Navigating the realm of high-pressure seals reveals a crucial component in many industrial applications, where the integrity of fluid systems is paramount. High-pressure seals are indispensable in industries ranging from aerospace and automotive to oil and gas and chemical manufacturing. Their design, material composition, and installation dictate their performance, while their failure can lead to catastrophic consequences. This article delves into the intricate world of high-pressure seals, offering valuable insights grounded in years of field experience and technical expertise.
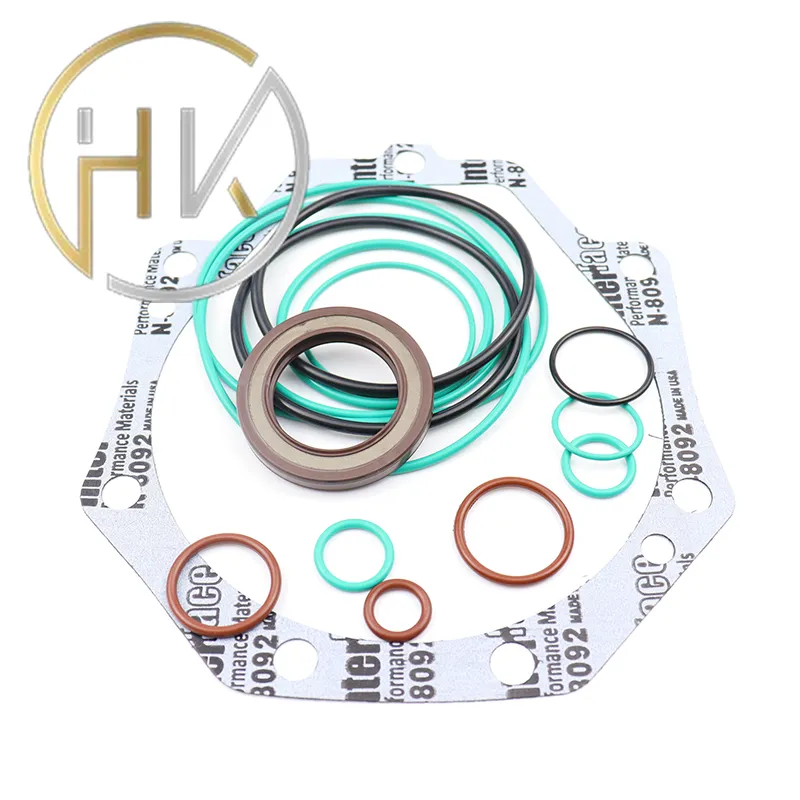
Understanding the role of high-pressure seals begins with recognizing their function in preventing leaks in systems under tremendous pressure. Whether in hydraulic cylinders or pipelines, these seals maintain system efficacy and safety, mitigating environmental hazards and financial losses. Their robustness makes them suitable for environments where standard seals would falter, handling extreme pressures over 10,000 psi with ease.
The design of high-pressure seals is tailored to specific applications, considering factors such as temperature, pressure, and the nature of the fluid being contained. Materials like PTFE, elastomers, and advanced composites are often employed for their exceptional durability and resistance to chemical degradation. A critical element in the design process involves finite element analysis (FEA), a computational tool that simulates how the seal performs under various conditions. This predictive model helps engineers optimize seal geometry and material selection, preemptively addressing potential failure points.
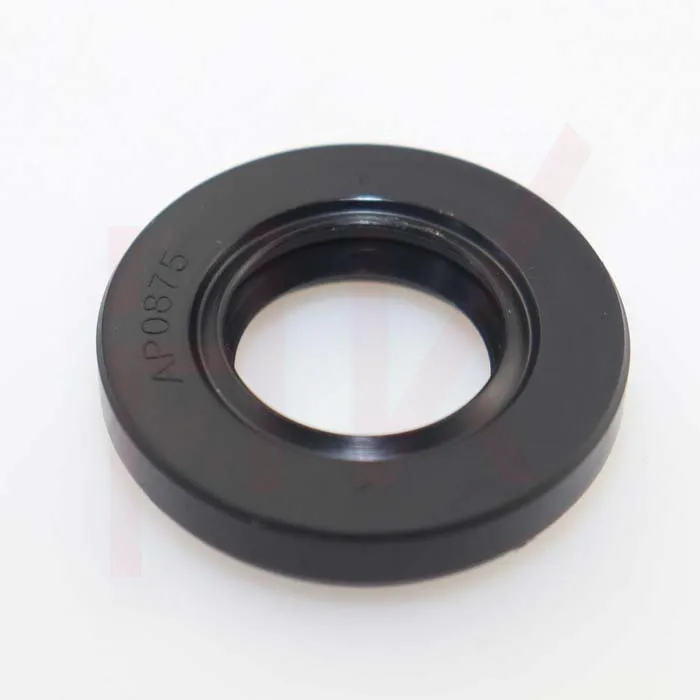
In practice,
high-pressure seal performance must be evaluated through rigorous testing. Hydrostatic and pneumatic testing are standard procedures wherein seals are subjected to pressures beyond their operational limits to ensure reliability in real-world conditions. Such tests are vital for components used in safety-critical sectors, such as aerospace, where seal failures could endanger lives. Real-world application brings additional challenges, such as abrasive wear and thermal cycling, underscoring the necessity for ongoing maintenance and periodic inspection.
high pressure seal
Professionals working with high-pressure seals often emphasize the importance of proper installation techniques. Misalignment during installation can lead to premature seal failure, drastically reducing service life and efficiency. Experts recommend adherence to manufacturer guidelines and the use of specialized tools and equipment to ensure precision. Furthermore, engaging experienced technicians for installation and commissioning can significantly enhance the operational lifespan of high-pressure seals.
As technology evolves, so too does the manufacture and application of high-pressure seals. Innovations such as additive manufacturing and the development of nanomaterials are paving the way for next-generation seals with enhanced performance characteristics. These advancements promise even greater efficiencies and the ability to withstand harsher environments, further cementing the role of high-pressure seals in industrial applications.
Selecting the right high-pressure seal is crucial and should be guided by thorough technical consultation. Factors such as compatibility with the working fluid, pressure and temperature ratings, and environmental conditions must be meticulously evaluated. Consulting with manufacturers and industry experts can facilitate the decision-making process, ensuring that the seal chosen meets the specific demands of the application.
In conclusion, high-pressure seals are vital to the integrity of numerous industrial operations. Their design and selection require a deep understanding of material science and engineering principles, reinforced by real-world application knowledge. Ensuring their optimal functionality involves both innovative design and adept installation, supported by regular maintenance and technological advancements. With these considerations, high-pressure seals will continue to serve as critical enablers of industrial efficiency and safety.