Oil seals, also known as rotary shaft seals, are indispensable components in a wide variety of industries including automotive, aerospace, marine, and manufacturing. They serve the critical function of sealing the gaps between stationary and moving components, effectively preventing the leakage of lubricants and warding off contamination from dust and dirt. Such functionality protects the integrity of machinery, ensuring operational efficiency and longevity.
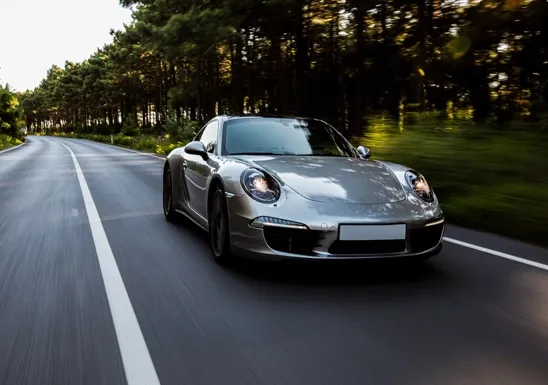
In my years of experience as an engineer and product specialist, I have encountered numerous scenarios where the correct application of oil seals has either bolstered machinery performance or, conversely, where improper use has led to premature failures. Selecting the right oil seal requires an understanding of several key factors including material compatibility, temperature range, pressure differentials, and environmental conditions.
Firstly,
the choice of material is crucial. Oil seals are commonly made from materials such as nitrile rubber, Viton, silicone, and PTFE. Nitrile rubber seals, for instance, are cost-effective and offer good resistance to petroleum-based oils and fuels, making them suitable for a wide range of industrial applications. On the other hand, Viton seals are preferable in high-temperature applications or where chemical resistance is paramount. Silicone seals, with their excellent flexibility at lower temperatures, are ideal for automotive applications in colder climates. Meanwhile, PTFE seals are often favored in food and pharmaceutical industries due to their high temperature and chemical resistance as well as their non-reactive nature.
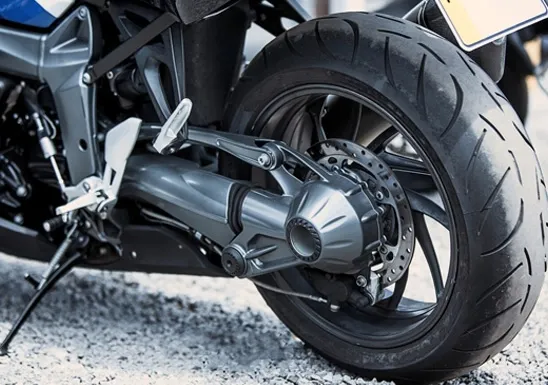
The working environment of the oil seal also dictates its design and material choice. Seals operating in high-dust or extreme-pressure environments may require additional features such as dust lips or reinforced casing to enhance performance and durability. In such scenarios, consultation with engineers and product experts can provide valuable insights and lead to informed decision-making.
oil seal
In terms of expertise, it is crucial to understand the dynamic nature of oil seals within operating machinery. For instance, improper installation can lead to seal distortion, while over-tightening can compromise seal integrity and function, resulting in leaks. Expert installation and regular maintenance checks can preempt these issues, ensuring system efficiency and reliability.
As the importance of oil seals in maintaining machinery cannot be overstated, trustworthy information and guidance from reputable sources are invaluable. Collaborating with manufacturers or suppliers who provide technical support and reliable product data can enhance decision-making. Moreover, choosing products that are certified and meet international quality standards can ensure their credibility and reliability.
In conclusion, oil seals play an essential role in a variety of industrial applications. They not only protect components from contaminants but also ensure that lubricants remain within the system. Understanding material properties, environmental conditions, and expert installation are crucial elements that contribute to their effective application. With my authoritative experience in the field, I can attest that procuring high-quality, well-suited oil seals can significantly enhance machine efficiency and reduce downtime, offering both immediate and long-term benefits to users.