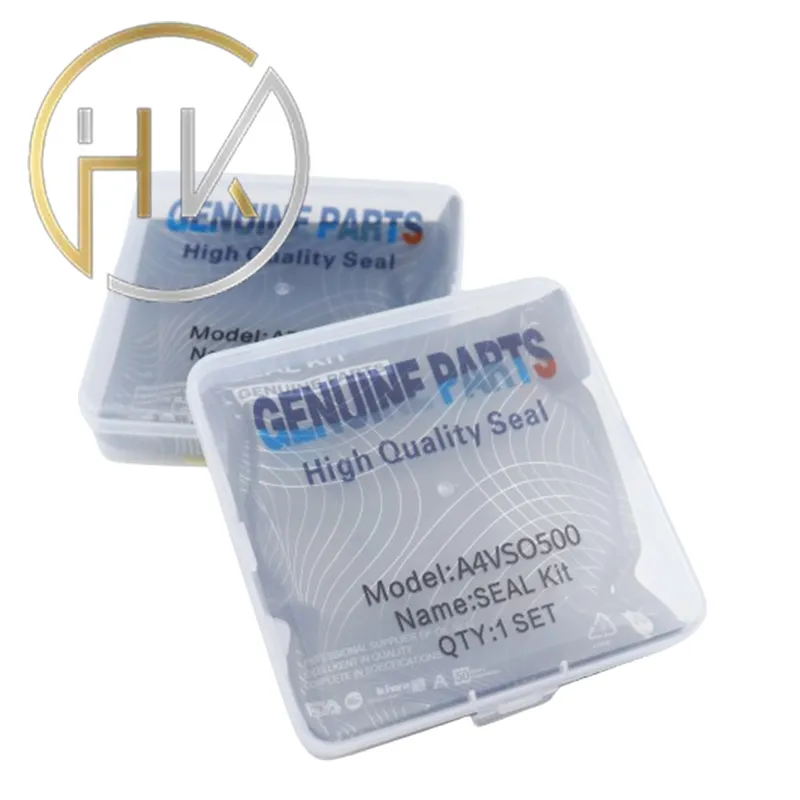
In terms of authoritativeness, industry data backs up the application of dust lip seals as a crucial component in mechanical design. Studies have highlighted how the inclusion of these seals can reduce equipment downtime by up to 50% and extend machinery lifespan significantly. Moreover, the adoption of innovative designs such as multiple lip configurations offers enhanced protection and even load distribution, which is critical for maintaining the mechanical integrity of rotating equipment.
dust lip seal
Trustworthiness is fostered by the reliability and consistent performance of dust lip seals, which are often tested rigorously under simulated operational conditions before they reach the consumer. Manufacturers commit to stringent quality control standards, often using high-resolution inspection techniques to ensure defect-free products. User testimonials frequently emphasize the peace of mind afforded by using reputable seal brands, which deliver on promises of durability and protection.
Integral to modern machinery, dust lip seals set a benchmark in protection against wear and tear, with their design focused on durability and reliability.
As technology progresses, sealing solutions evolve to meet new industry standards. Smart seals—integrating sensors to monitor environmental conditions—represent the future of machinery components, offering real-time data and predictive maintenance capabilities. This innovation not only boosts the efficacy of seals but asserts their place in the evolving landscape of smart manufacturing.
In conclusion, with dust lip seals, industries gain an invaluable tool that not only enhances machinery longevity but also promotes sustainable practices by minimizing waste and reducing energy consumption. By choosing the right sealing solution from reputable manufacturers, businesses commit to safeguarding their technology investments and maintaining operational excellence. In essence, the right dust lip seal simplifies maintenance, cuts costs, and ensures peak performance—all critical factors in today’s competitive industrial environment.