Oil seals, often unheralded but highly crucial, underpin the integrity and efficiency of a myriad of mechanical systems spanning diverse industries. The multifaceted roles of these components cannot be overstated, particularly given their primary function of sealing parts and safeguarding devices from contamination and premature wear. With over two decades immersed in the field of mechanical engineering and product development, I'll delve into the nuanced application, selection, and maintenance of oil seals, tailoring insights to bolster both expertise and decision-making.
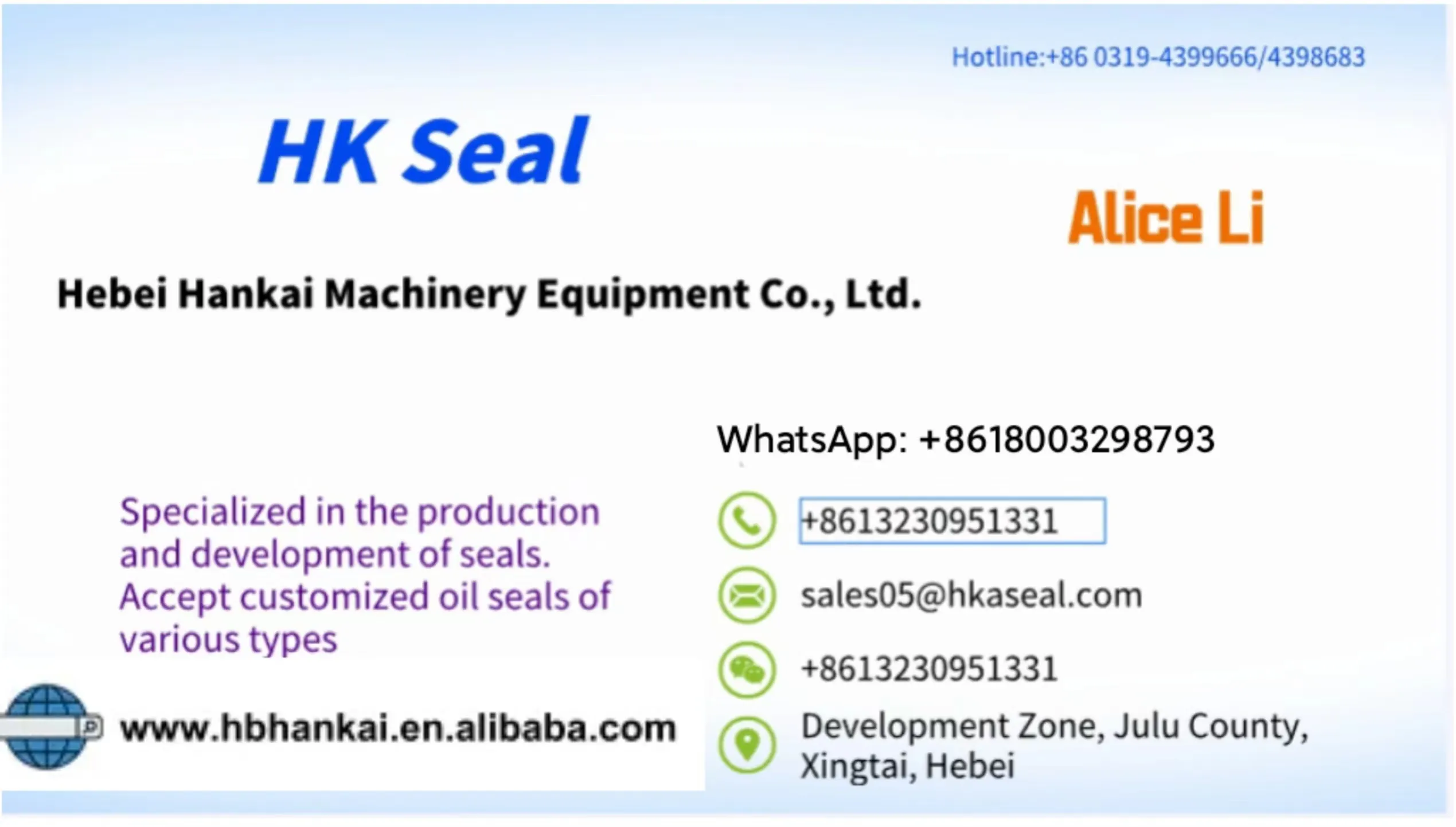
The pivotal role of oil seals in operational longevity lies in their ability to confine lubricants within equipment compartments while simultaneously preventing the ingress of dust, dirt, and moisture. These seals are integral in machinery across automotive, manufacturing, and even aerospace industries. For instance, automotive engines rely on oil seals to enclose motor oil while hindering dirt from entering the combustion engine, which significantly reduces the risk of contamination and friction-related damages. In an industrial context, hydraulic systems utilize oil seals to prevent the leakage of hydraulic fluid, ensuring non-stop, efficient production cycles.
Selecting the appropriate oil seal is a decisive factor that determines the efficacy and service life of mechanical systems. The choice hinges on understanding four critical parameters material compatibility, temperature range, pressure endurance, and shaft speed. For example, in high-temperature environments, seals manufactured from silicone or fluorocarbon rubber are preferred due to their superior heat resistance.
Conversely, in colder conditions, nitrile rubber may offer optimal performance. My experience suggests that underestimating shaft speed can lead to rapid degradation of the seal's lip, thus amplifying the need for precision in matching the seal type to the operational requirements.
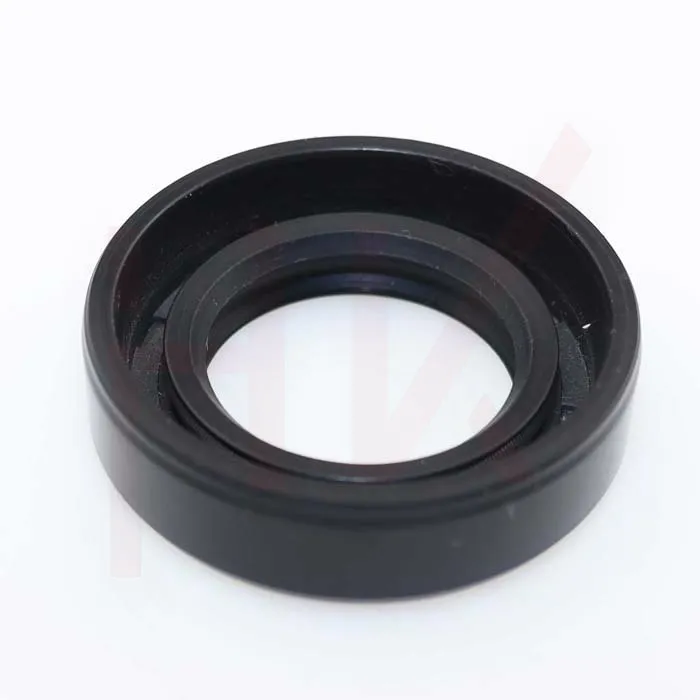
Expertise in this domain also demands a comprehension of various oil seal designs, such as single lip, dual lip, and combination seals, each serving distinct mechanical functions. Single lip seals are generally suited for low-pressure scenarios, offering basic sealing performance; dual lip seals, however, include an auxiliary lip that provides enhanced contamination protection, while combination seals integrate a dust lip, and are invaluable in vigorously dusty environments — a vital component for off-road vehicles and agricultural machinery.
oil seals
Achievement of authoritative knowledge in oil seals is further cemented by recognizing the signs of wear and implementing a proactive maintenance regime. Regular inspection for signs of leakage, vibration, or unusual noises can preempt catastrophic failures. Adopting a comprehensive maintenance schedule, which includes periodic replacement and allowing assessment by professionals, is essential. My professional circle commonly advocates for the use of condition monitoring technologies that enable predictive analysis, thus extending seal longevity and optimizing system reliability.
Despite the intricate nature of oil seals, fostering trust and reliability in mechanical operations begins with informed product choices and meticulous application. Expectations for oil seal performance continuously rise as industries evolve, demanding that seals are not only reliable but also environmentally sustainable. Adopting materials with lower environmental impact and ensuring rigorous adherence to international standards stands as a testament to industry-leading practices.
In conclusion, oil seals serve as the unsung protectors within myriad mechanical assemblies, demanding attention to detail from selection through to maintenance. As industries pivot towards more sustainable and efficient practices, oil seals will undoubtedly continue to play a cardinal role. Sharing insights gained from practical experience and research advances our collective understanding, fortifying oil seal utility across both renewed and novel applications. Leveraging such knowledge ensures not only the longevity and reliability of industrial operations but also underscores a commitment to engineering excellence and ecological stewardship.