In the intricate machinery of vehicles and industrial applications, the oil seal hub stands as an unsung hero, ensuring the seamless operation and longevity of equipment. These components, though small, play a crucial role in maintaining the integrity of the systems in which they are installed.
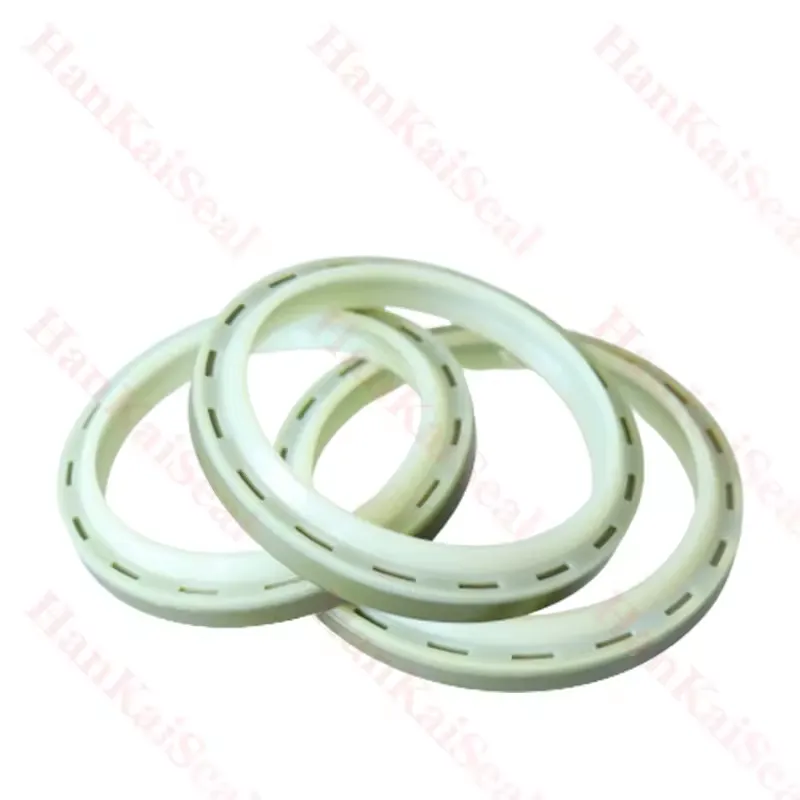
The oil seal hub is designed to protect the bearing and other internal components from contamination and prevent the leakage of lubricants. It acts as a barrier between the rotating and stationary components of machinery, effectively sealing the passage of fluids. These seals are crafted from durable materials, often comprising nitrile rubber, silicone, or fluoropolymer, each selected based on the specific operational environment.
When discussing the expertise in manufacturing oil seal hubs, attention to detail is paramount. Precision engineering ensures that the seal fits perfectly within the designated hub, with the correct tension to withstand varying temperatures and pressures. The process of designing an oil seal hub is both an art and a science, requiring a deep understanding of mechanical systems and fluid dynamics. Qualitative assessment methods, such as Finite Element Analysis (FEA), are frequently employed to predict the performance and longevity of these components under different environmental conditions.
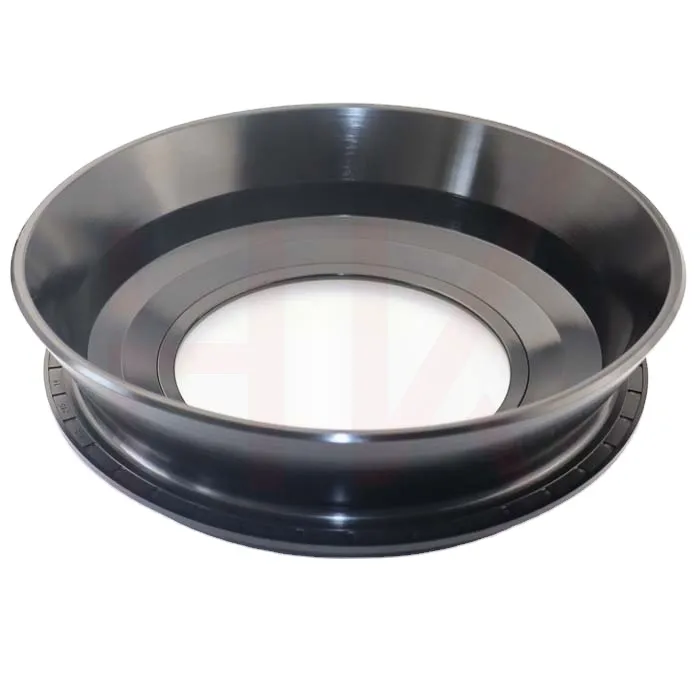
Real-world experience highlights the importance of selecting the right oil seal hub for specific applications. In automotive industries, for instance, the choice of seal can significantly affect vehicle performance. High-quality seals contribute to reducing friction and wear, leading to lower maintenance costs and improved fuel efficiency. Conversely, subpar seals can lead to premature failure, resulting in costly repairs and downtime.
oil seal hub
In the realm of industrial machinery, where downtime can equate to thousands of lost dollars per hour, the reliability of oil seal hubs becomes even more critical. Industries such as petrochemicals, aerospace, and heavy machinery demand seals that can cope with extreme conditions, including high pressure, aggressive chemicals, and temperature fluctuations. Therefore, manufacturers often subject oil seal hubs to rigorous testing to ensure they meet stringent safety and performance standards.
Trustworthiness is built by consistently delivering products that perform as promised. Companies with established reputations in producing oil seal hubs invest heavily in research and development.
This focus not only enhances product quality but also fosters innovation. For instance, recent advancements have seen the emergence of smart seals equipped with sensors to provide real-time data on seal performance, further minimizing the risk of unexpected failures.
Additionally, authoritative entities in the industry, such as certification bodies, play a role in validating the quality and performance of oil seal hubs. Compliance with standards set by these organizations is crucial for assuring customers of the seal's reliability and durability.
In conclusion, the oil seal hub, despite its seemingly modest role, is essential for the optimized functioning of both simple and complex systems. Its design and performance are the result of meticulous engineering, thorough testing, and continuous innovation. By selecting superior oil seal hubs, companies and individuals can enhance the efficiency and reliability of their machinery, ultimately safeguarding their investments and operations. The commitment to quality, backed by experience, expertise, authority, and trust, underpins the success of those manufacturers who lead the field in oil seal technology.