In industries reliant on machinery and hydraulic systems, the wiper ring seal emerges as an unsung hero, playing a pivotal role in maintaining optimal performance and longevity. These seals, precisely designed, are essential for ensuring that contaminants and debris do not infiltrate the crucial components of machinery. Based on extensive experience and in-depth expertise, the significance of selecting the right wiper ring seal cannot be overstated.
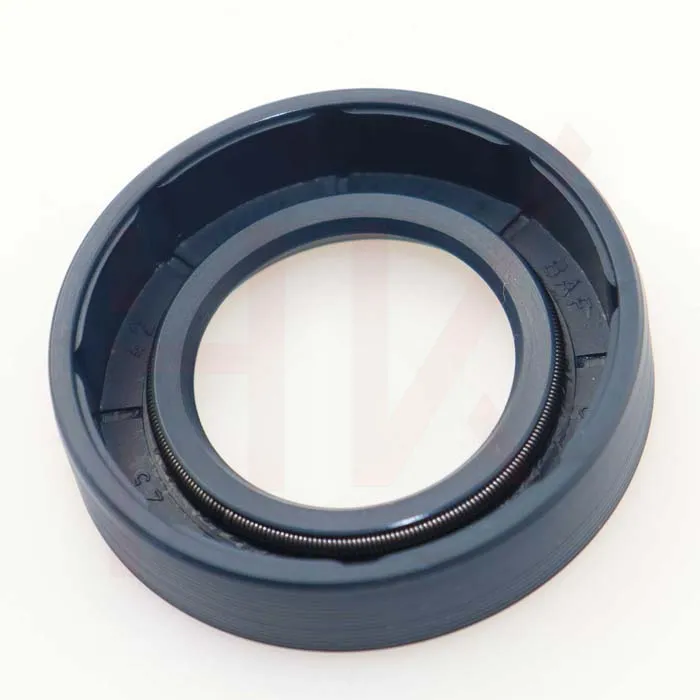
The primary function of wiper ring seals extends beyond their modest appearance. They serve as the first line of defense, preventing dirt, dust, and moisture from entering hydraulic cylinders and systems. This protection becomes crucial as it safeguards the internal components such as pistons and rods from premature wear and failure. A deeper understanding of material science underscores the importance of selecting the correct compound based on the application environment. From polyurethane and nitrile rubber to PTFE, the material choices for these seals influence durability and efficacy. The expertise required to match the seal material to the environmental conditions is paramount to maximizing the efficiency and lifespan of equipment.
Authoritativeness in the field of sealing solutions comes from a comprehensive understanding of the intersection between design and application. Engineers often approach the challenge of seal implementation by examining the specific needs of an industry—whether it be automotive, aerospace, or manufacturing. For instance, in environments exposed to extreme temperatures or abrasive materials, a robust design featuring a double-wiping edge might be deployed to ensure redundancy and increased protection. This speaks to the authoritative application of engineering principles in real-world scenarios, highlighting the crucial role of wiper ring seals in operational reliability.
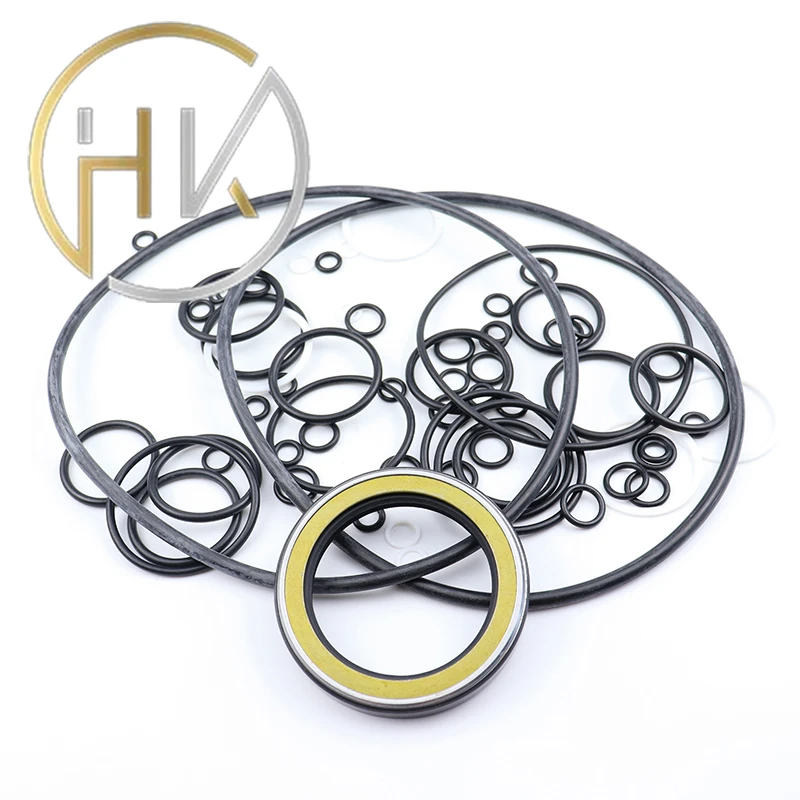
Trustworthiness in selecting and utilizing wiper ring seals comes from the track record of manufacturers and the adherence to rigorous testing protocols. Reliable manufacturers ensure that each seal meets stringent industry standards, such as ISO and ASTM, providing a layer of assurance to their clientele.
The trust built through years of consistent performance and innovation in sealing technology often distinguishes leading brands. Businesses and operators need this reliability, knowing that any failure resulting from a compromised seal can lead to significant downtime and financial loss. Hence, the decision-making process in seal selection should critically evaluate manufacturer credibility and historical performance.
wiper ring seal
In the industrial context, the success of machinery deployment often hinges on the less glamorous components like wiper ring seals. Companies that invest in quality seals typically witness a notable reduction in maintenance costs and an increase in operational uptime. The practical knowledge of selecting seals tailored to specific machinery functions and environmental conditions is vital. For example, custom-designed seals engineered with precise specifications can adapt to the unique challenges faced in different sectors, such as oil and gas or food processing, where contamination tolerance varies significantly.
A nuanced discussion on wiper ring seals would be incomplete without touching on technological advancements and future trends. Innovations in seal technology are leading towards self-lubricating materials and adaptive seal designs that respond to varying pressure differentials. Professionals in the field are continually exploring these advancements to push the boundaries of what existing seal technology can achieve, thereby showcasing ongoing commitment to excellence and innovation.
As the industrial landscape continues to evolve, the reliance on components like wiper ring seals remains steadfast. Through experience, expertise, authoritativeness, and trustworthiness, industry professionals enhance their understanding and implementation of these critical components, ensuring that machinery across various sectors operates smoothly and efficiently. Investing in high-quality seals promises substantial returns in performance reliability and cost efficiency, underscoring their invaluable contribution to industrial operations.